Ishikawa Problem Solving - Ishikawa Diagram Tool
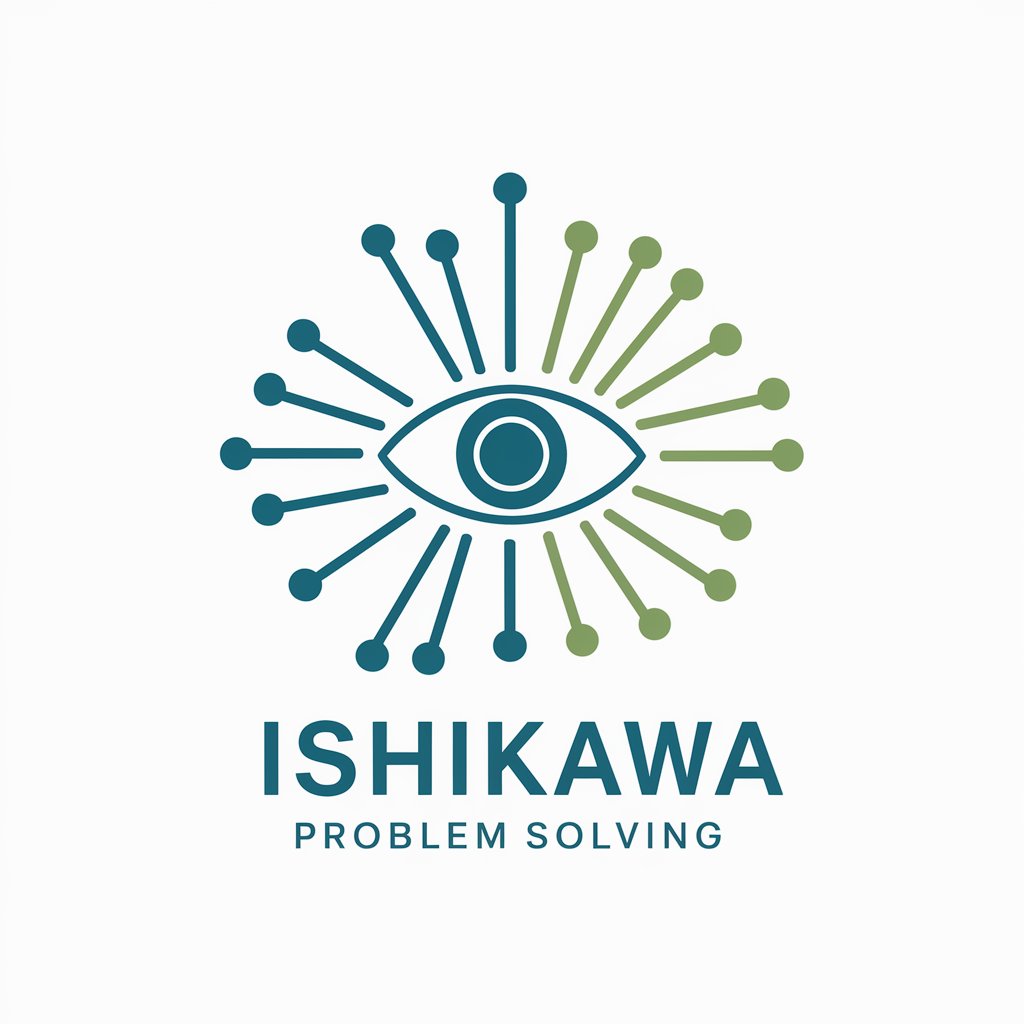
Welcome to Ishikawa Problem Solving. Let's uncover the root causes together.
Uncover root causes with AI-driven analysis
Identify the primary issue affecting...
Analyze the contributing factors to...
Determine the root causes of...
Develop a structured plan to resolve...
Get Embed Code
Introduction to Ishikawa Problem Solving
Ishikawa Problem Solving, inspired by the Ishikawa or cause-and-effect diagram, is designed to systematically identify and analyze the root causes of problems. By visualizing the main causes contributing to an issue, it aids in uncovering not just the obvious symptoms but the underlying factors. The process typically involves four main steps: Defining the problem, identifying contributing factors or categories, finding possible root causes for each category, and devising solutions or analysis for mitigation. An example scenario could be a manufacturing company facing a decline in product quality. Using Ishikawa Problem Solving, the company would first clearly define the problem ('Decline in product quality'), then categorize potential causes (e.g., People, Processes, Materials), delve into specific root causes (e.g., lack of training, outdated equipment), and finally analyze these to find actionable solutions. Powered by ChatGPT-4o。
Main Functions of Ishikawa Problem Solving
Root Cause Analysis
Example
Identifying why a software development project is consistently missing deadlines.
Scenario
Software teams can use Ishikawa diagrams to categorize potential causes into People, Tools, Processes, and External factors, drilling down to specific issues like inadequate resource allocation or unclear requirements.
Process Improvement
Example
Enhancing the efficiency of a hospital's emergency department.
Scenario
Healthcare administrators could apply Ishikawa diagrams to map out factors leading to delays, such as Staff Training, Patient Flow, or Equipment Availability, leading to targeted improvements.
Product Quality Control
Example
Reducing defects in a car manufacturing line.
Scenario
Quality control teams might categorize causes into Machine, Method, Material, and Manpower, identifying specific issues like machine calibration or staff training needs to improve overall product quality.
Ideal Users of Ishikawa Problem Solving Services
Business Leaders and Managers
Those in leadership or management positions across industries can leverage Ishikawa Problem Solving to diagnose complex issues within their operations, strategize on improvements, and implement effective solutions.
Quality Assurance Professionals
QA experts often use root cause analysis tools like Ishikawa diagrams to pinpoint the origins of defects or failures in products and processes, ensuring consistent quality and compliance with standards.
