Resin, Pigment,Filler,Additive,Defoamer,Promoter - Advanced Material Solutions
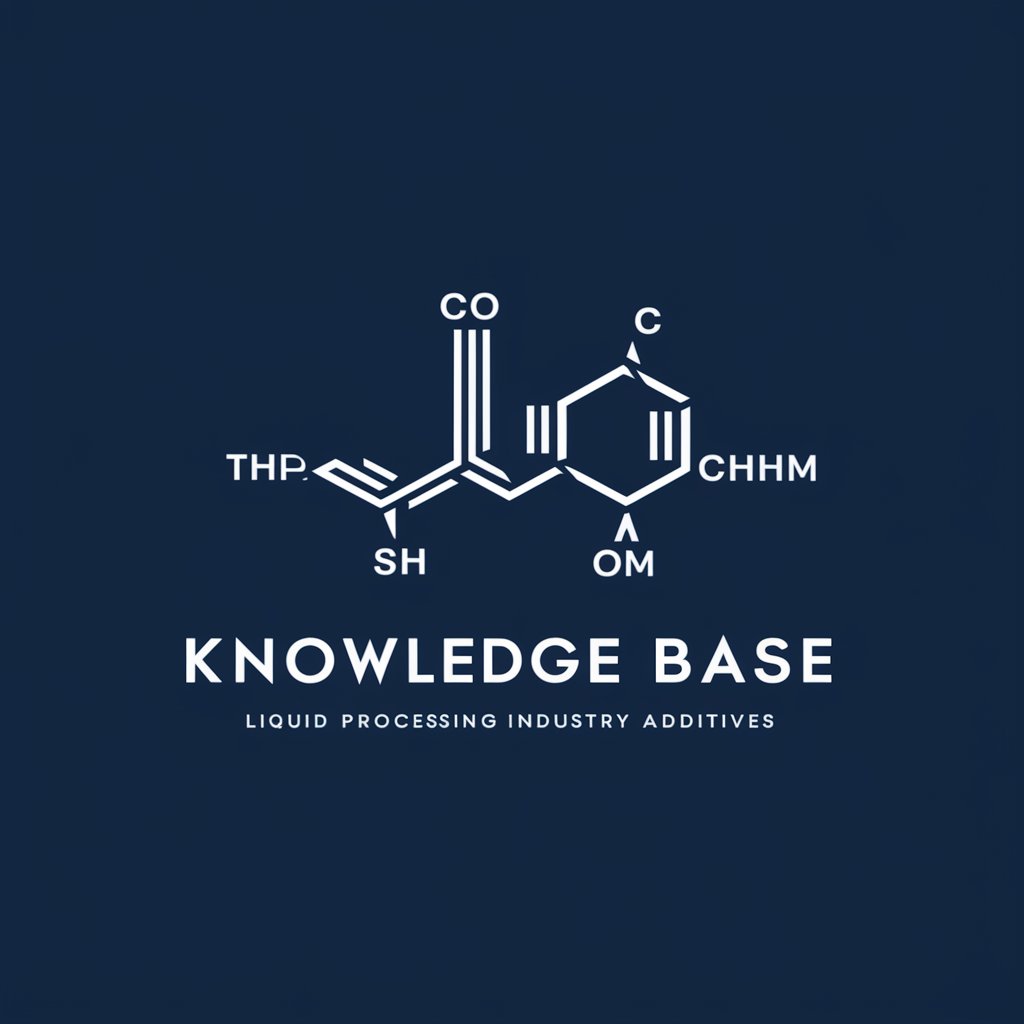
Welcome! How can I assist you with your additive needs today?
Empower your creations with AI-driven chemical expertise
Provide detailed information about the benefits of using defoamers in industrial applications.
Explain the working principles of adhesion promoters in paint formulations.
Describe the role of leveling agents in achieving smooth coatings.
Discuss the advantages of wetting agents in ink production.
