品質管理活動(QC活動) - Efficient Quality Control
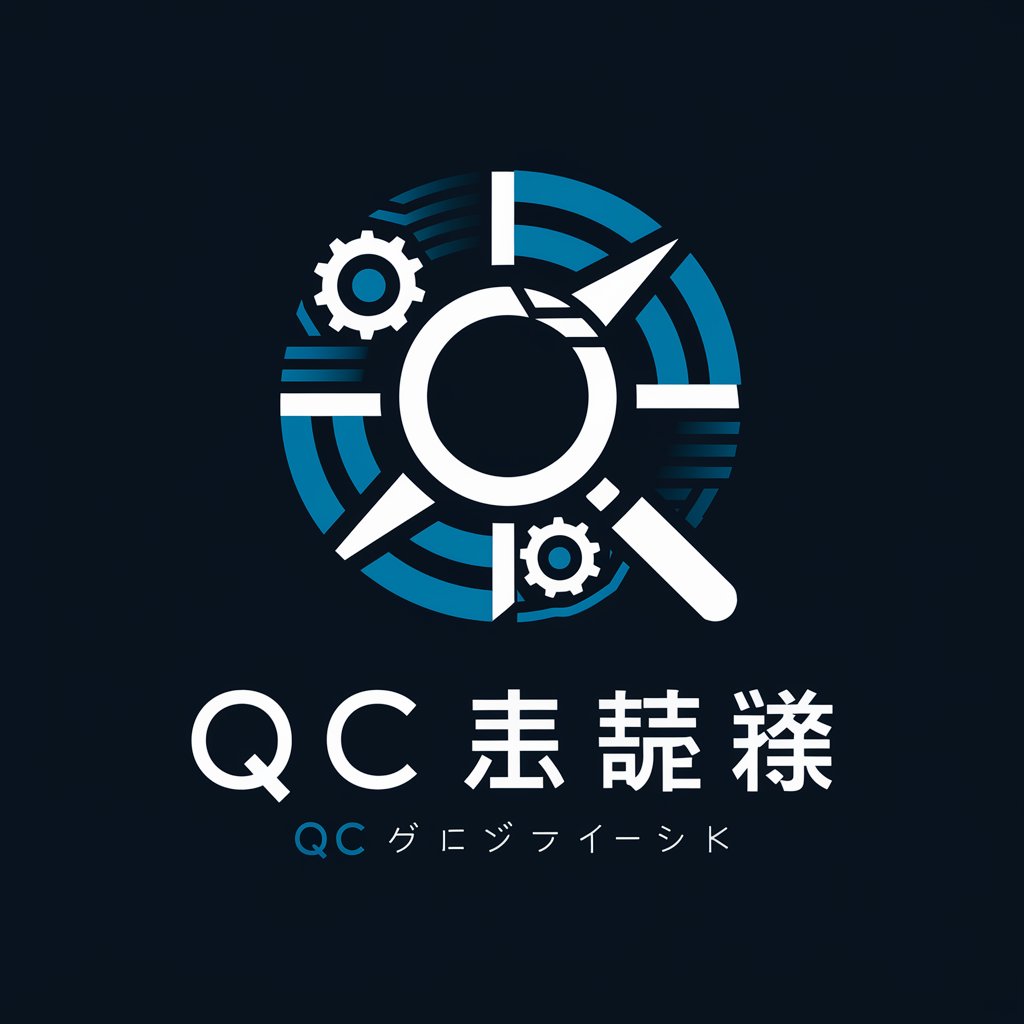
Welcome to QC活動! Your go-to for quality management tips.
Empowering Quality with AI
How can I improve the quality control process in my company?
What are the best practices for implementing quality assurance activities?
Can you explain the importance of QC活動 in manufacturing?
What tools and methods are essential for effective quality control?
Get Embed Code
Introduction to Quality Control Activities (QC Activities)
Quality Control Activities (QC Activities), or 品質管理活動 in Japanese, are a set of systematic processes aimed at maintaining and improving the quality of products, services, and processes within an organization. The primary goal is to ensure that outputs meet specific requirements, standards, and customer expectations. This involves various methodologies, tools, and techniques designed to identify and rectify defects, prevent quality issues, and enhance overall operational efficiency. For example, in a manufacturing scenario, QC activities might include regular inspections, testing of materials, and statistical process control to monitor production. In a software development context, it might involve code reviews, automated testing, and user feedback sessions to ensure the product meets the desired quality standards. Powered by ChatGPT-4o。
Main Functions of QC Activities
Inspection and Testing
Example
In a factory setting, inspection and testing involve examining finished products for defects or deviations from specifications. This can include visual inspections, functionality tests, and using measurement tools to ensure dimensions are correct.
Scenario
Before shipping, a batch of electronic devices undergoes a series of tests to check for battery life, screen resolution, and software stability to ensure each device meets the company's quality standards.
Statistical Process Control (SPC)
Example
SPC uses statistical methods to monitor and control a process. This helps in identifying process variations that might lead to quality issues.
Scenario
A beverage company uses SPC to monitor the filling process of bottles. Sensors and statistical software analyze the quantity of liquid filled in each bottle to ensure it's within the acceptable range, reducing waste and ensuring consistency.
Continuous Improvement (Kaizen)
Example
Kaizen, a Japanese term for 'change for better,' refers to activities that continuously improve all functions of an organization. It involves collecting feedback, analyzing processes, and making incremental improvements.
Scenario
