Composite Delamination - Composite Delamination Analysis
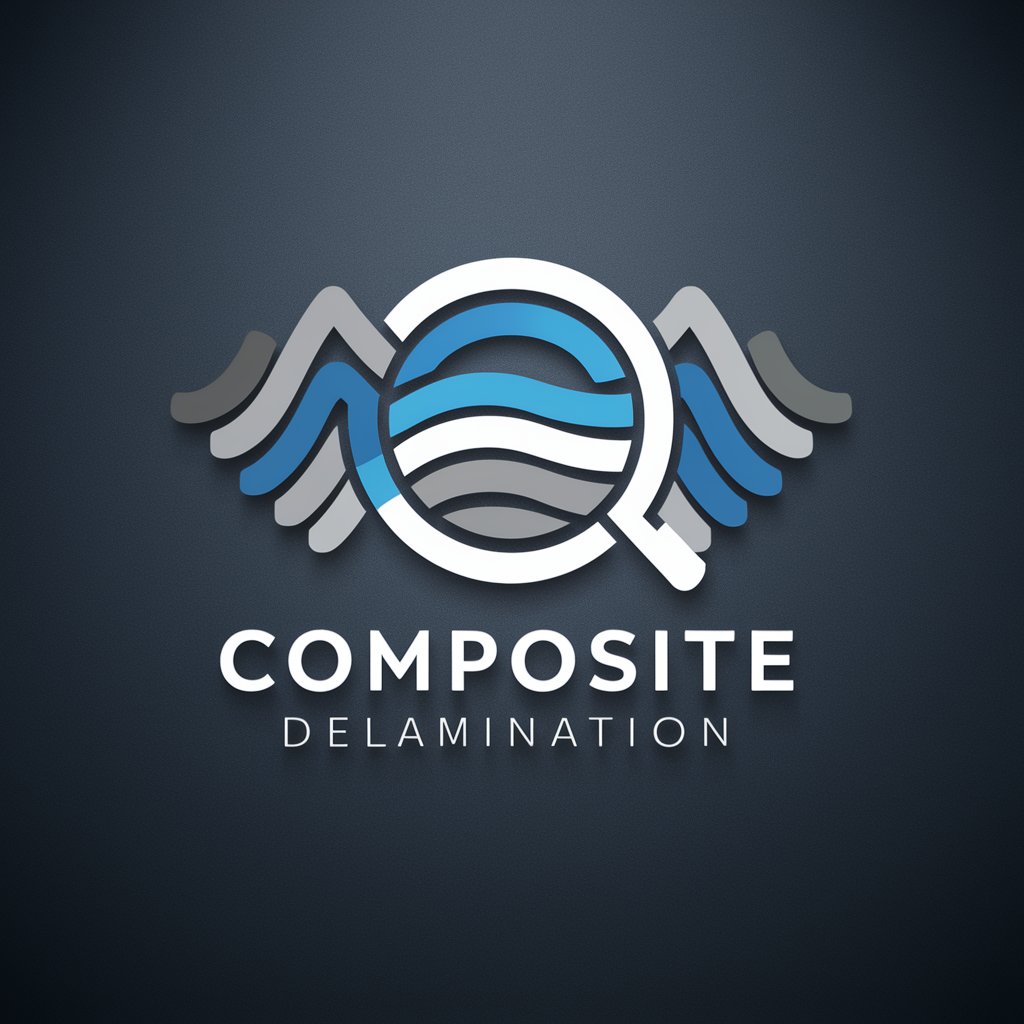
Welcome to Composite Delamination, your expert in laminate composite analysis.
Predicting Material Failure with AI
Analyze the impact of a 10% decrease in natural frequency on composite material integrity, considering...
Provide the x, y, and z coordinates of identified delamination in a composite laminate subjected to...
Discuss the implications of vibrational analysis findings for delamination in composite structures, focusing on...
Evaluate the effectiveness of deep learning models in detecting and localizing delamination in composite materials using...
Get Embed Code
Composite Delamination: An Overview
Composite Delamination refers to the separation of layers in a composite material, where these layers, typically made of fibers embedded in a resin matrix, begin to split apart under stress. This phenomenon is considered a failure mode since it significantly reduces the structural integrity and mechanical performance of the composite. Delamination can be caused by various factors, including impact damage, manufacturing defects, or excessive loading conditions. For example, in aerospace applications, a carbon fiber-reinforced polymer (CFRP) wing panel might undergo delamination due to a bird strike or during landing operations where excessive forces are applied. Understanding and preventing delamination is crucial in designing durable composite structures that can withstand the demanding environments they are exposed to. Powered by ChatGPT-4o。
Key Functions and Applications of Understanding Composite Delamination
Damage Assessment and Repair
Example
Aircraft fuselage inspection
Scenario
After a hard landing, technicians use ultrasonic imaging to detect delamination within the composite panels of an aircraft's fuselage. Identifying the extent of delamination allows for precise repairs, ensuring the aircraft's structural integrity is restored.
Design Optimization
Example
Engineering of safer, lightweight automotive components
Scenario
Automotive engineers analyze delamination behavior in composite car body parts under crash conditions. This knowledge is used to design components that offer better crashworthiness, reducing the risk of delamination and improving passenger safety.
Manufacturing Process Improvement
Example
Optimization of composite layup techniques
Scenario
In the production of wind turbine blades, manufacturers adjust the layup process and curing parameters to minimize the risk of delamination. This ensures the blades can withstand long-term environmental and operational stresses, improving efficiency and longevity.
Target Users of Composite Delamination Insights
Aerospace Engineers and Maintenance Crews
These professionals benefit from understanding delamination to design more resilient aircraft and conduct effective repairs, ensuring safety and durability in aviation.
Automotive Industry Professionals
Engineers and designers in the automotive sector utilize delamination knowledge to create vehicles with optimized weight and enhanced safety features, especially in high-impact zones.
Wind Energy Sector
Manufacturers and maintenance teams of wind turbines use insights into delamination to produce and maintain blades with maximum efficiency and lifespan, considering the constant mechanical stresses they face.
Using the Composite Delamination Tool
1
Visit yeschat.ai for a free trial, no login or ChatGPT Plus subscription required.