Get Embed Code
Introduction to Resin, Pigment, Filler, Additive, Defoamer, Promoter
Resin, Pigment, Filler, Additive, Defoamer, Promoter are key components in the formulation of various chemical materials, each serving a distinct function. Resins form the backbone of formulations, providing structure and binding properties. Pigments add color and aesthetic qualities. Fillers enhance properties like strength, durability, and volume at lower costs. Additives fine-tune the formulation to improve performance in specific conditions, such as UV stability or flow characteristics. Defoamers prevent unwanted foam formation during manufacturing or application, ensuring a smooth finish. Promoters enhance the adhesion of coatings to substrates, ensuring long-term durability and resistance to environmental factors. An example scenario includes the creation of coatings for automotive applications, where these components work synergistically to provide corrosion resistance, vibrant color, and adherence to metal surfaces. Powered by ChatGPT-4o。
Main Functions and Real-World Applications
Resin
Example
Epoxy resins in coatings
Scenario
Provide structural integrity and chemical resistance to protective coatings for industrial flooring, enhancing durability against abrasions and chemical spills.
Pigment
Example
Titanium dioxide in paints
Scenario
Offers high refractive index to provide superior opacity and brightness, making it ideal for use in both interior and exterior paints for vibrant and long-lasting color.
Filler
Example
Calcium carbonate in plastics
Scenario
Improves mechanical properties such as strength and stiffness while reducing costs in plastic composites used in automotive parts.
Additive
Example
UV stabilizers in outdoor furniture coatings
Scenario
Protects against degradation from sunlight exposure, extending the life and appearance of outdoor furniture products.
Defoamer
Example
Silicone-based defoamers in cement mixes
Scenario
Prevents foam formation during the mixing and application of cement, ensuring a smoother, more consistent finish for construction projects.
Promoter
Example
Silane adhesion promoters in glass coatings
Scenario