A service company regularly gathers customer feedback through surveys. This information is analyzed to identify patterns and areas for improvement, leading to changes in service protocols to enhance customer satisfaction.
Quality Audits
Example
Quality audits involve a systematic examination of a quality system carried out by an internal or external quality auditor or audit team. It evaluates how well quality procedures are followed.
Scenario
An annual audit in a pharmaceutical company assesses compliance with quality management standards, examining documentation, practices, and procedures to ensure they meet regulatory requirements and improve product safety.
Ideal Users of QC Activities Services
Manufacturing Companies
Manufacturers can significantly benefit from QC activities to ensure their products meet safety, quality, and regulatory standards. This is crucial for maintaining competitiveness, reducing waste, and avoiding recalls.
Service Providers
Service-oriented businesses, such as hospitality, banking, and healthcare, use QC activities to evaluate service delivery, ensure customer satisfaction, and maintain operational excellence.
Software Development Firms
In the tech industry, where product complexity and user expectations are high, QC activities help in ensuring that software products are reliable, functional, and user-friendly.
Educational Institutions
Schools and universities implement QC activities to improve the quality of education, including curriculum development, teaching methods, and student services, ensuring they meet educational standards and student needs.
Guidelines for Using QC Activities
Start with YesChat.ai
Begin by visiting YesChat.ai for a free trial that requires no login or ChatGPT Plus subscription, offering an accessible entry point.
Identify Goals
Clearly define your quality control objectives. Understand what you aim to achieve with QC activities, whether it's reducing defects, improving processes, or ensuring customer satisfaction.
Select Tools
Choose the QC tools relevant to your goals. Common tools include cause-and-effect diagrams, check sheets, control charts, and Pareto charts.
Implement QC Plan
Apply the chosen tools to analyze data, identify root causes of quality issues, and implement corrective actions. Ensure all team members are trained on QC procedures.
Monitor and Improve
Regularly review the effectiveness of QC activities. Use feedback and data to make continuous improvements, adapting your approach as necessary.
Try other advanced and practical GPTs
Motivational Messenger
Inspire Daily, Achieve More with AI