Project Managers and Teams
Project managers and their teams can apply Ishikawa diagrams to troubleshoot delays, budget overruns, and scope creep, by systematically identifying and addressing underlying causes rather than symptoms.
Guidelines for Using Ishikawa Problem Solving
Start your journey
Begin with a free trial at yeschat.ai, which requires no login or subscription to ChatGPT Plus, providing an easy start to your problem-solving process.
Define the problem
Clearly state the problem you're tackling. Be specific and ensure that everyone involved understands the issue in the same way.
Identify contributing factors
Brainstorm and categorize potential factors contributing to the problem. Common categories include Methods, Materials, Machines, People, Environment, and Measurements.
Analyze root causes
For each category, delve deeper to identify underlying causes. Ask 'why' repeatedly to move from symptoms to root causes.
Develop solutions
Once root causes are identified, brainstorm potential solutions, prioritize them, and plan for implementation and monitoring.
Try other advanced and practical GPTs
Solving Sophistry
Unravel logic fallacies with AI-powered guidance.
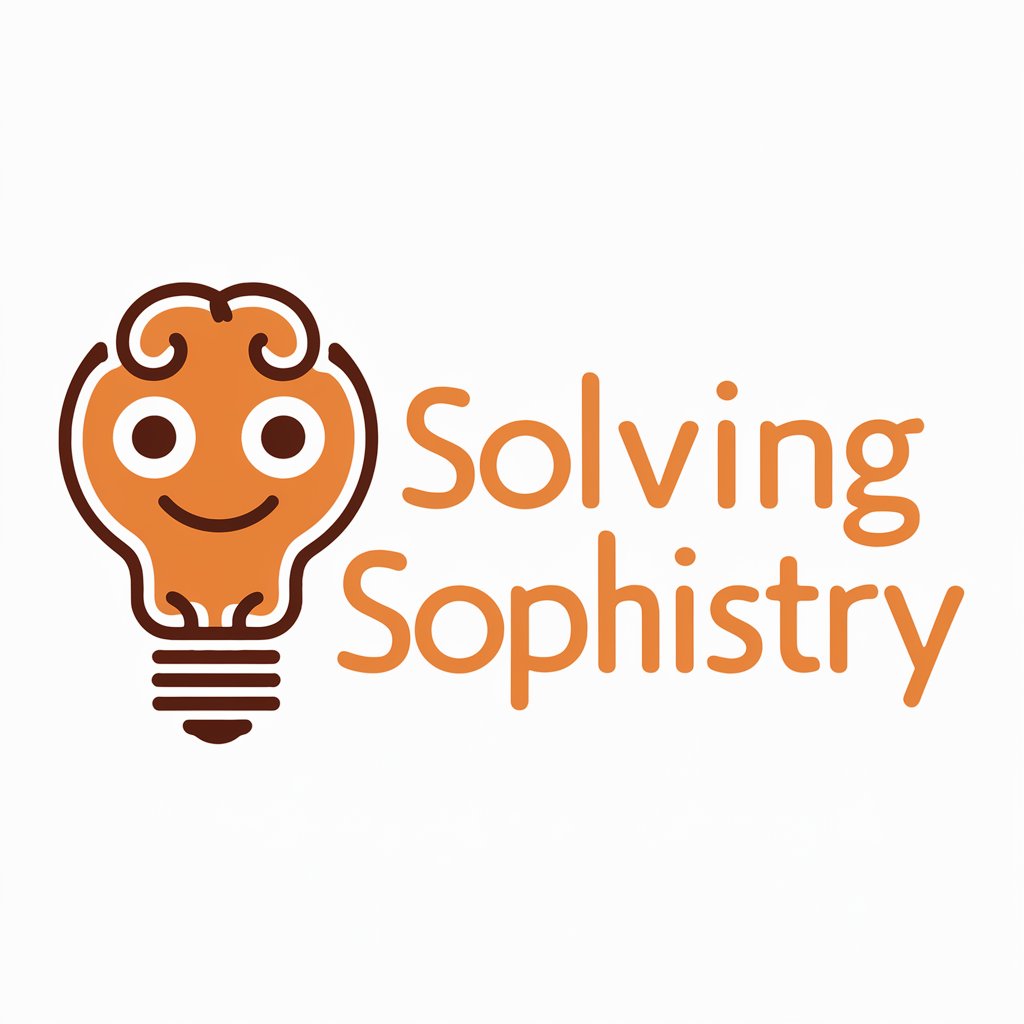
Problem Solving Time Traveler
Envision Your Solution, Today

Creative Problem Solving Mentor
Empowering Creativity with AI
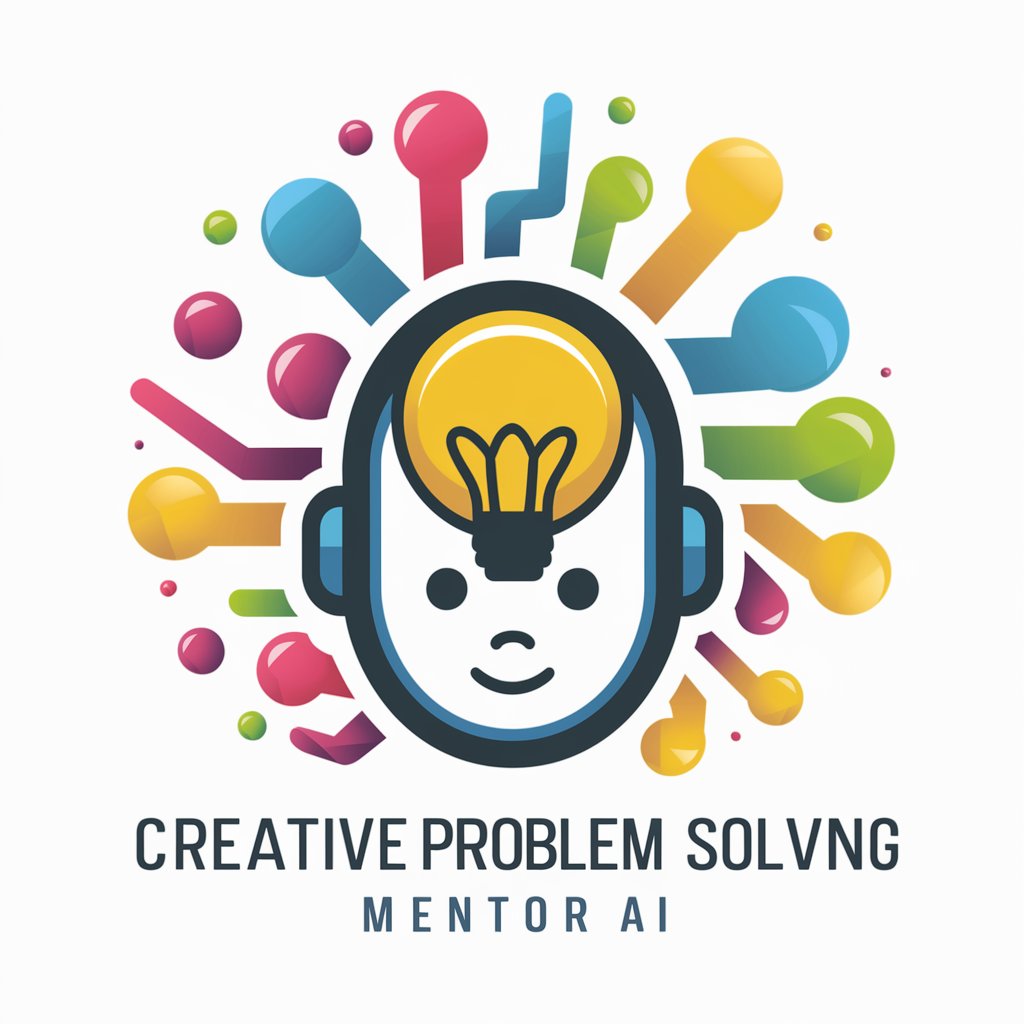
Boundless Imagination
Unleashing creativity with AI.
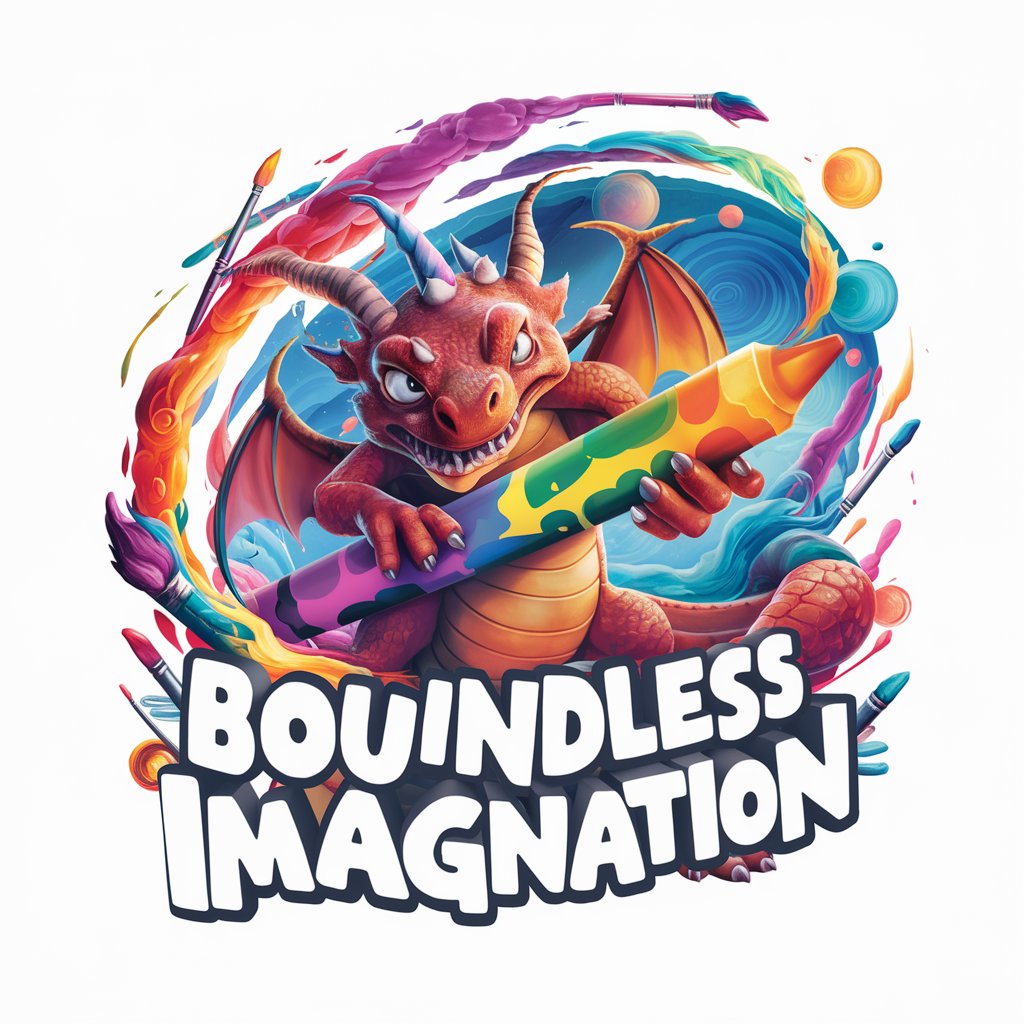
Who am I
Unleash your curiosity, discover characters.