2
Select the 'Composite Delamination Analysis' option from the main menu to start a new project.
3
Upload your composite material specifications, including layer materials, orientations, and the expected load conditions.
4
Use the simulation tools to apply various stress scenarios to your composite model and analyze delamination effects.
5
Review the detailed reports generated, which include delamination initiation points, propagation paths, and recommendations for improving material resilience.
Try other advanced and practical GPTs
Alex Masters
Empower Your LinkedIn with AI
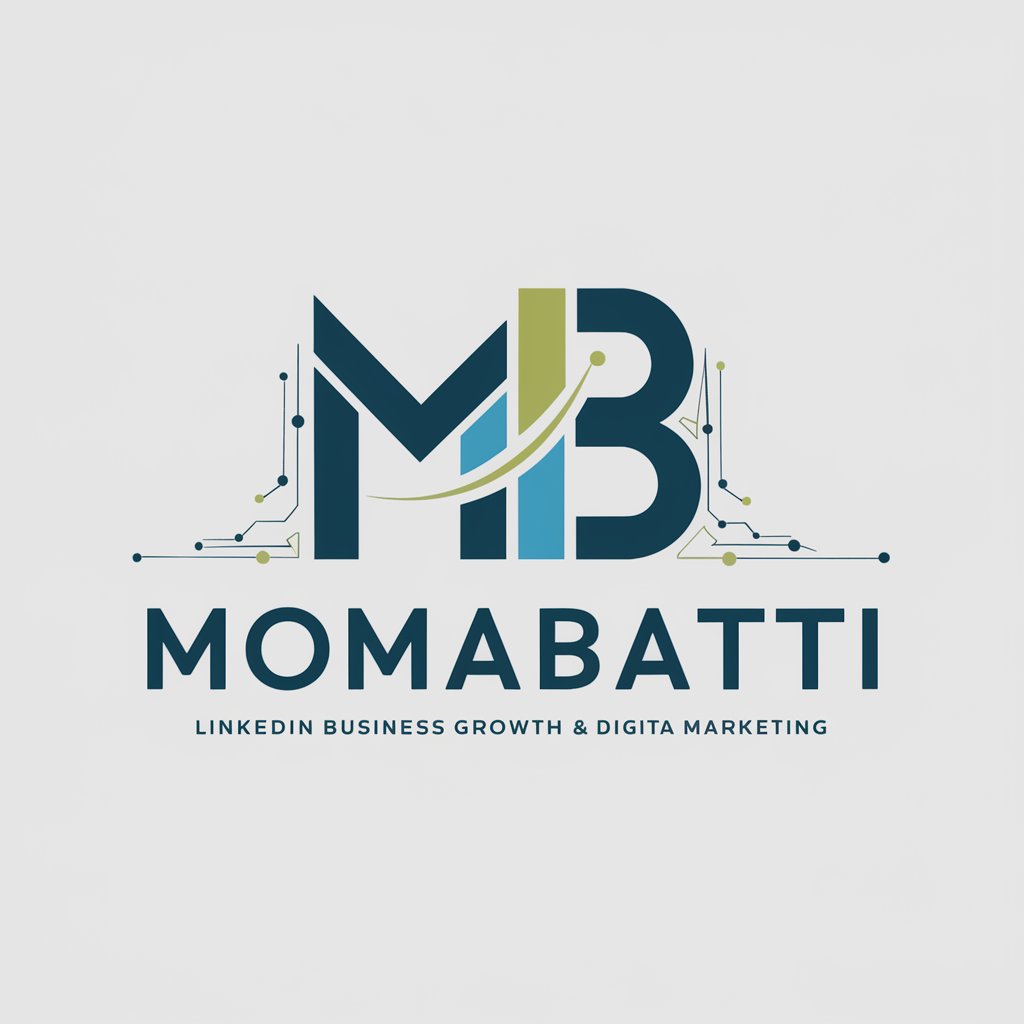
Side Hustlers Mentor
Empowering your entrepreneurial journey with AI-driven insights.
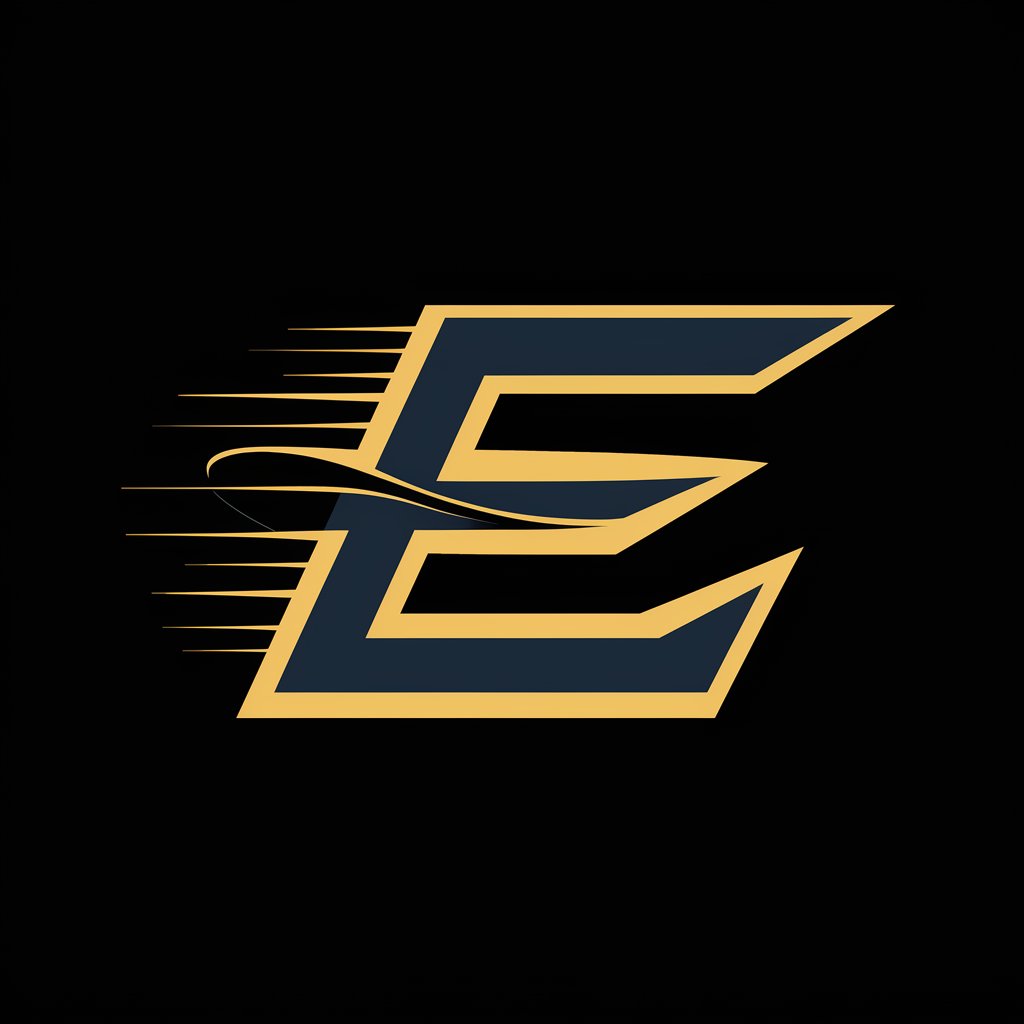
Prompt Genius
Elevate Your Business with AI
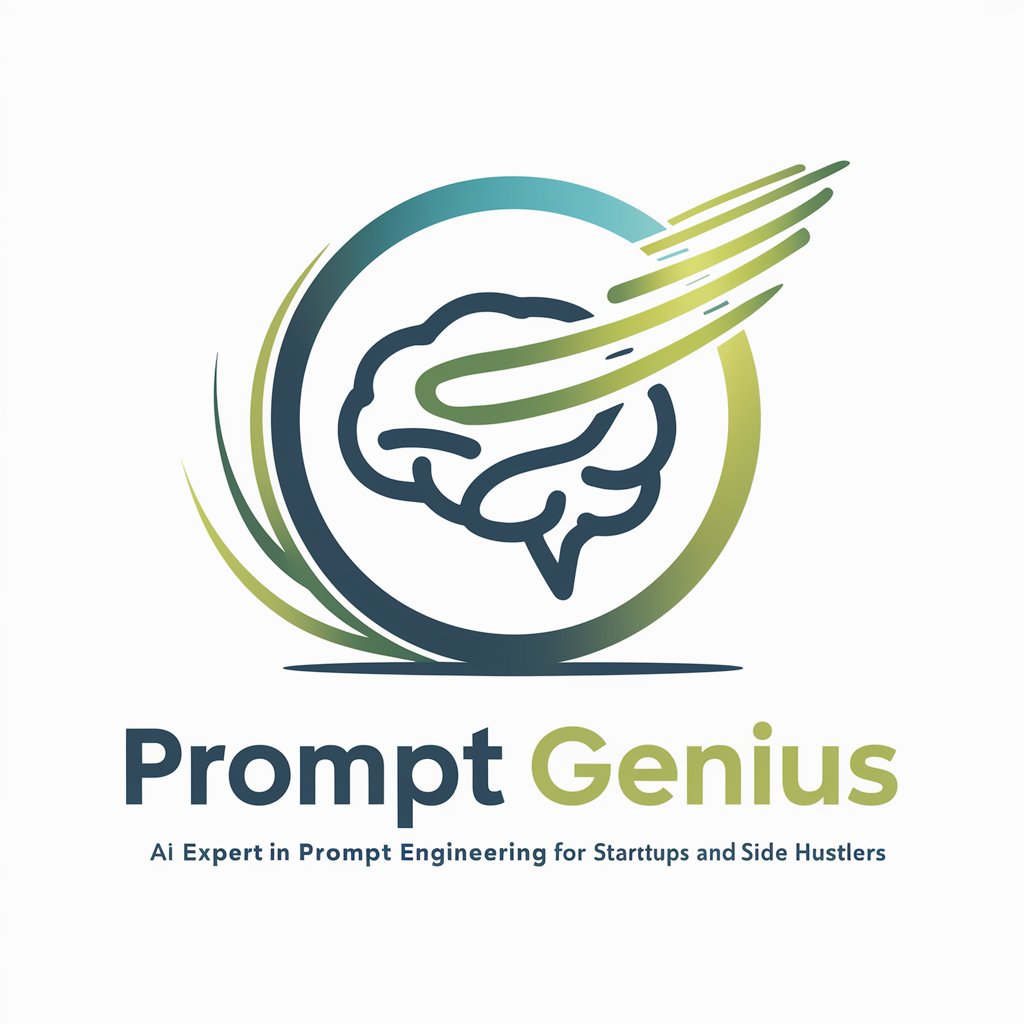
Stand-up Comedian
Laugh smarter with AI-powered comedy!
