Operations Management - Operations Management Insight
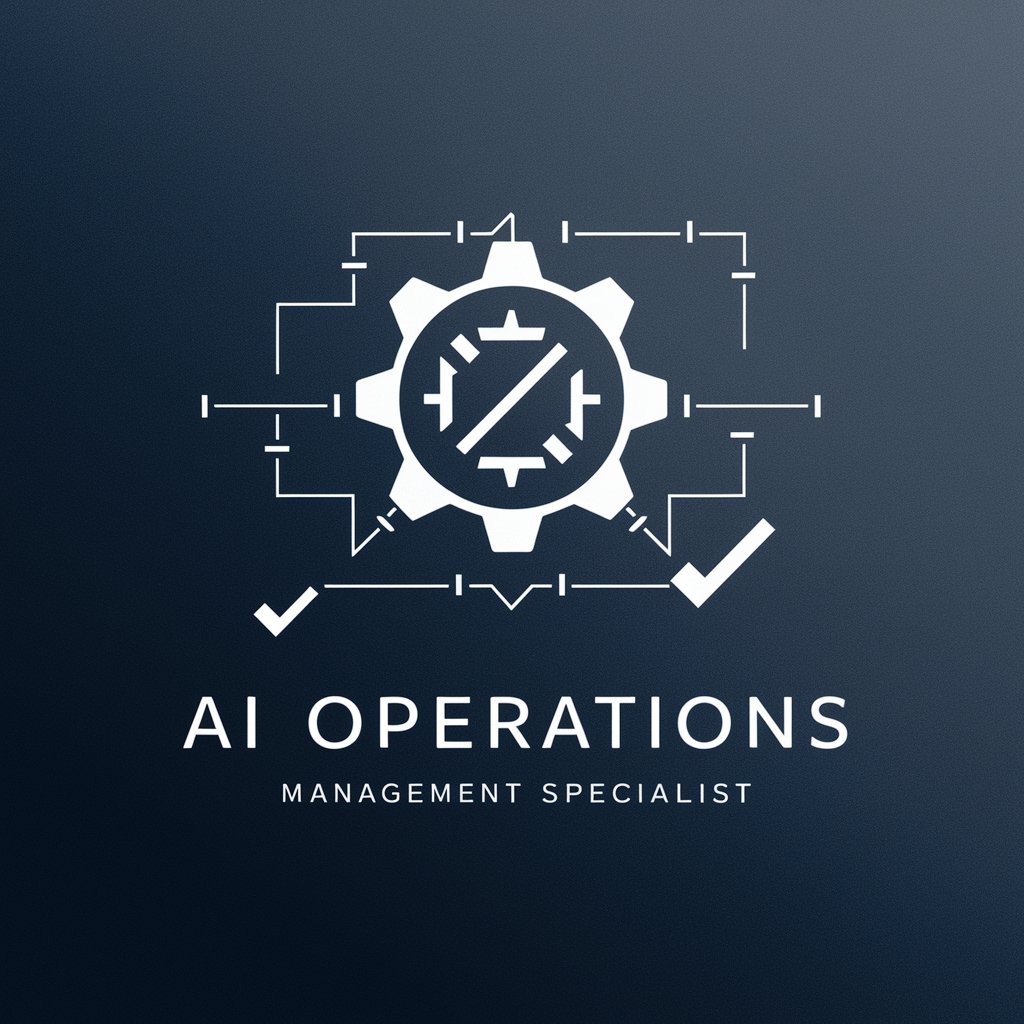
Welcome! Let's optimize your operations for peak efficiency.
Streamline Operations with AI
What are the best practices for improving workflow efficiency in manufacturing?
How can I optimize my supply chain to reduce costs and increase efficiency?
What strategies can be implemented for effective inventory management?
How can quality control processes be enhanced to ensure product consistency?
Get Embed Code
Introduction to Operations Management
Operations Management (OM) is a critical area of management focused on overseeing, designing, and controlling the process of production and redesigning business operations in the production of goods or services. Its primary aim is to ensure that business operations are efficient in terms of using as few resources as needed, and effective in terms of meeting customer requirements. It involves the responsibility of ensuring that business operations are efficient in terms of using as little resource as possible while being effective in meeting customer demands. For example, in a manufacturing setup, OM oversees the transformation of raw materials into finished products through efficient process design, operation, and supply chain management. In a service-oriented company, OM might involve managing the process that converts inputs (like knowledge, skills) into outputs (services) that offer value to customers. Scenarios illustrating OM include streamlining operations in a car manufacturing plant to reduce waste and increase productivity, or optimizing the scheduling system in a hospital to improve patient care and reduce wait times. Powered by ChatGPT-4o。
Main Functions of Operations Management
Supply Chain Management
Example
Coordinating with suppliers to ensure timely delivery of materials
Scenario
A furniture manufacturing company uses OM to manage its supply chain, ensuring that wood and hardware are delivered on schedule to meet production deadlines, optimizing inventory levels, and reducing storage costs.
Quality Control
Example
Implementing quality assurance processes to meet customer expectations
Scenario
A software development firm applies OM principles to maintain high-quality standards, using systematic testing procedures to identify bugs before product release, ensuring customer satisfaction and loyalty.
Inventory Management
Example
Using just-in-time inventory systems to reduce holding costs
Scenario
A retail chain employs OM techniques to manage its inventory efficiently, minimizing overstock and understock situations by adjusting orders based on real-time sales data, thereby reducing waste and increasing profitability.
Process Improvement
Example
Applying lean manufacturing principles to enhance efficiency
Scenario
A food processing company leverages OM to streamline its operations, reducing process steps and eliminating non-value-added activities, resulting in faster production times and lower production costs.
Ideal Users of Operations Management Services
Manufacturing Firms
These businesses benefit from OM in optimizing production processes, improving product quality, and managing supply chains, leading to enhanced efficiency and reduced costs.