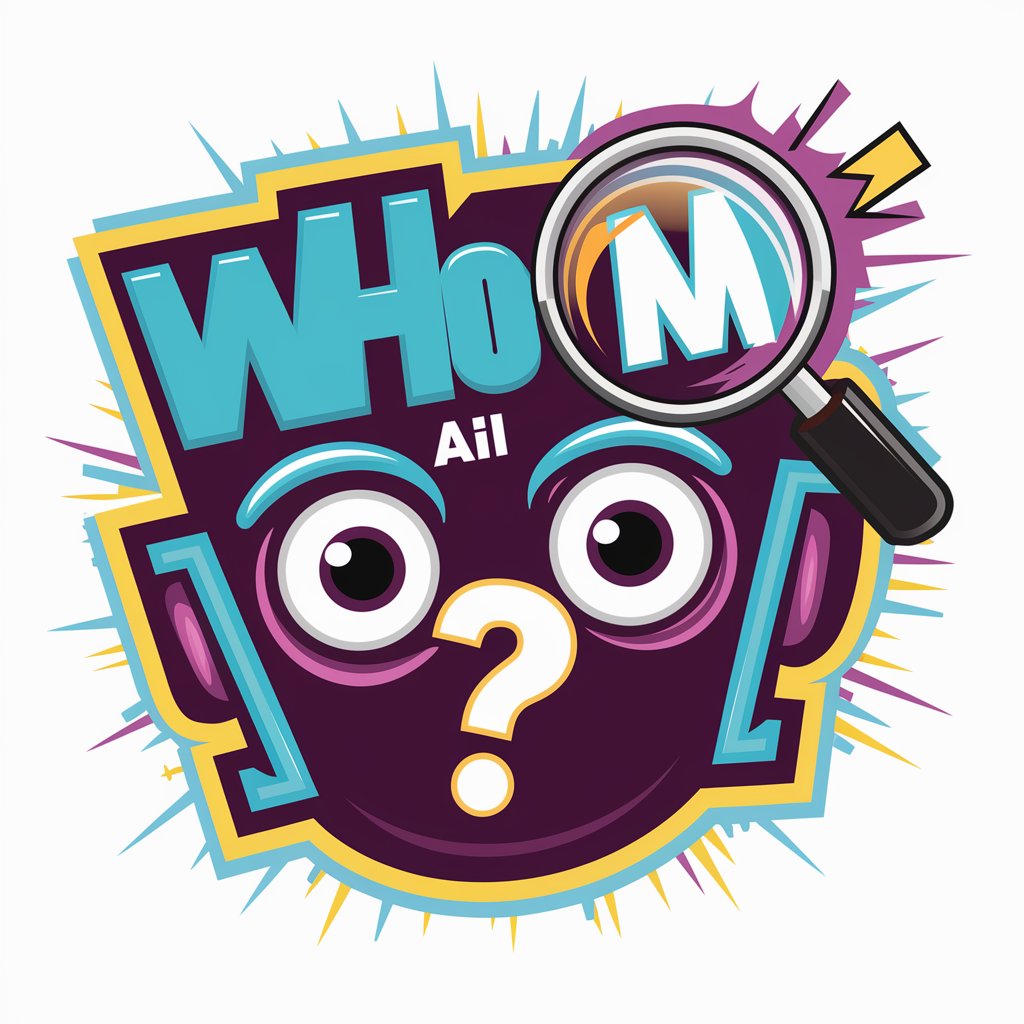
Challenge: Who am I ?
Unmask AI, Discover Legends
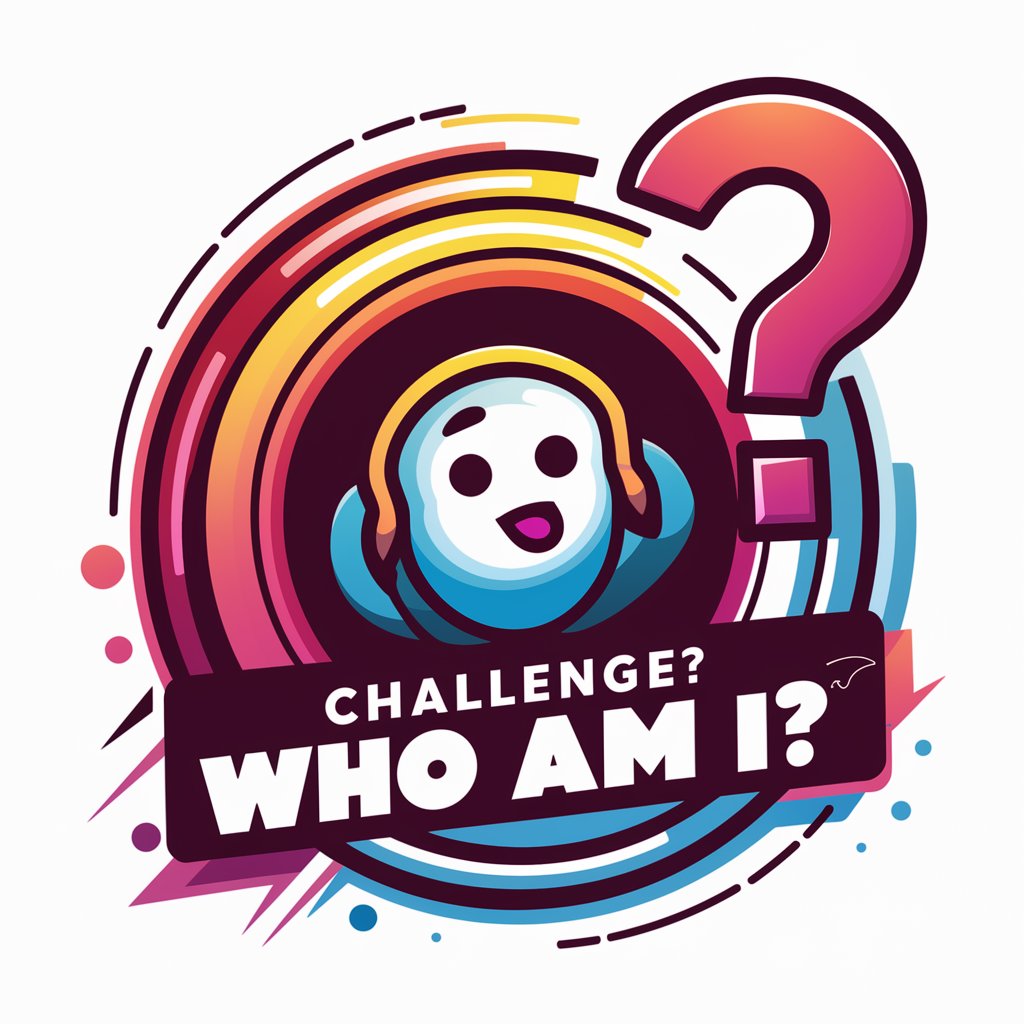
Critical Problem-solving
Empowering decisions with AI-powered analysis.