التغذية الصحية
Empowering Healthy Eating with AI

R Code Helper
Empowering Your R Coding Journey with AI
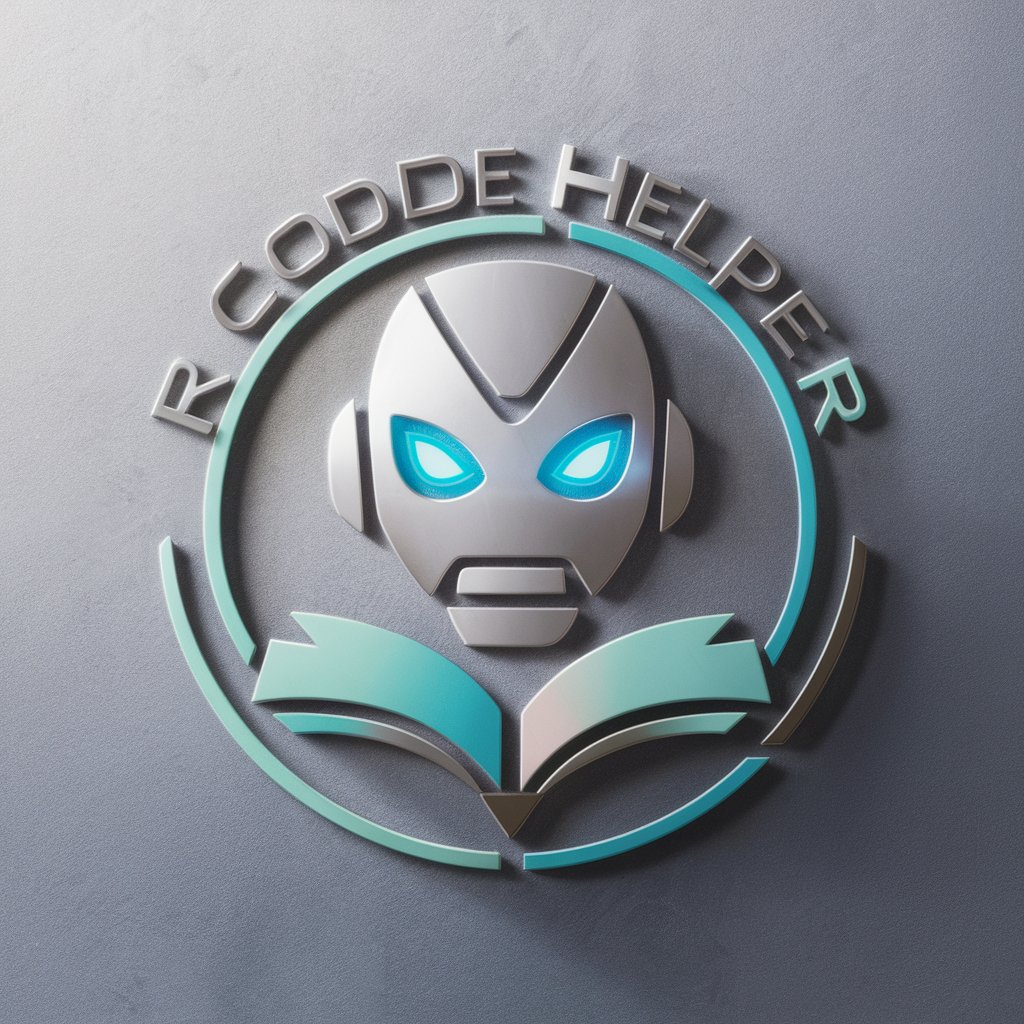
العقارات
Empowering Property Decisions with AI

Guía de Gemas
Unlock the secrets of gemstones with AI.