Service Providers
Service-oriented companies, including healthcare, banking, and logistics, use OM to streamline operations, improve service delivery, and enhance customer satisfaction through efficient process management.
Retail and E-commerce
Retailers and online stores utilize OM for inventory management, ensuring the right products are available at the right time, optimizing the supply chain, and enhancing the customer shopping experience.
Small and Medium Enterprises (SMEs)
SMEs leverage OM to find efficient ways of operating within limited resources, focusing on process improvements and efficient resource use to scale operations and compete effectively in their markets.
How to Utilize Operations Management
Start Your Journey
Begin by visiting a platform offering a comprehensive Operations Management tool for a hassle-free trial, no login or ChatGPT Plus required.
Identify Your Needs
Assess your organization's operations to identify inefficiencies, bottlenecks, or areas for improvement. Common use cases include streamlining supply chains, enhancing quality control, and optimizing inventory management.
Customize Your Approach
Leverage the tool to tailor solutions specific to your operations' challenges. Utilize features like workflow analysis, process mapping, and efficiency metrics to drive improvements.
Implement Changes
Apply the insights and recommendations from the tool to your operations. Focus on areas with the highest potential impact, and consider pilot projects to test new processes or technologies.
Monitor and Adjust
Regularly review performance data to monitor the effectiveness of implemented changes. Use this feedback to make ongoing adjustments, ensuring continuous improvement in your operations.
Try other advanced and practical GPTs
Hotel Management
Enhancing Hospitality with AI Expertise
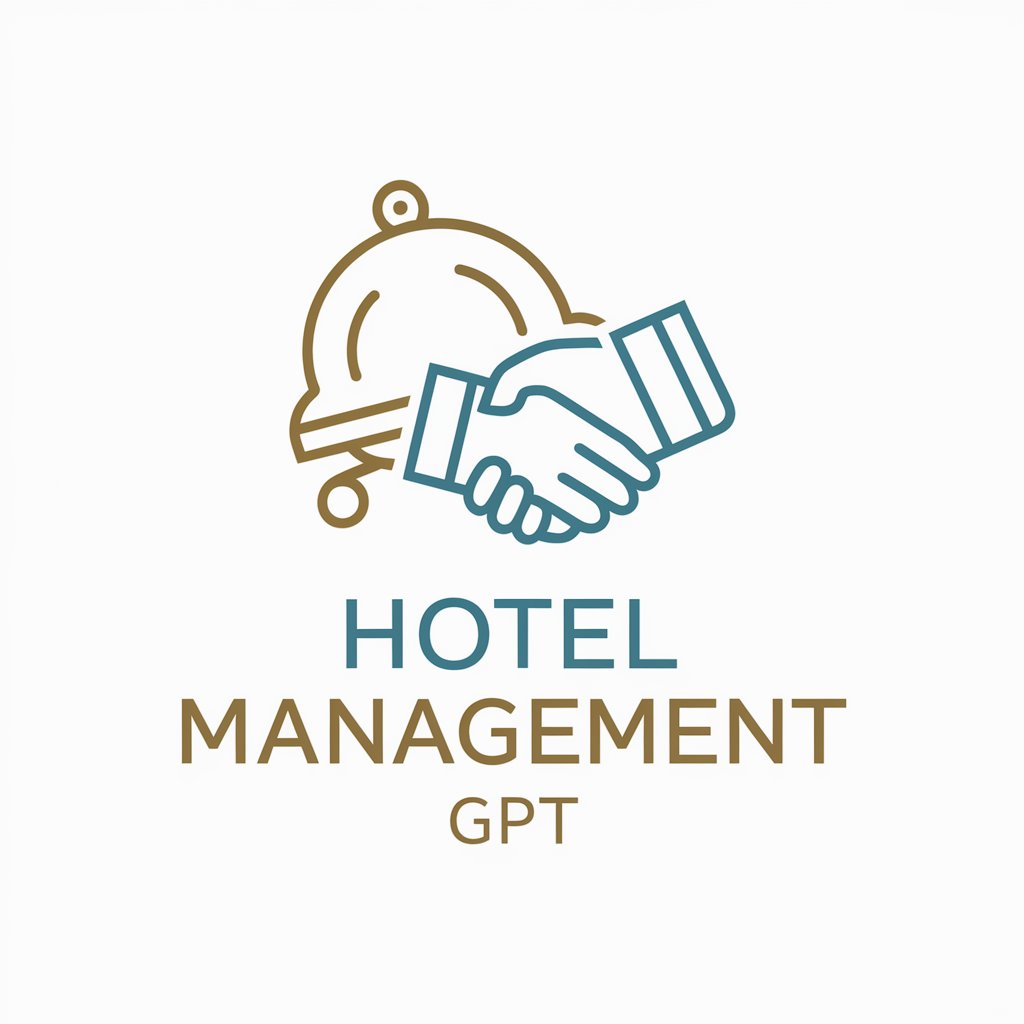
FFA GENIE
Empowering Insurance Agents with AI
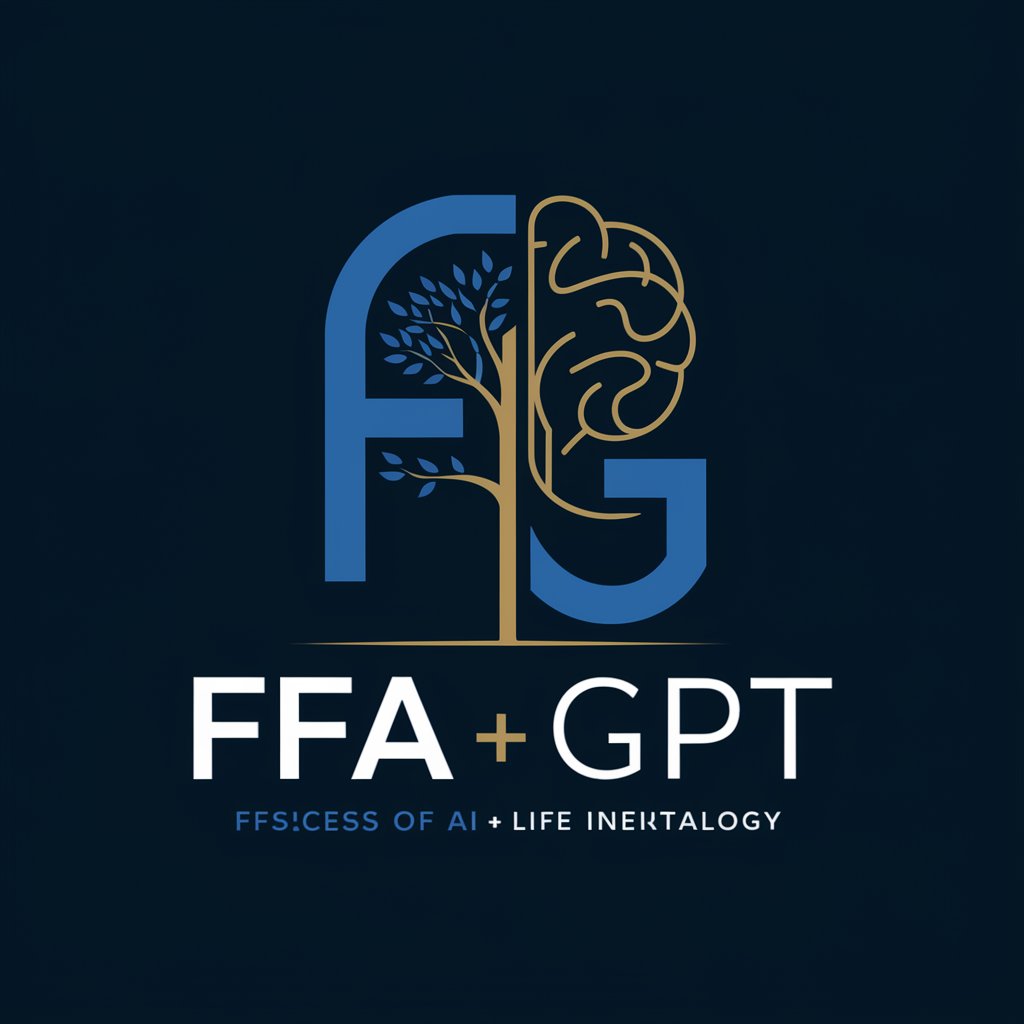