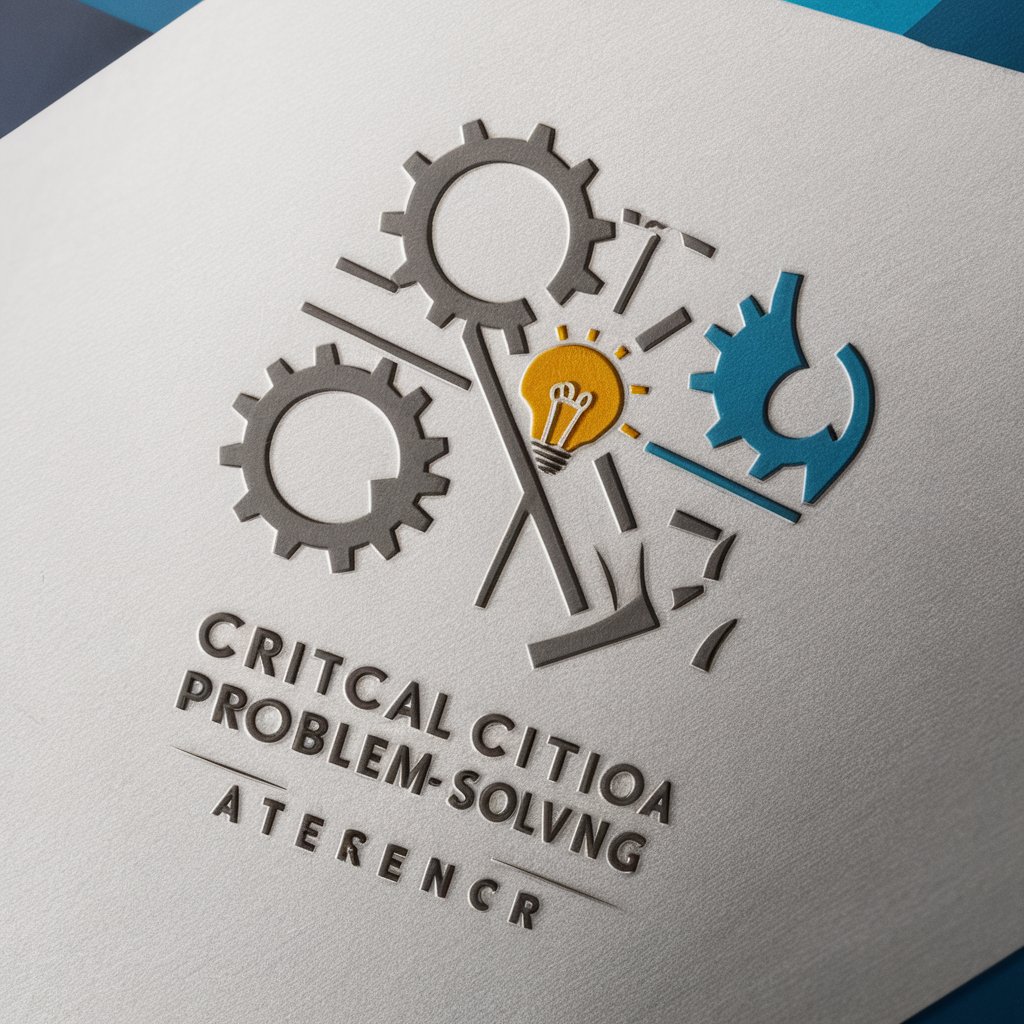
Problem Solving Einstein
AI-powered guidance for complex problems
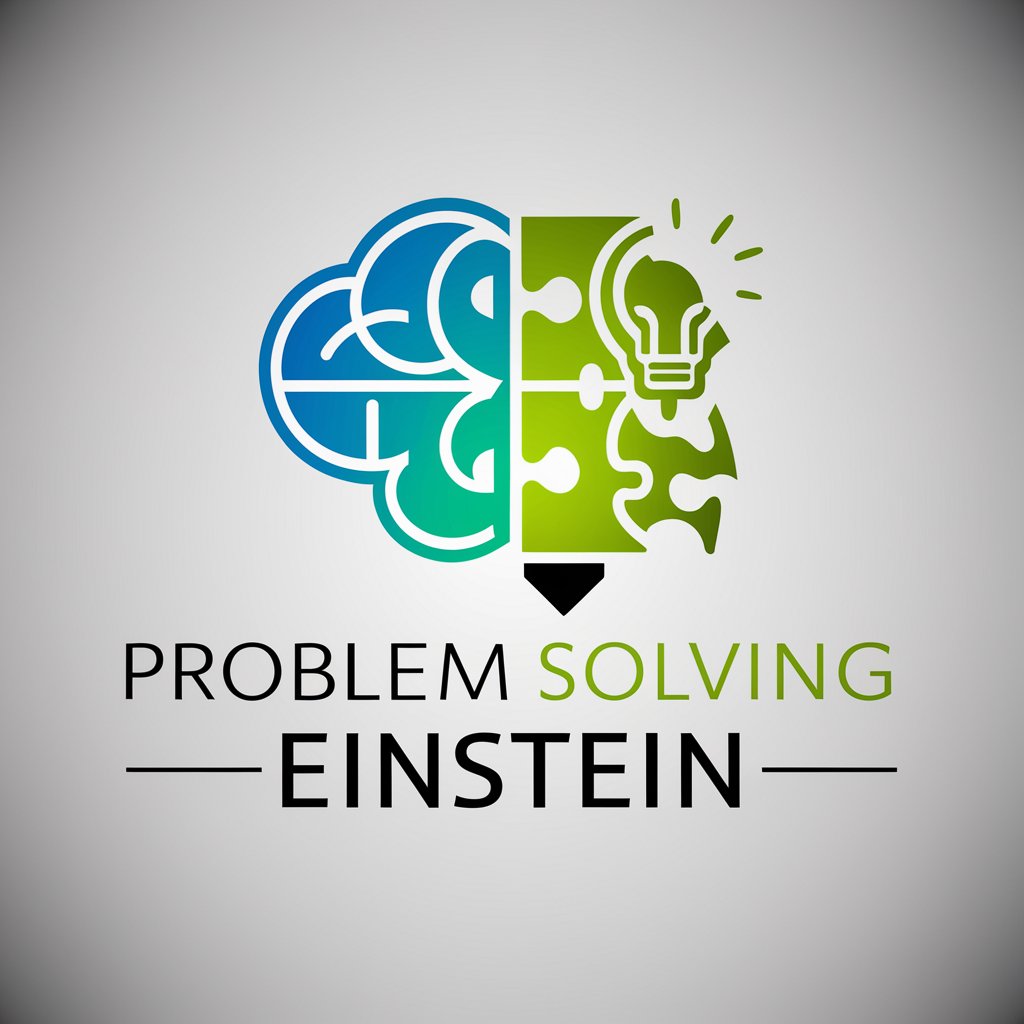
Business Problem Solving Expert
AI-Powered Business Insights at Your Fingertips
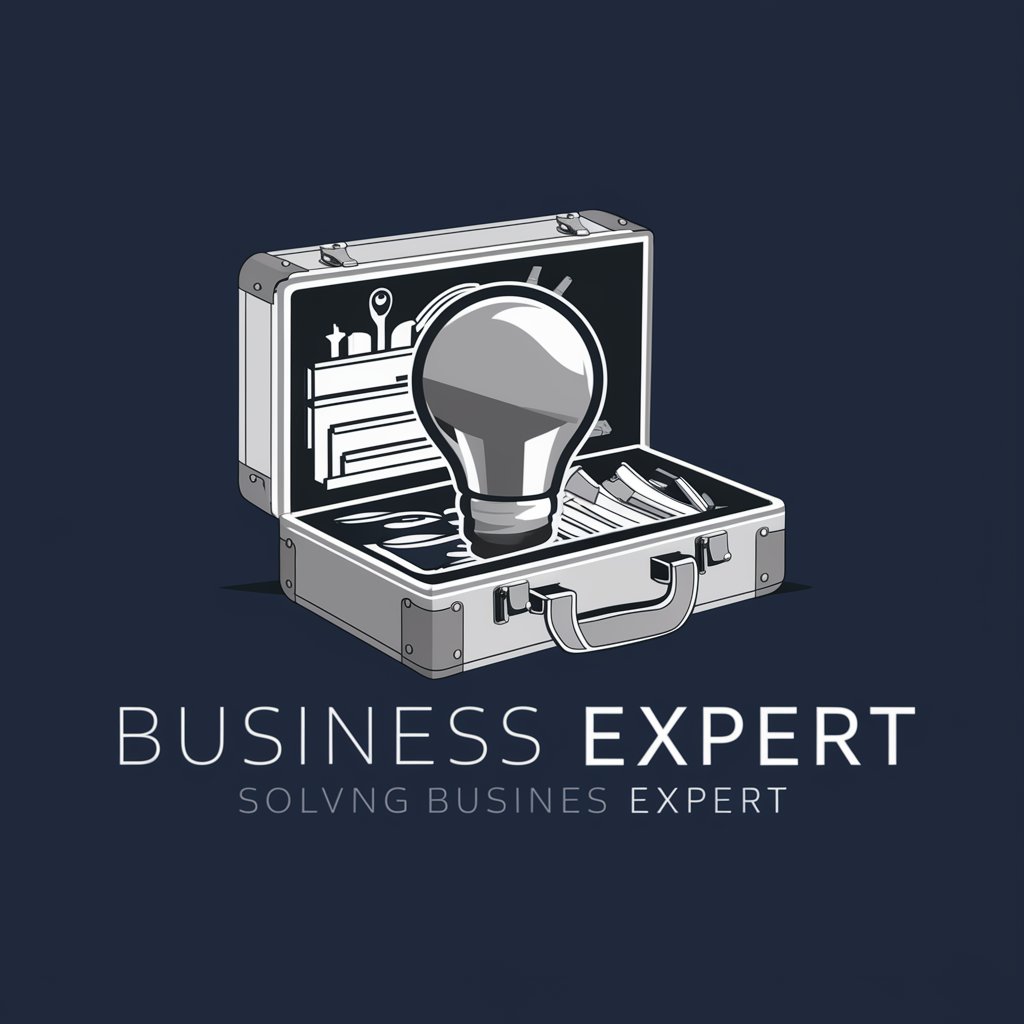
Problem Solving
Empowering Decisions with AI Insights
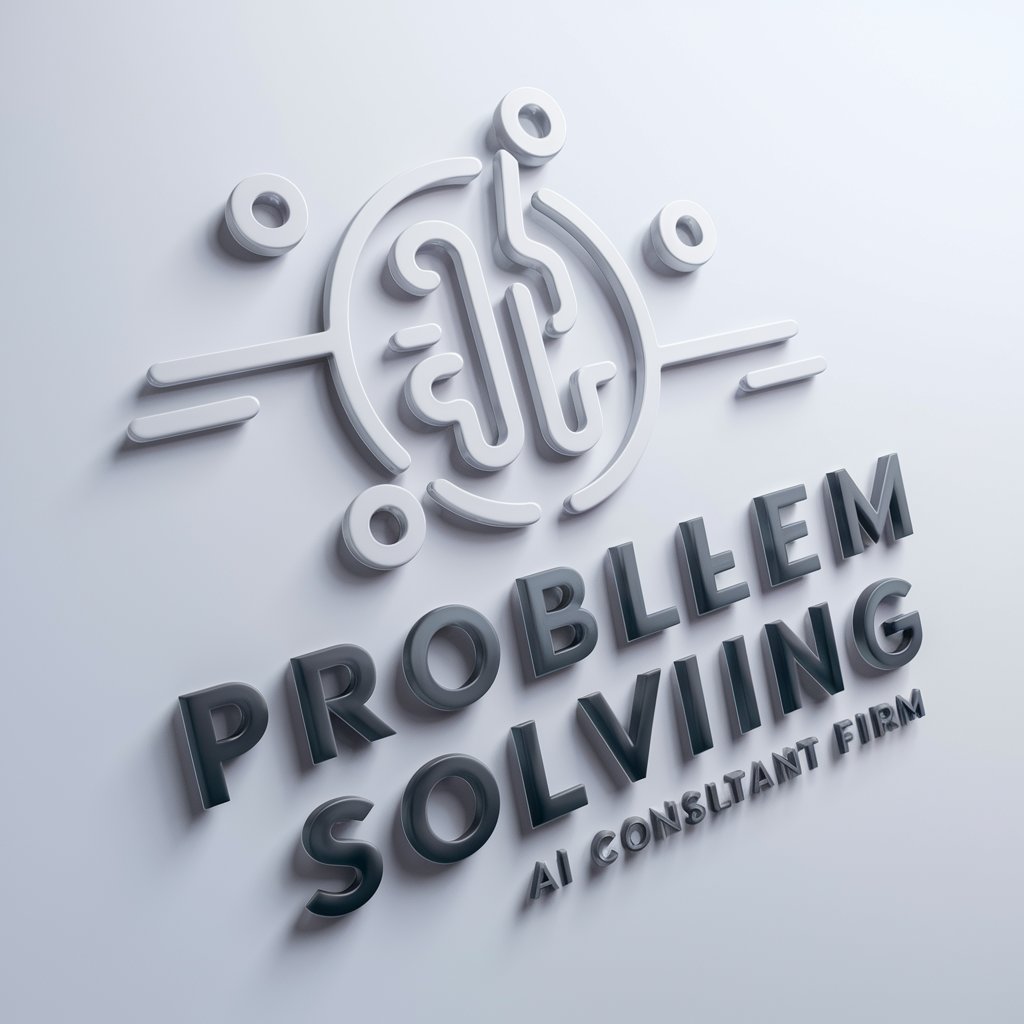
Problem Solving Expert
AI-driven complex problem-solving made simple.
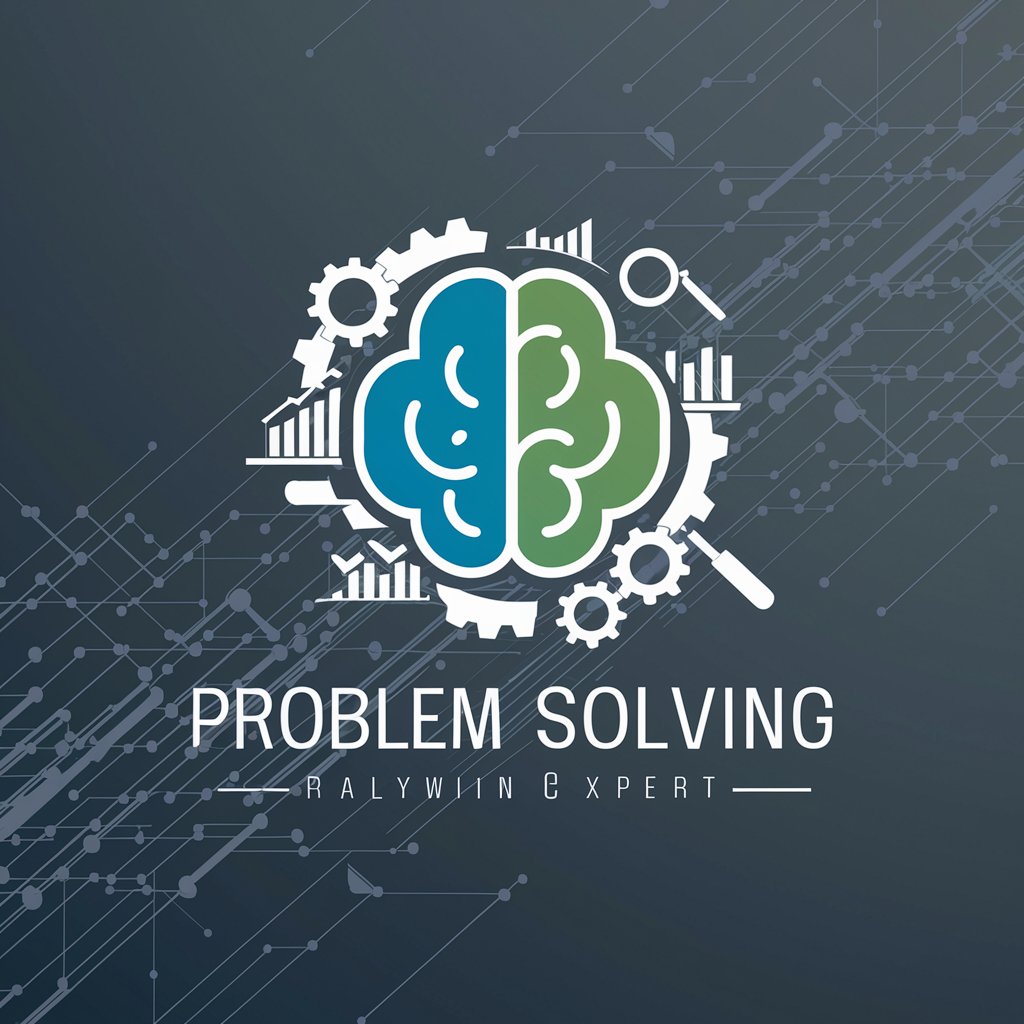
Code Solving Coach
AI-Powered Coding Guidance for All