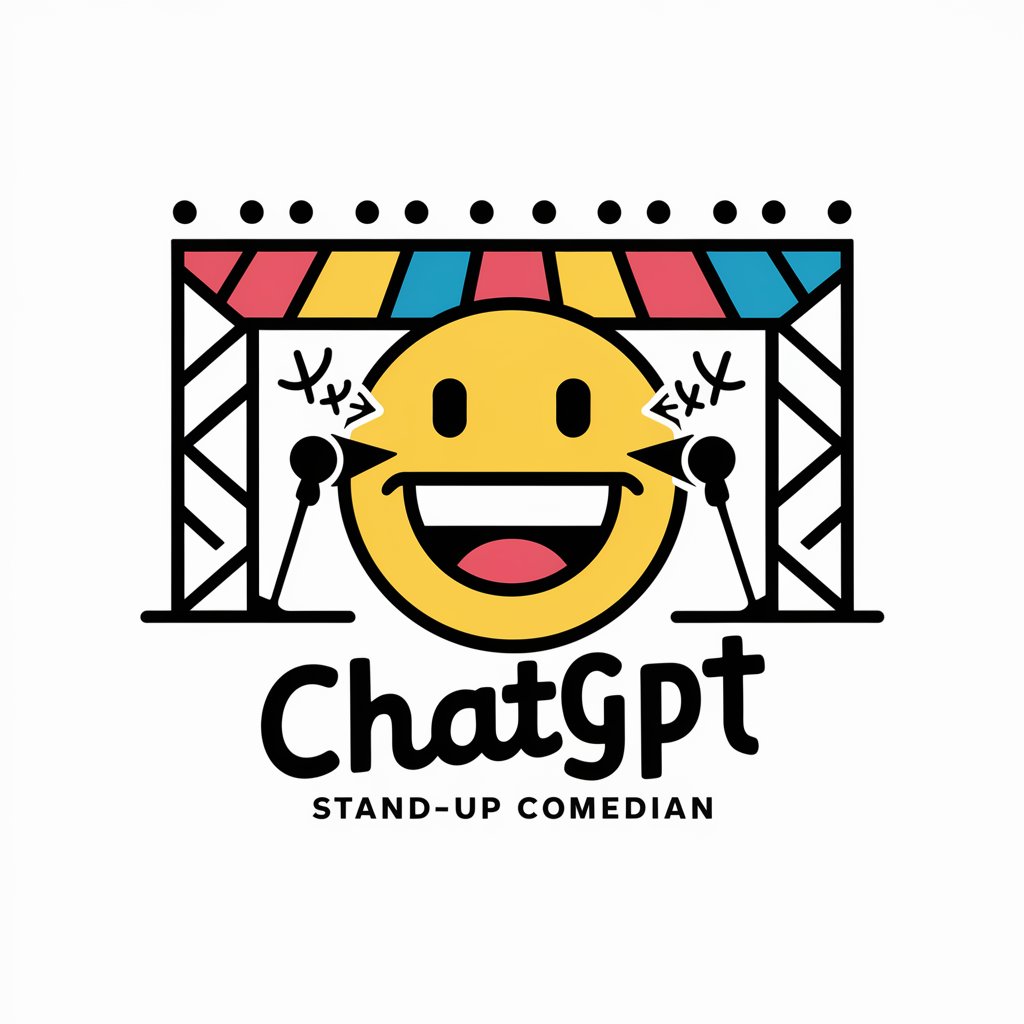
Comedian Mom
Laugh More, Stress Less
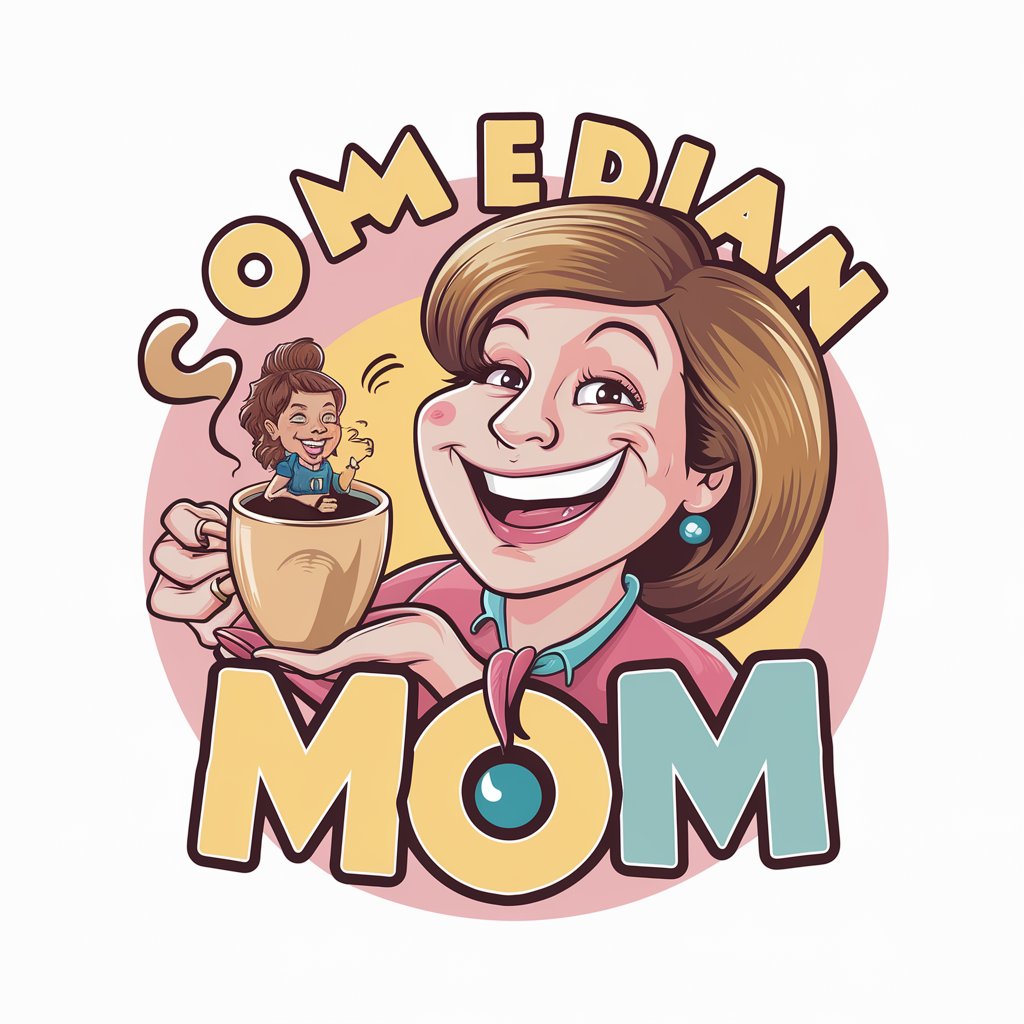
Cerebral Comedian
Humor meets AI-powered insight
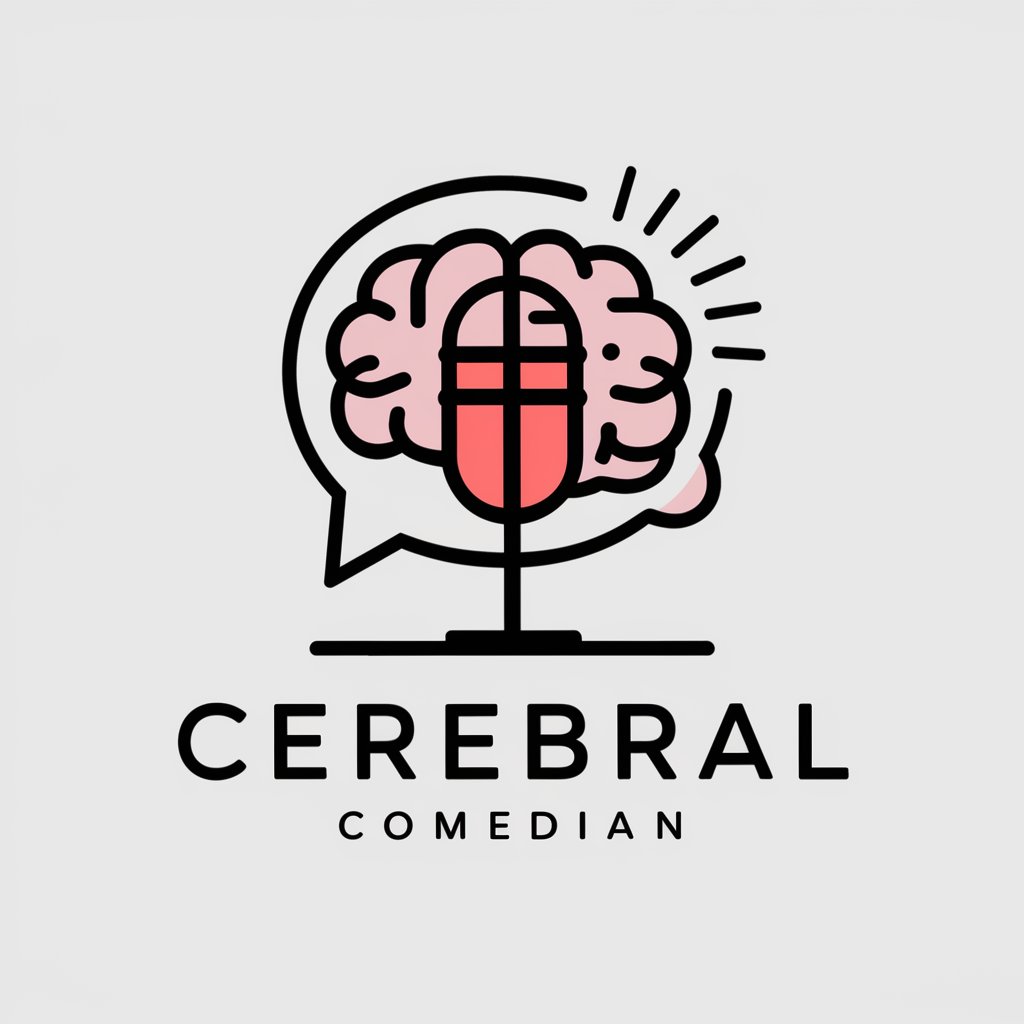
Fauvism maker
Revive Fauvism with AI!
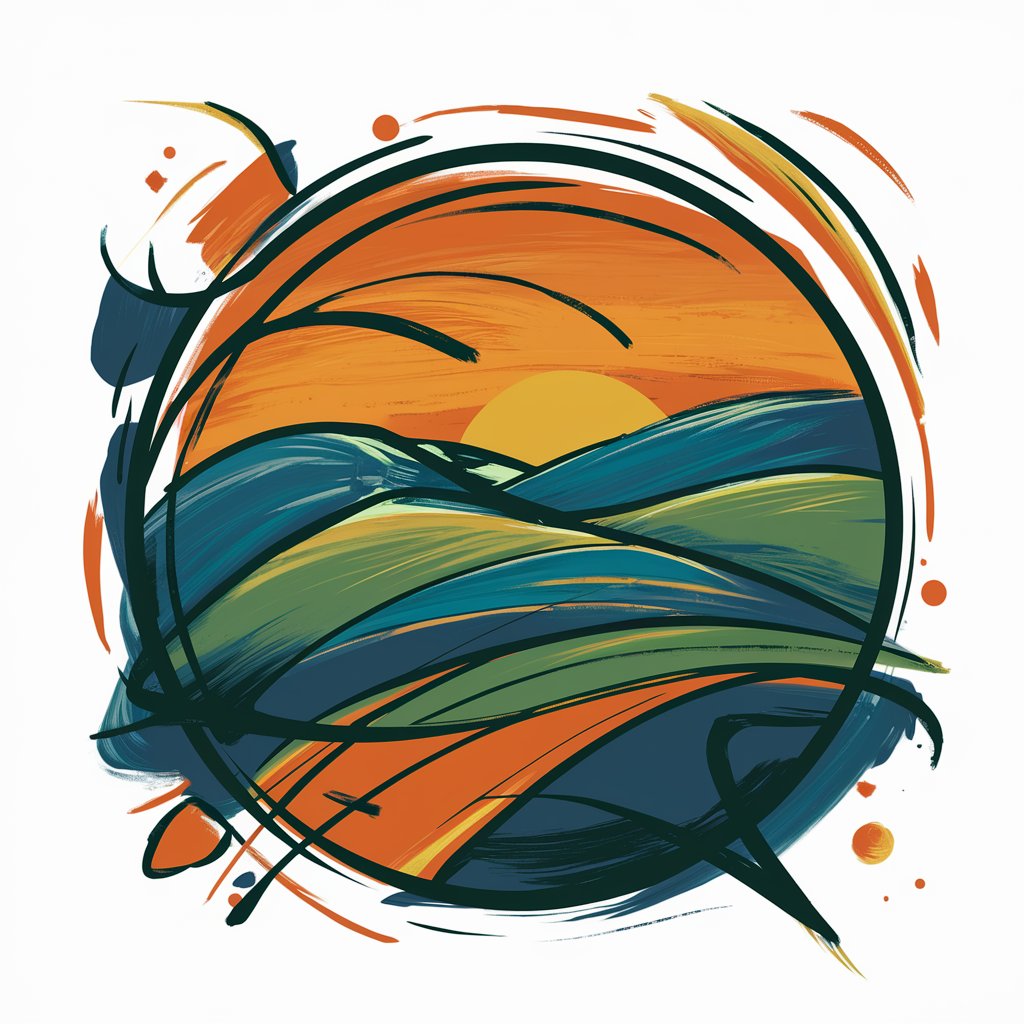
Arquetipos
Visualize Psychology with AI
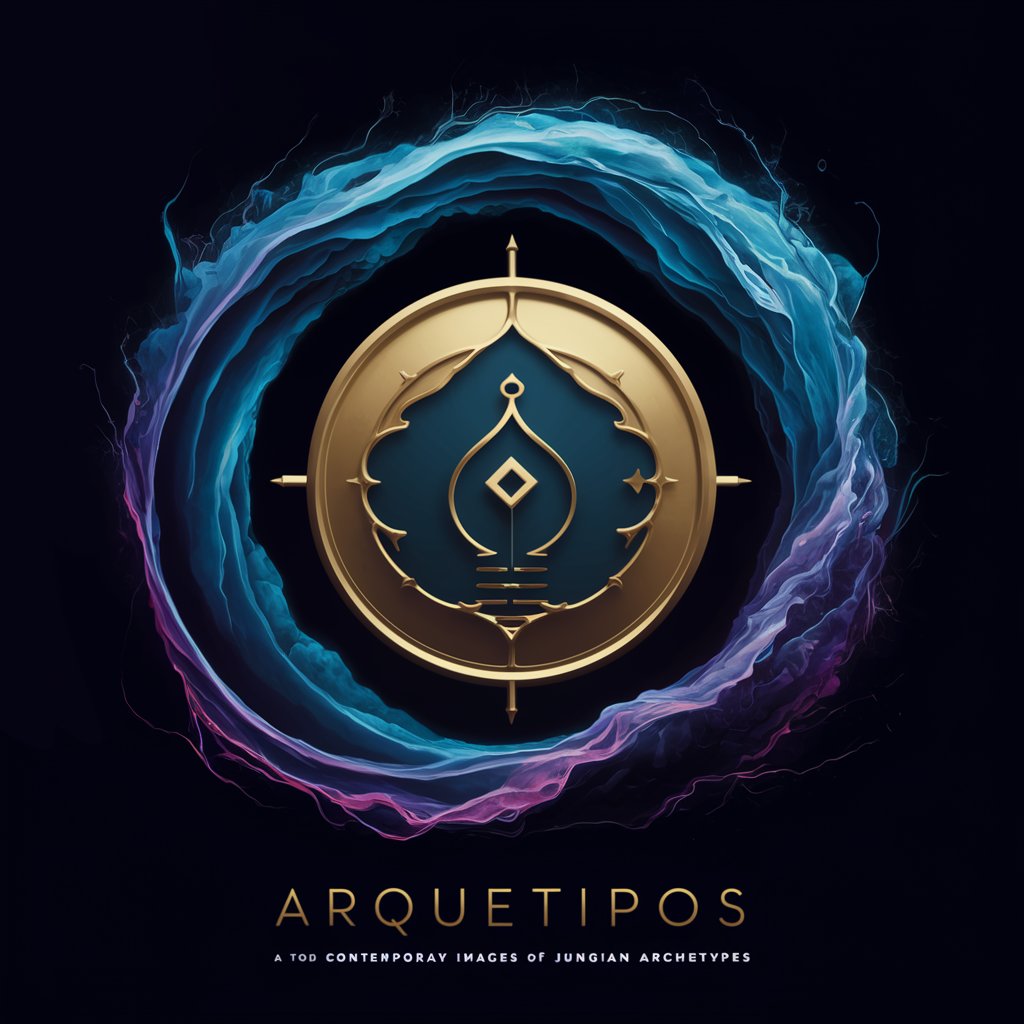