SOC
Empowering Cybersecurity with AI
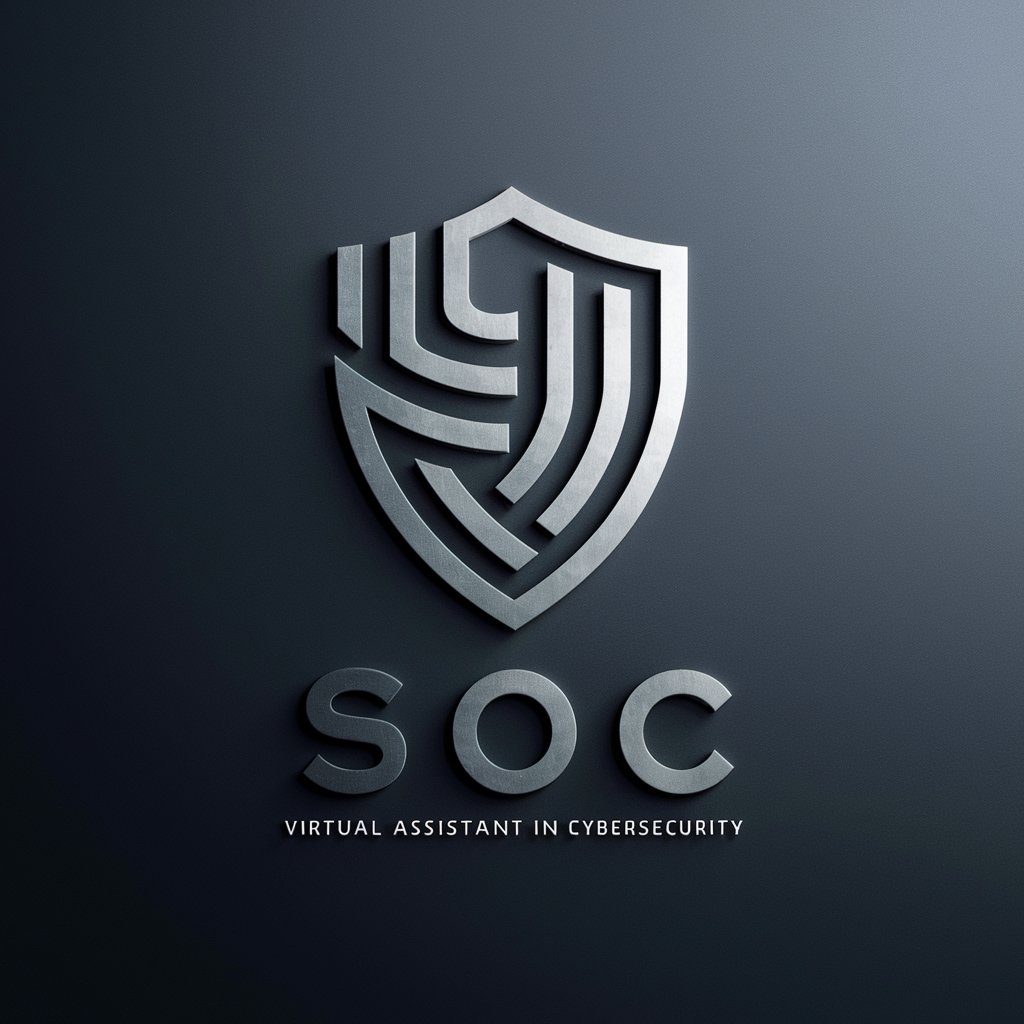
Agribusiness
Empowering Agribusiness with AI
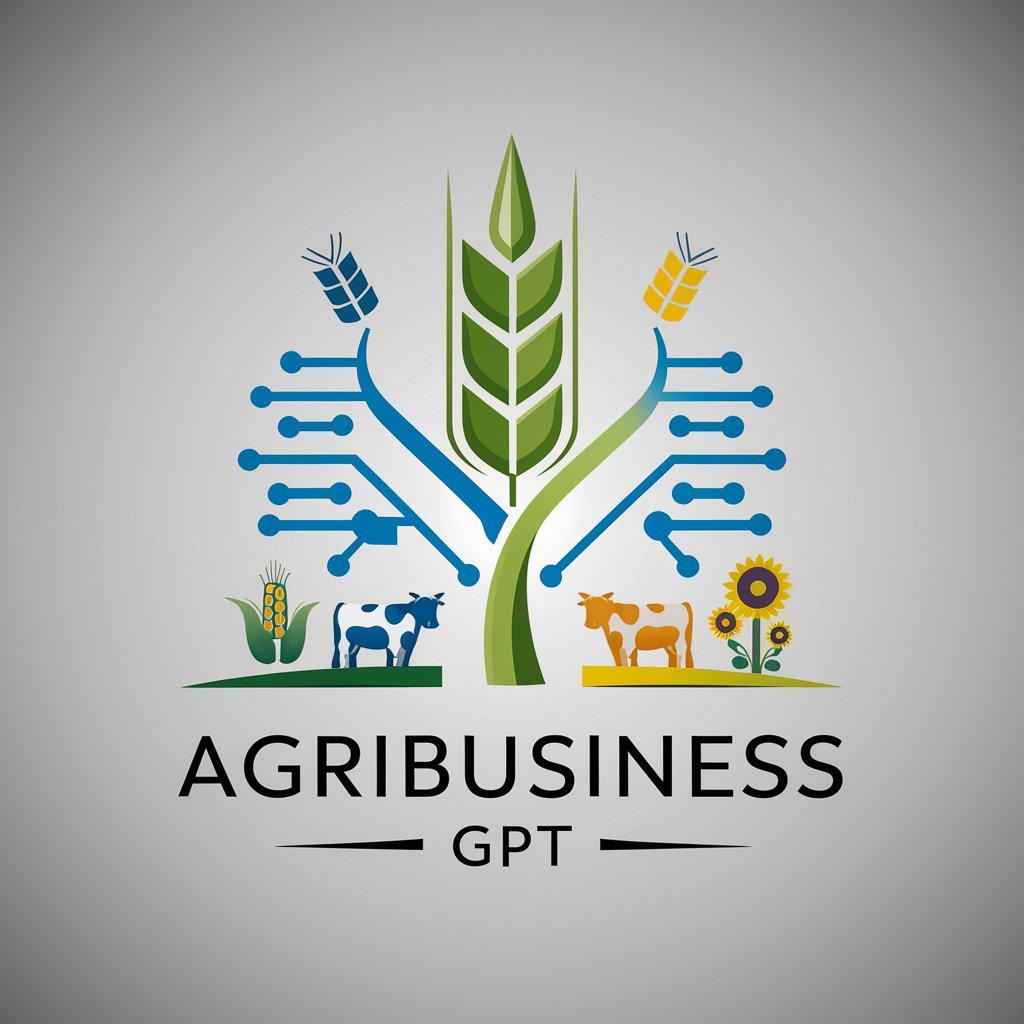
Operations Safety
Empowering Safe Operations with AI
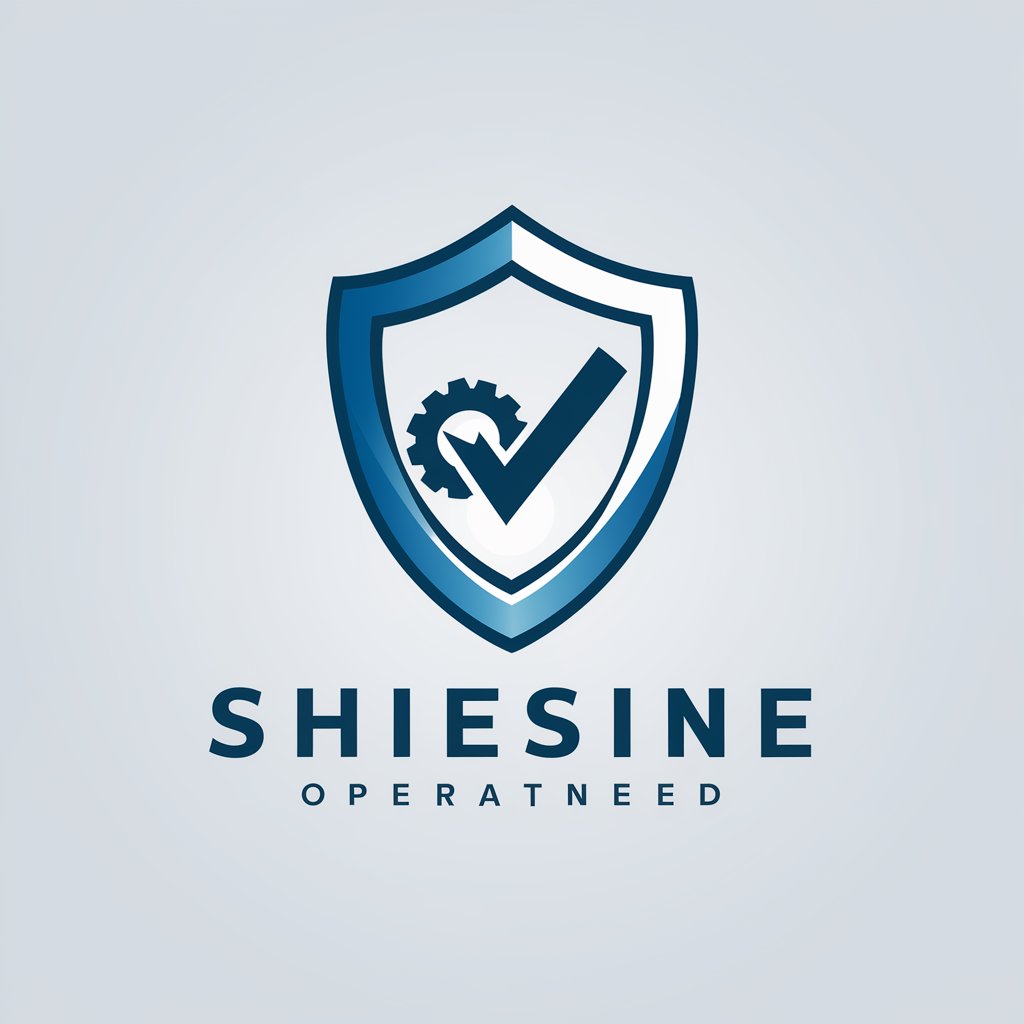
Hero Image Creator
Craft stunning hero images with AI
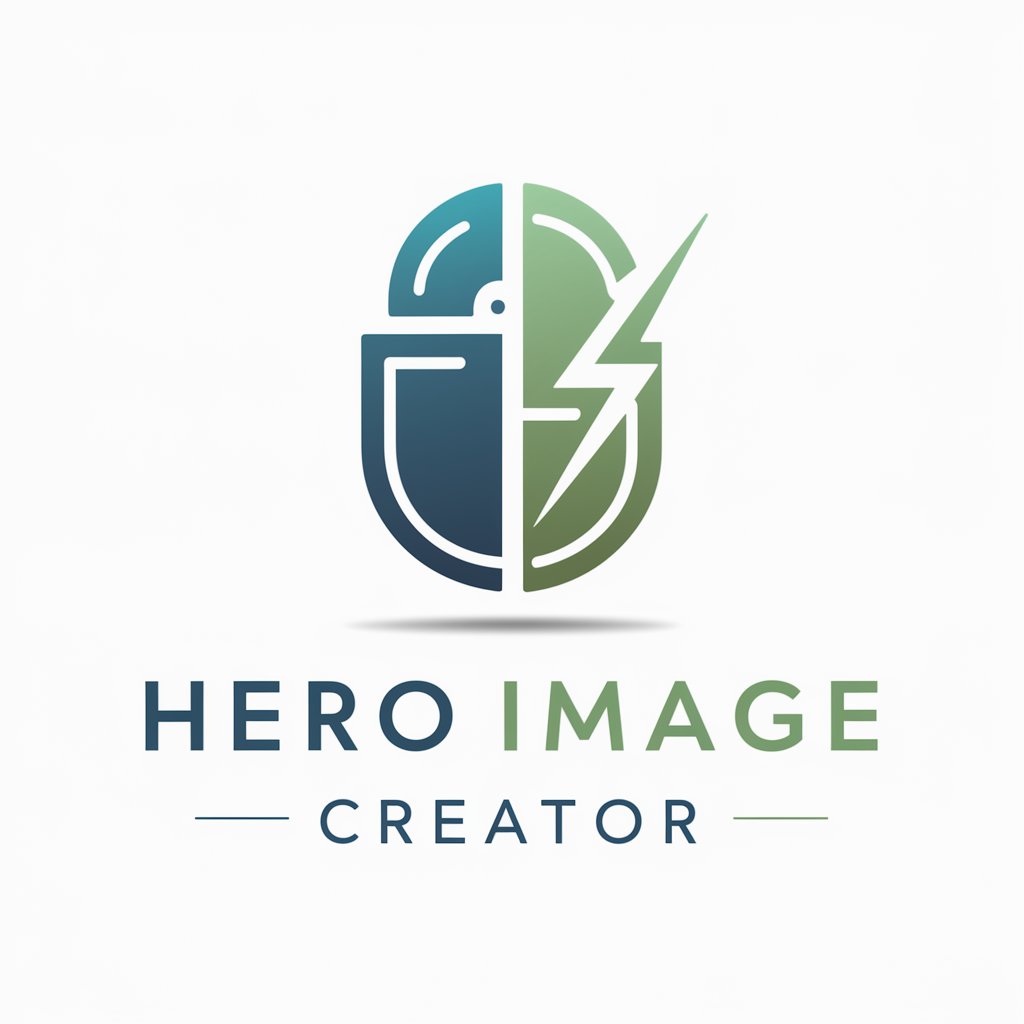
Fast Loan
Instant financial solutions, powered by AI

OPEX 1.0 by Umar Ibrahim
Empower operations with AI-driven insights
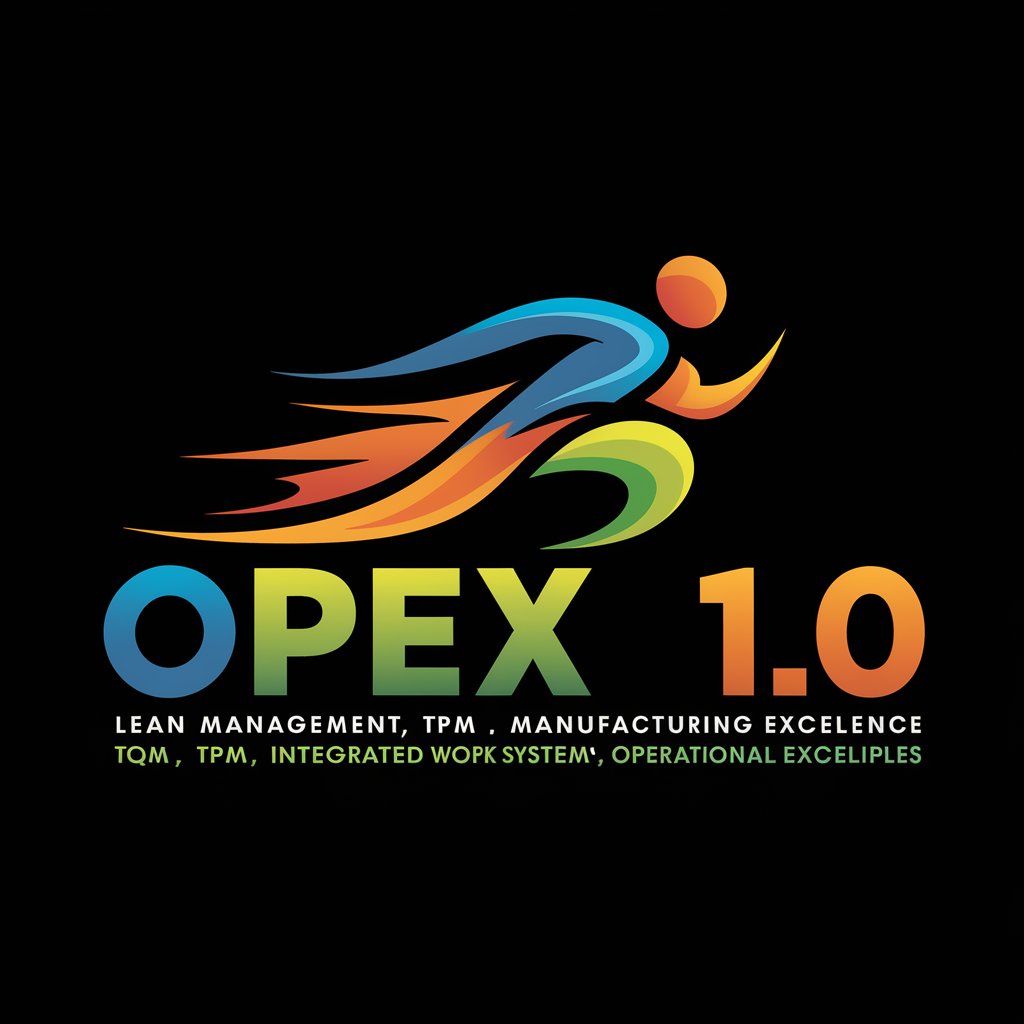
Gun Shop
Navigate Firearm Laws with AI
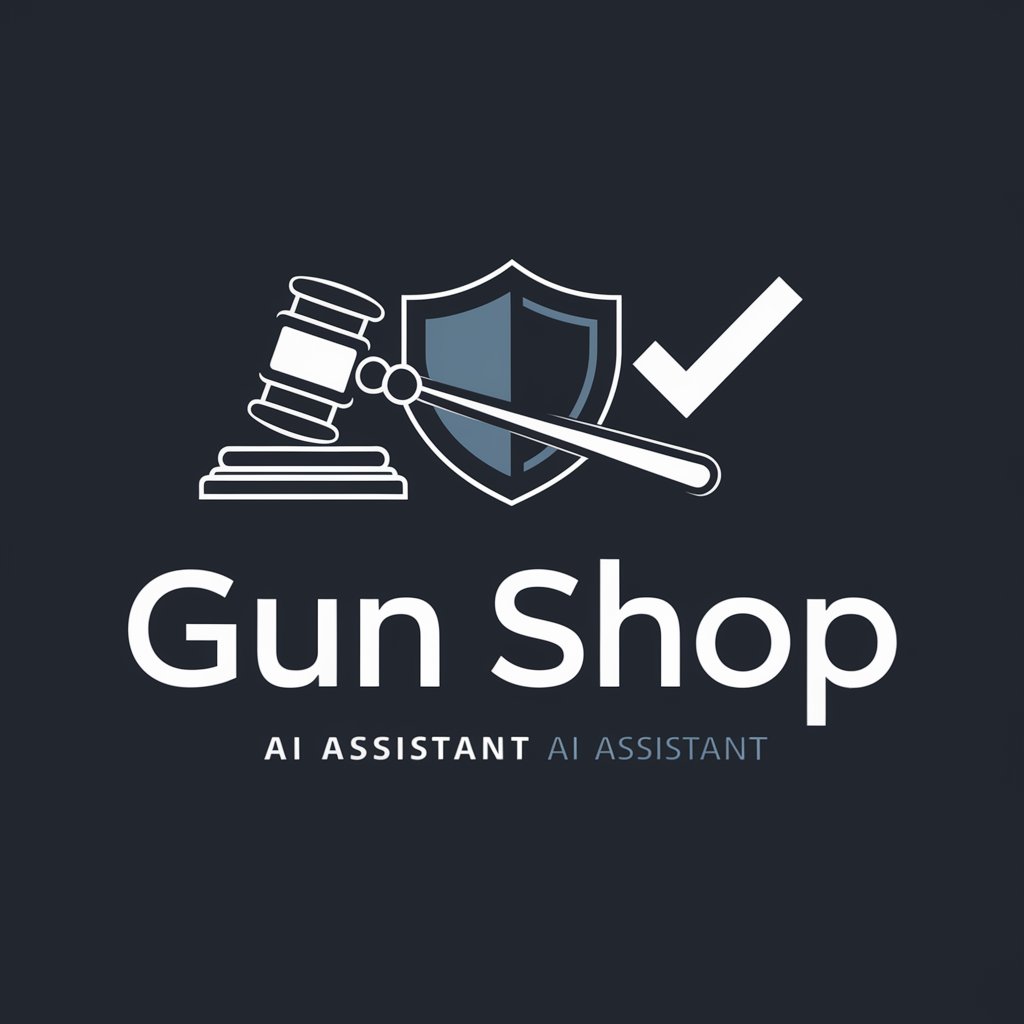
Small Business Operations