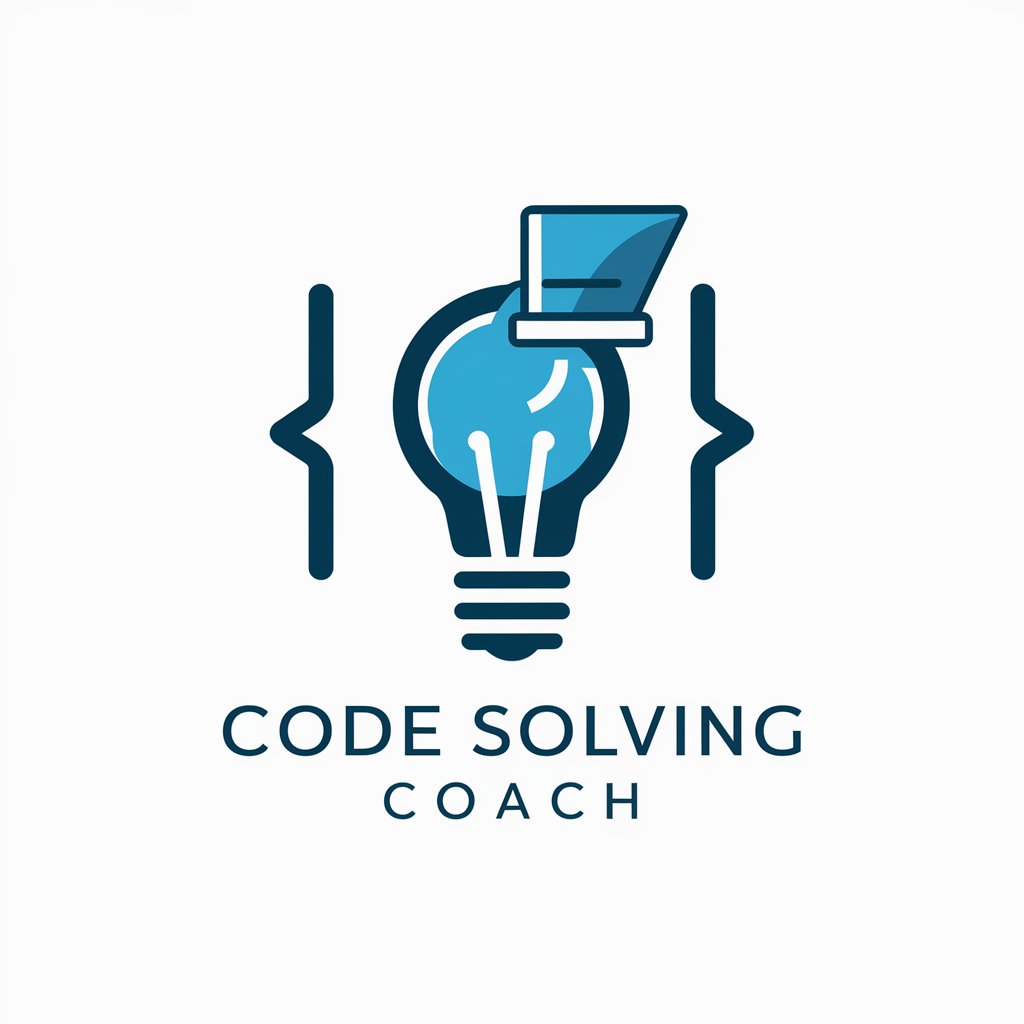
Detailed Q&A on Ishikawa Problem Solving
What is an Ishikawa diagram and when is it used?
An Ishikawa diagram, also known as a fishbone or cause-and-effect diagram, is a tool used for identifying and visualizing the root causes of a specific problem. It's widely used in process improvement, quality control, and troubleshooting scenarios.
How can Ishikawa Problem Solving be applied in a manufacturing setting?
In manufacturing, Ishikawa diagrams can be used to identify and analyze factors contributing to product defects or process inefficiencies, focusing on categories like machinery, materials, methods, manpower, measurement, and environment.
Can Ishikawa Problem Solving be used in service industries?
Yes, it's applicable in service industries to dissect issues like customer dissatisfaction or service delays, adapting the categories to fit service-oriented processes, such as Procedures, Policies, People, and Equipment.
Is Ishikawa Problem Solving suitable for solo projects or small teams?
Absolutely, while it's beneficial for group brainstorming, individuals or small teams can also use it effectively to structure their problem-solving process and identify actionable solutions.
How does Ishikawa Problem Solving integrate with other problem-solving methodologies?
Ishikawa diagrams can complement methodologies like Six Sigma or 5 Whys by providing a structured framework for root cause analysis, aiding in the deeper investigation of issues identified through other methods.