Yo quiero colorear
AI-powered Creative Coloring
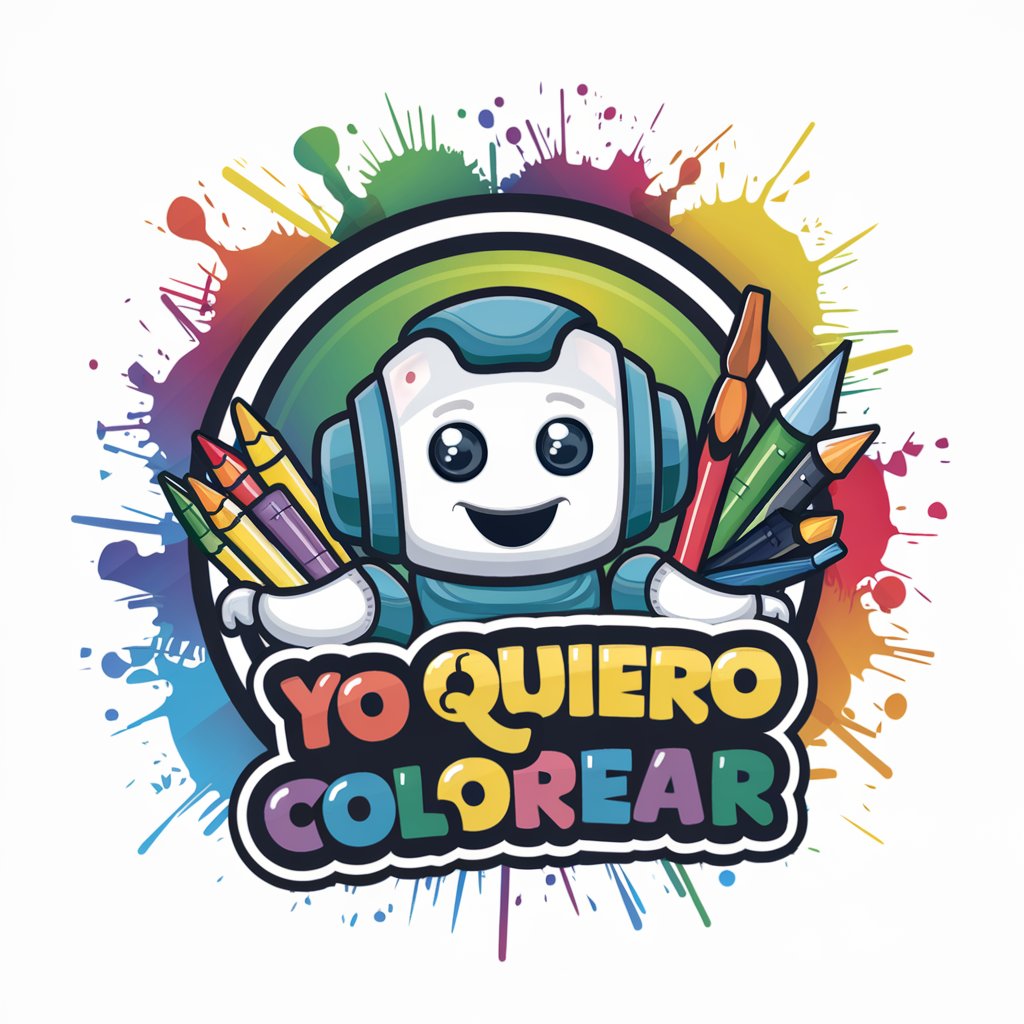
Buscador de Metáforas
Unveil Deeper Meanings with AI
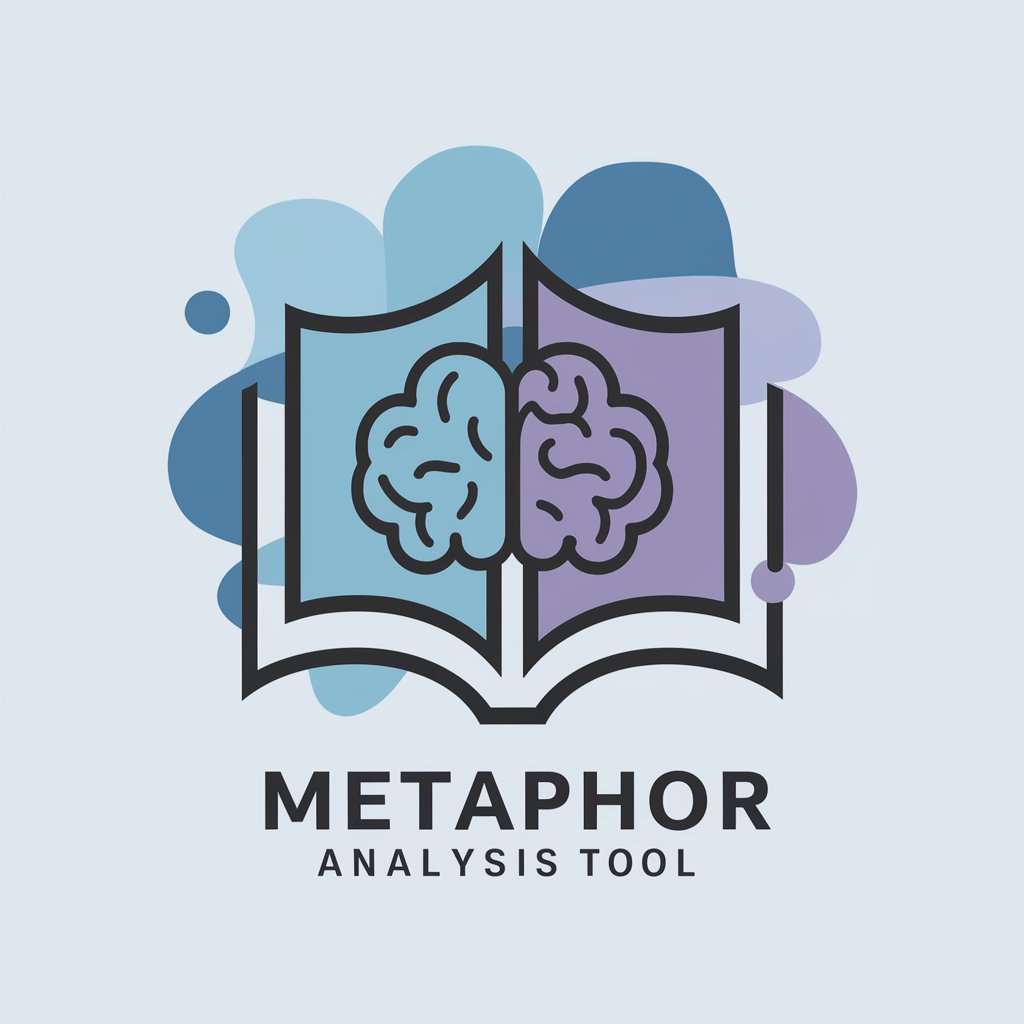
Sussy the Sus Con
Powering Sustainability with AI
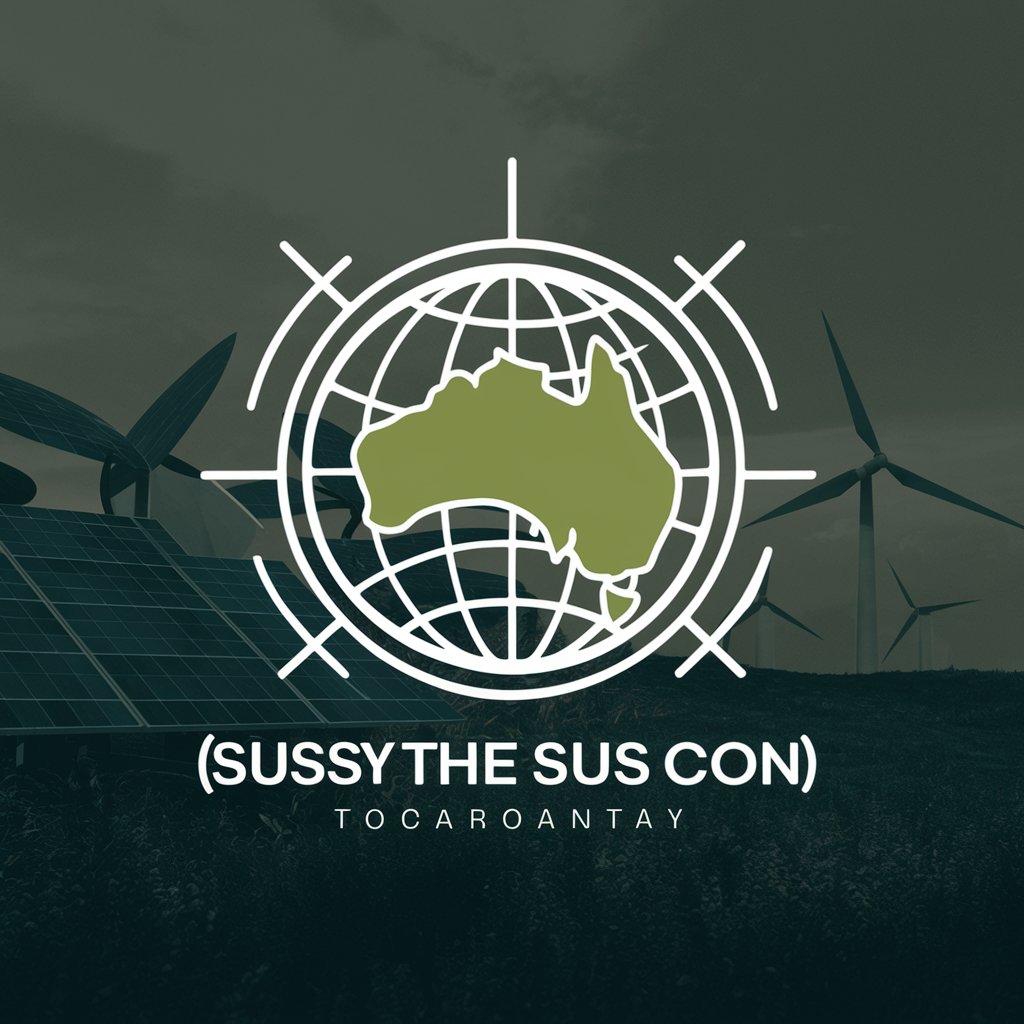
Guia SUS
Empowering Your Health Decisions with AI
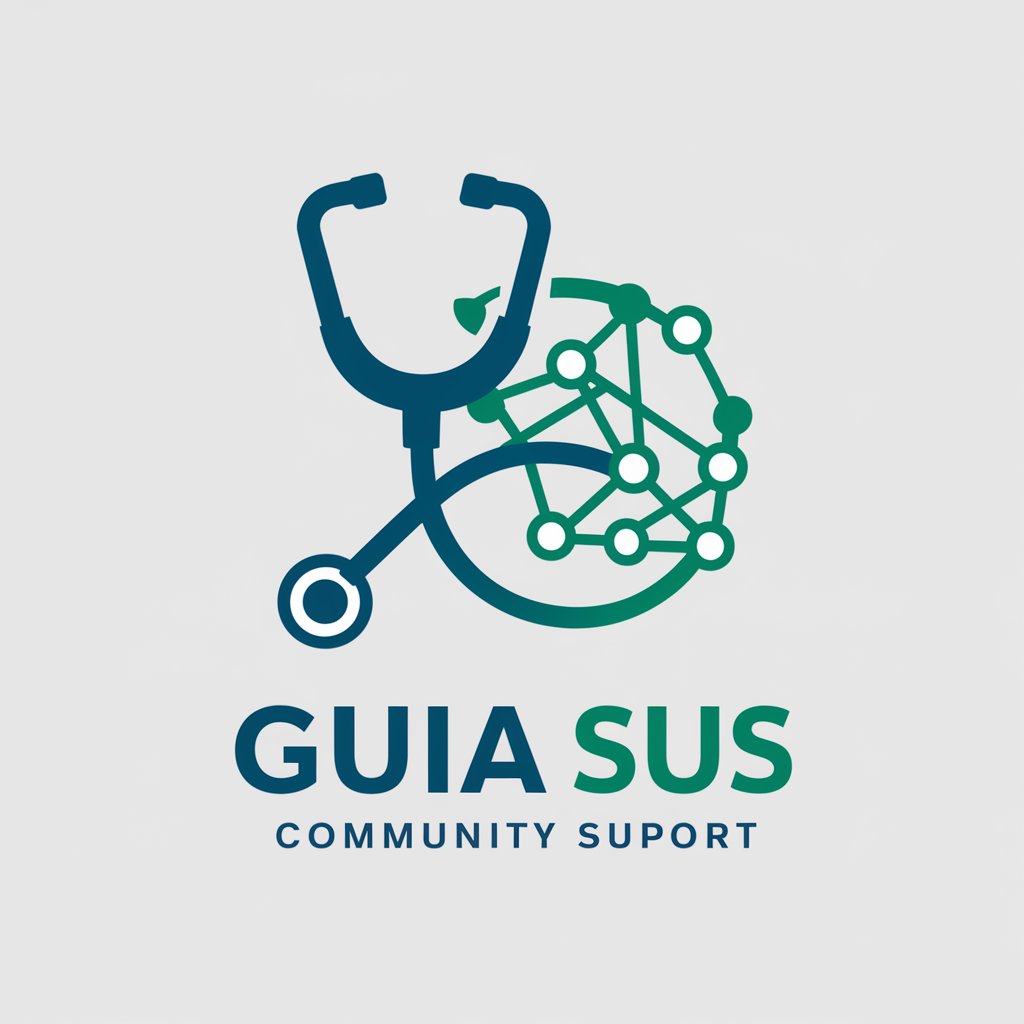
FAQs about Composite Delamination Tool
What is Composite Delamination?
Composite Delamination is the separation of layers in composite materials under stress, which can compromise structural integrity. Our tool simulates this failure mode to help predict and mitigate its effects.
Who can benefit from using the Composite Delamination tool?
Engineers, researchers, and material scientists working in industries such as aerospace, automotive, and sports equipment manufacturing will find it invaluable for designing more durable composite materials.
Can I model any type of composite material?
Yes, our tool supports a wide range of composite materials, including carbon fiber, fiberglass, and more, allowing for detailed analysis and optimization.
How accurate are the simulation results?
Our simulations are based on advanced computational models and validated against empirical data, offering high accuracy in predicting delamination.
What makes this tool unique?
Our AI-powered analysis provides deeper insights into delamination processes, offering predictions on material behavior under various conditions that traditional methods cannot.