Empowering businesses with AI-driven insights
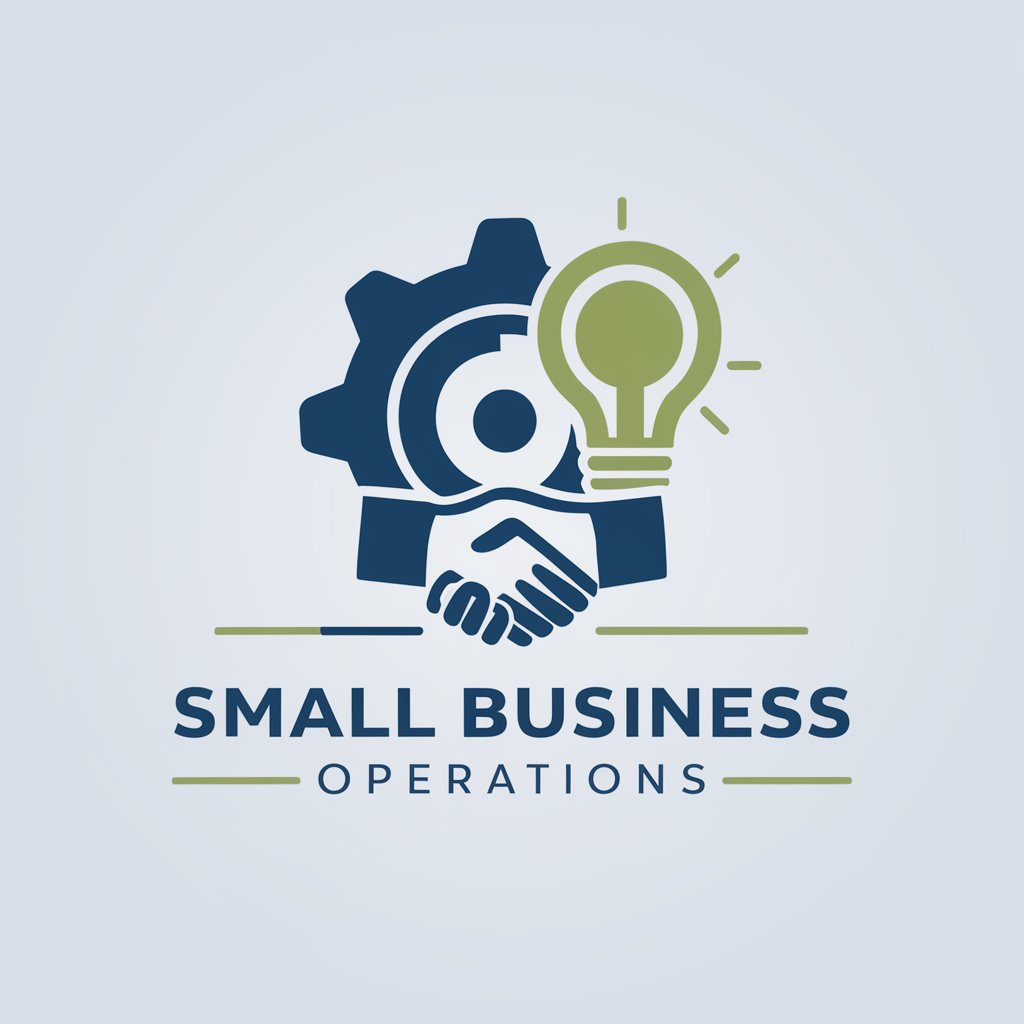
LPL Financial Operations Guide
Streamlining Financial Advisory with AI
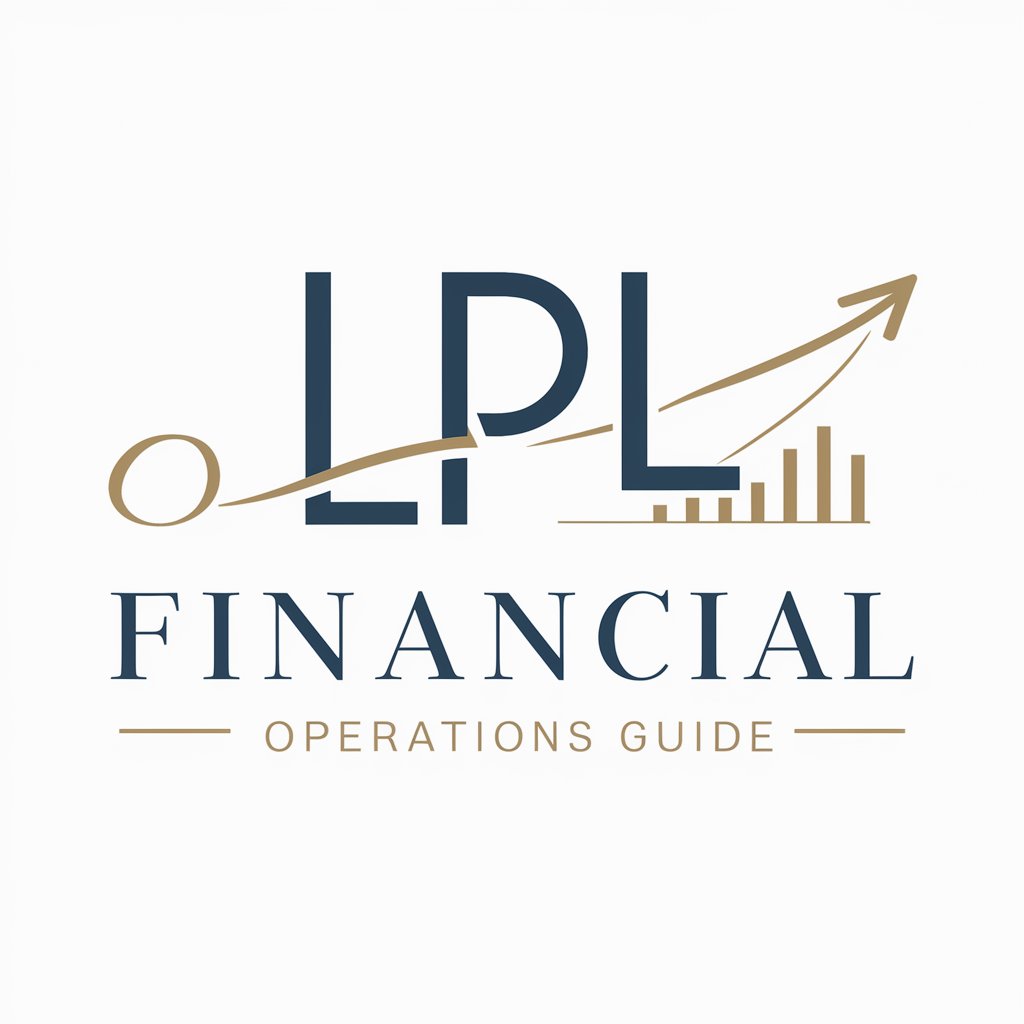
BDRGPT
AI-powered Executive Outreach Made Simple
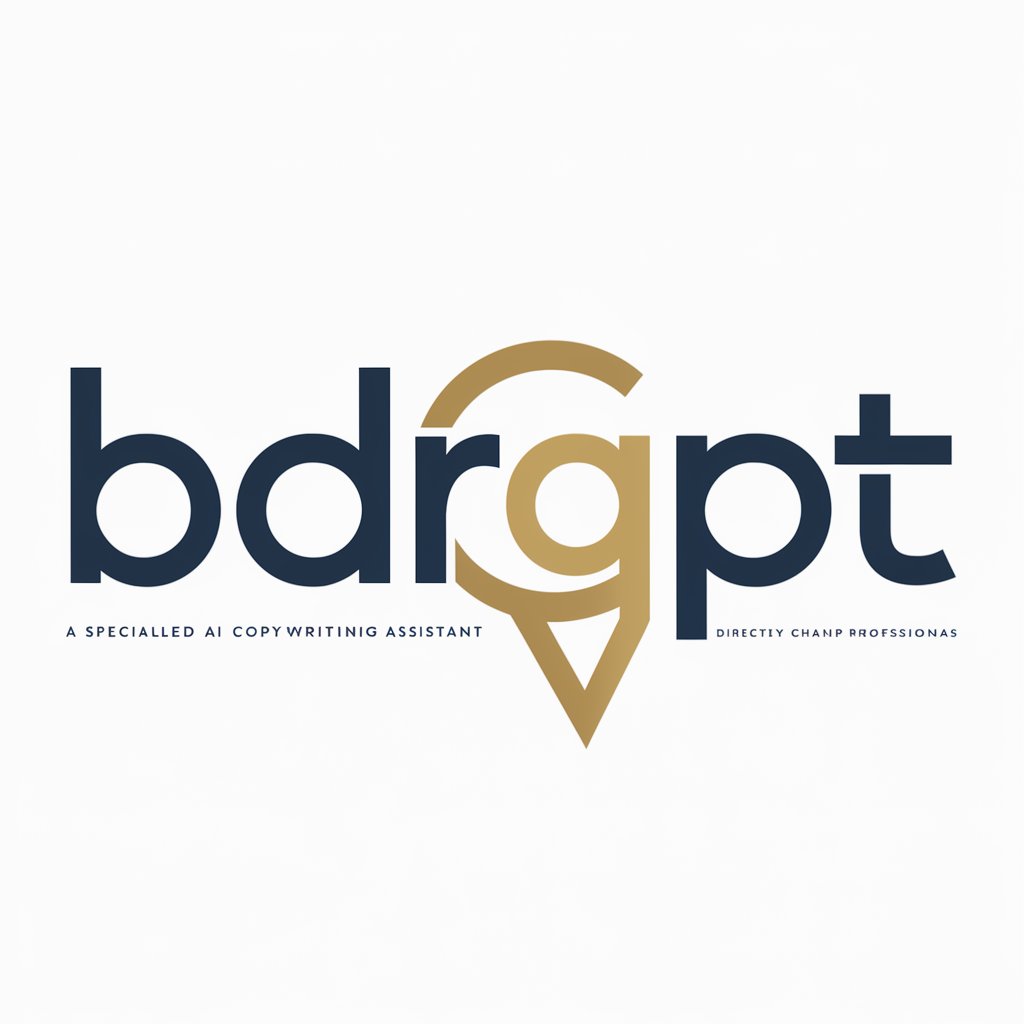
In-Depth Q&A on Operations Management
What is Operations Management?
Operations Management involves overseeing, designing, and controlling the process of production and redesigning business operations in the production of goods or services. It ensures that business operations are efficient in terms of using as little resource as needed, and effective in terms of meeting customer requirements.
How can Operations Management improve efficiency?
It improves efficiency by optimizing the workflow and processes, reducing waste, and enhancing productivity. Techniques such as lean manufacturing, Six Sigma, and process reengineering are often applied to achieve these goals.
Can Operations Management help in reducing operational costs?
Yes, by streamlining processes, improving supply chain management, and minimizing waste, Operations Management can significantly reduce operational costs. It focuses on making the operations more efficient, which directly contributes to lowering expenses.
How does Operations Management contribute to customer satisfaction?
It enhances customer satisfaction by ensuring that the production process is as efficient and effective as possible, leading to higher quality products and services, faster delivery times, and improved reliability, all of which contribute to a better customer experience.
What role does technology play in Operations Management?
Technology plays a crucial role in Operations Management by providing tools and systems for process automation, data analysis, and real-time monitoring of operations. This enables more informed decision-making, improves efficiency, and facilitates innovation in processes and products.