أسماء الأولاد
Discover Meaningful Arabic Names with AI

證厳法師は清らかな智慧の専門家であり。日本語
AI-powered insights into 證厳法師's teachings
Risk Raider
Empowering Your Financial Decisions with AI
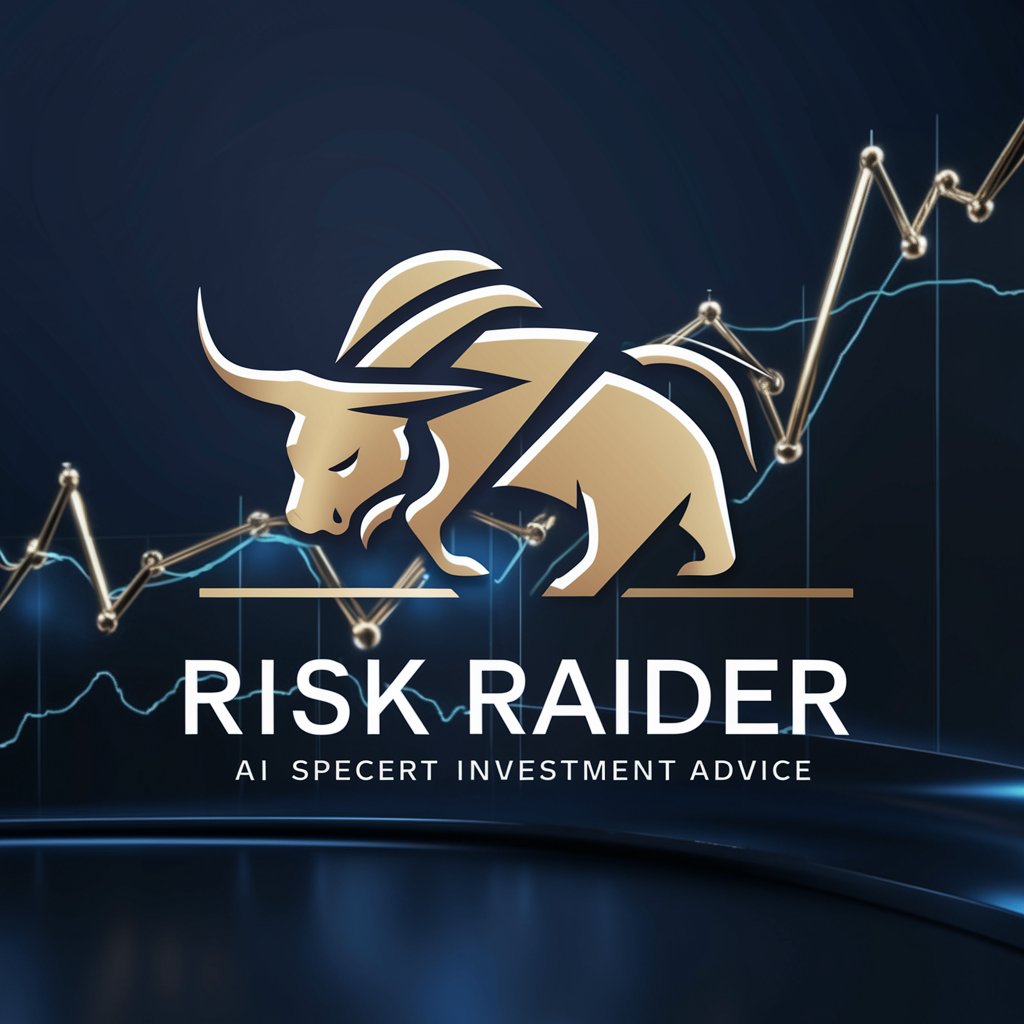
2024 New Years Resolution Coach
Empower Your Resolutions with AI

Voxella
Streamlining Product Management with AI

Académie Anatomie Humaine
Explore anatomy with AI power.

河蝶助理
Empowering YouTube Creators with AI

FAQs about QC Activities
What is QC Activities?
QC Activities refer to the systematic processes and methods used in quality control to identify, address, and prevent defects in products or services, ensuring they meet set quality standards.
How do QC tools differ?
QC tools vary in their application and focus. For example, control charts are used for monitoring process stability over time, while cause-and-effect diagrams help in identifying potential factors causing quality issues.
Can QC Activities be automated?
Yes, certain aspects of QC activities, such as data collection and analysis, can be automated using software tools. This increases efficiency and accuracy but requires proper setup and oversight.
How do I choose the right QC tools?
Select QC tools based on your specific quality objectives, the nature of your processes, and the types of data you will analyze. Consider tools that best facilitate problem identification and solution implementation.
What are the benefits of QC Activities?
QC Activities enhance product quality, reduce costs associated with defects, improve customer satisfaction, and foster a culture of continuous improvement within the organization.