Enhances the bonding between glass substrates and protective coatings, crucial for automotive and architectural applications requiring long-term durability and clarity.
Target User Groups
Coatings and Paint Manufacturers
Businesses specializing in the production of industrial, automotive, and architectural coatings and paints would benefit from these components by creating formulations tailored to specific performance criteria, such as corrosion resistance, color retention, and environmental sustainability.
Plastics and Composites Industry
Companies involved in manufacturing plastics and composite materials utilize fillers, additives, and promoters to enhance material properties, reduce production costs, and improve the end product's performance in applications ranging from automotive parts to consumer goods.
Printing and Packaging
This sector benefits from specialized pigments, defoamers, and additives that improve the quality and functionality of printed materials and packaging, such as food safety, visual appeal, and resistance to fading or environmental damage.
How to Use Resin, Pigment, Filler, Additive, Defoamer, Promoter
1
Begin with a visit to yeschat.ai for a no-login, free trial experience, embracing the simplicity and accessibility of our service.
2
Identify your specific needs or challenges related to resin, pigment, filler, additive, defoamer, or promoter to explore the most suitable options.
3
Utilize the detailed product information, including application guidelines, technical parameters, and safety storage tips, for informed decision-making.
4
Experiment with small-scale testing to ensure compatibility and performance meet your expectations before full-scale implementation.
5
For any further queries or detailed customization advice, reach out via email to enhance your experience and achieve optimal results.
Try other advanced and practical GPTs
中英文对照翻译
Seamless AI-Powered Bilingual Translations
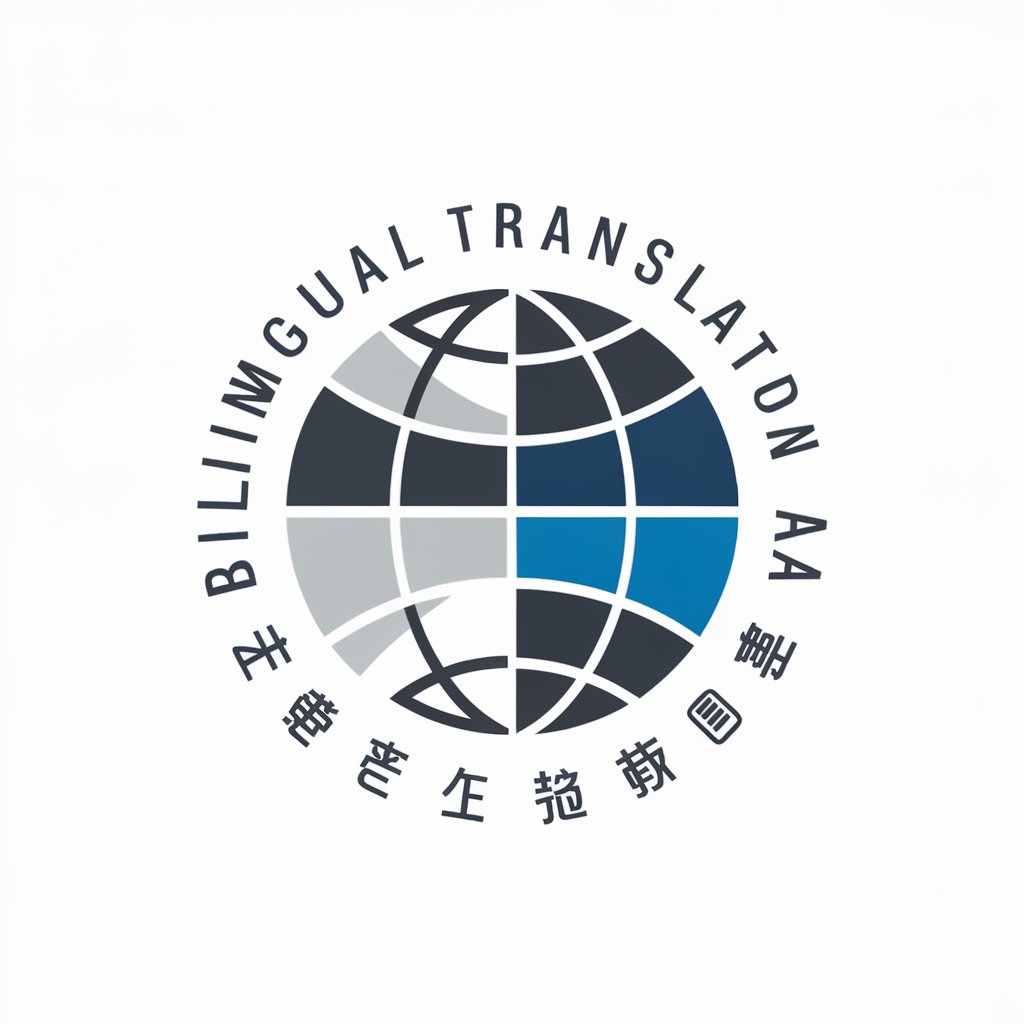
中英文对照翻译
Bridging Languages with AI Precision
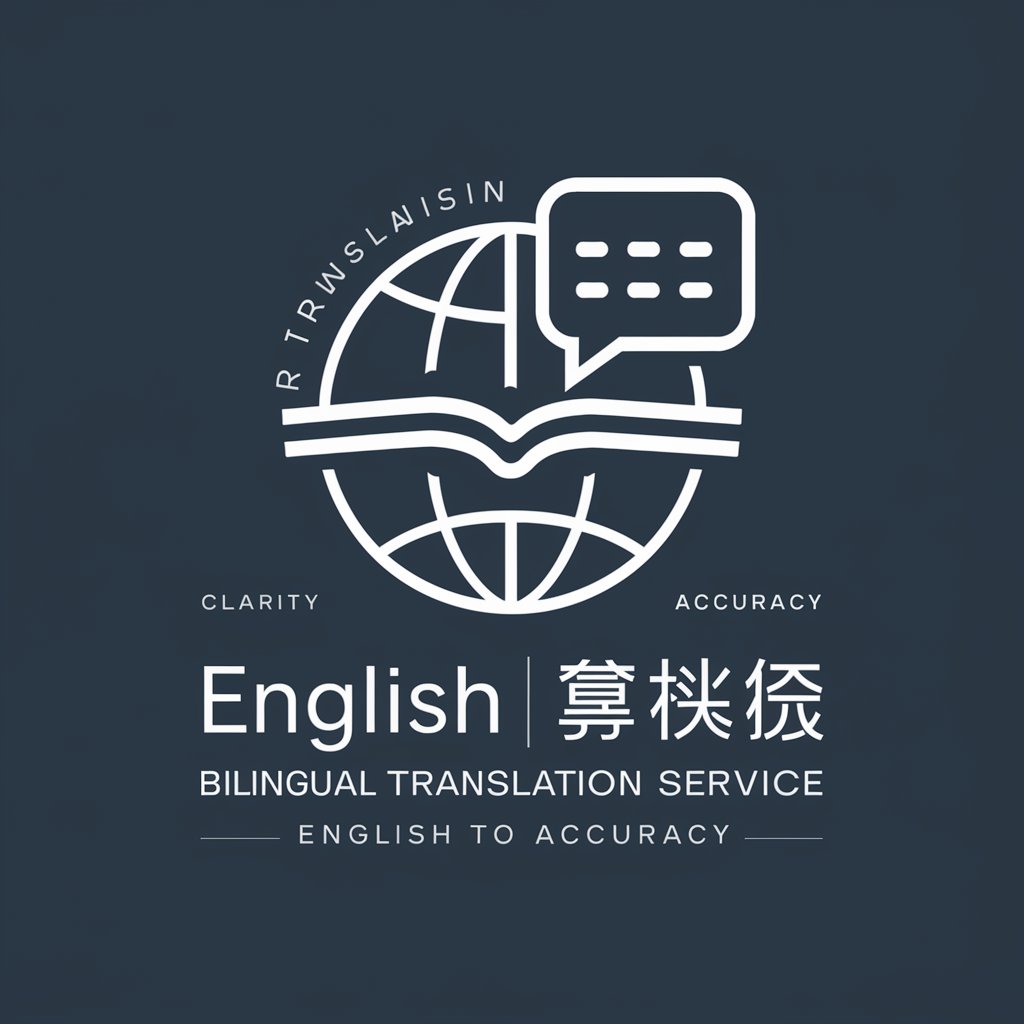
中英文对照翻译
Seamless AI-powered bilingual translation
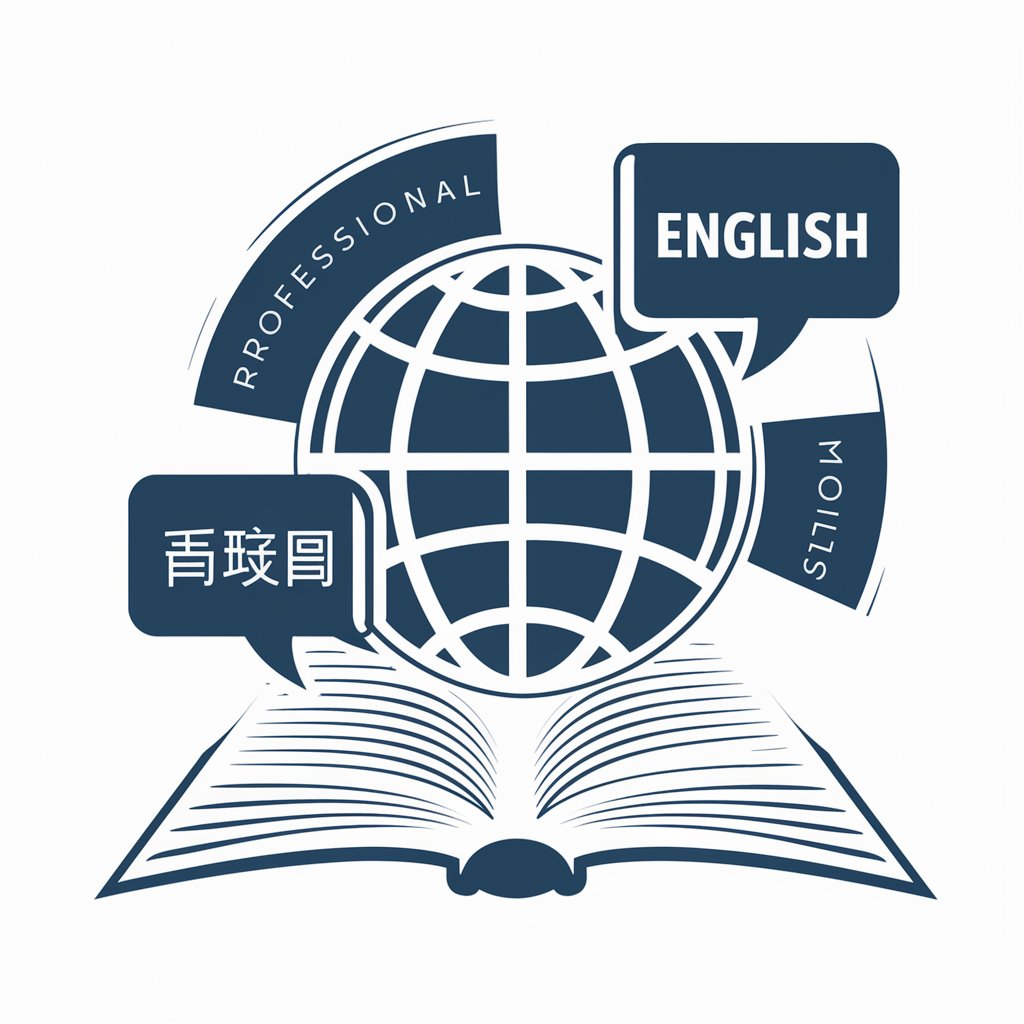
画意照影
Transforming photos into art with AI
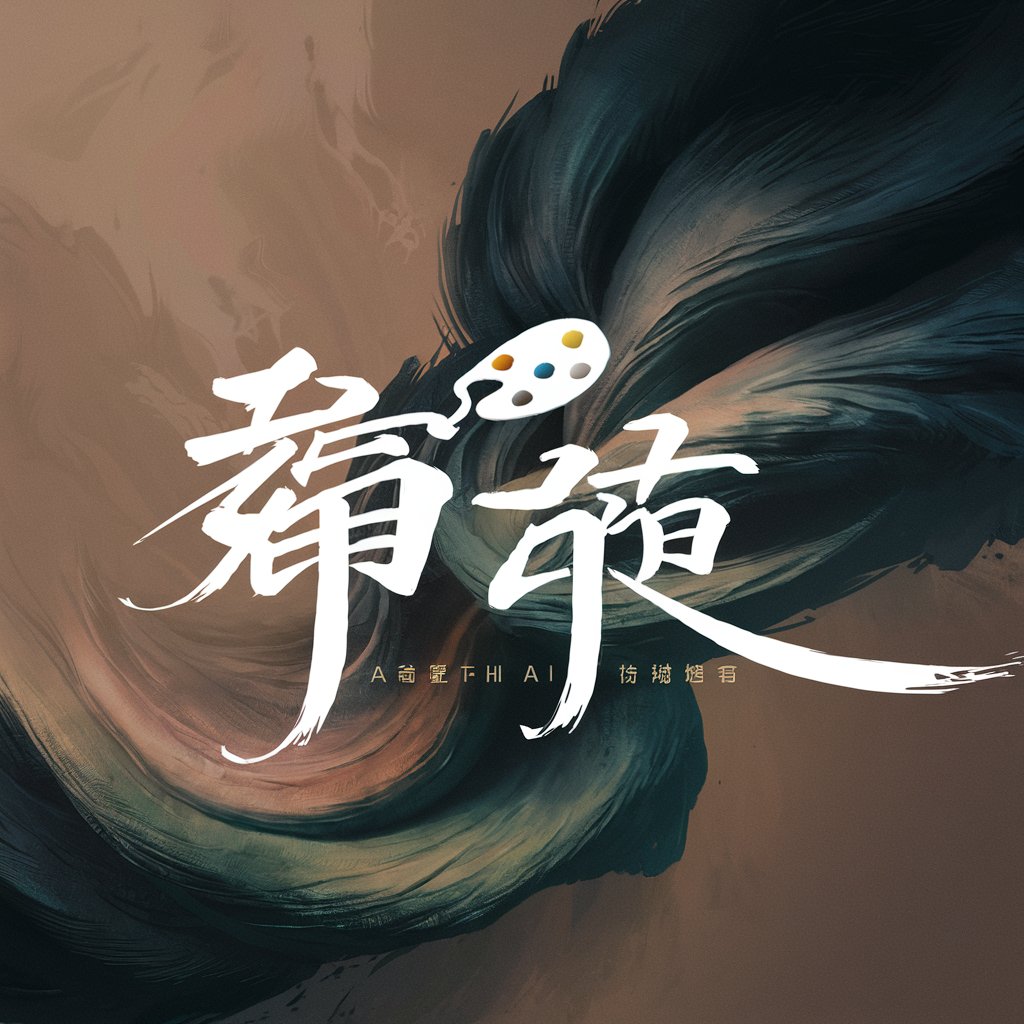
Android 底层向导
Empowering Android development with AI
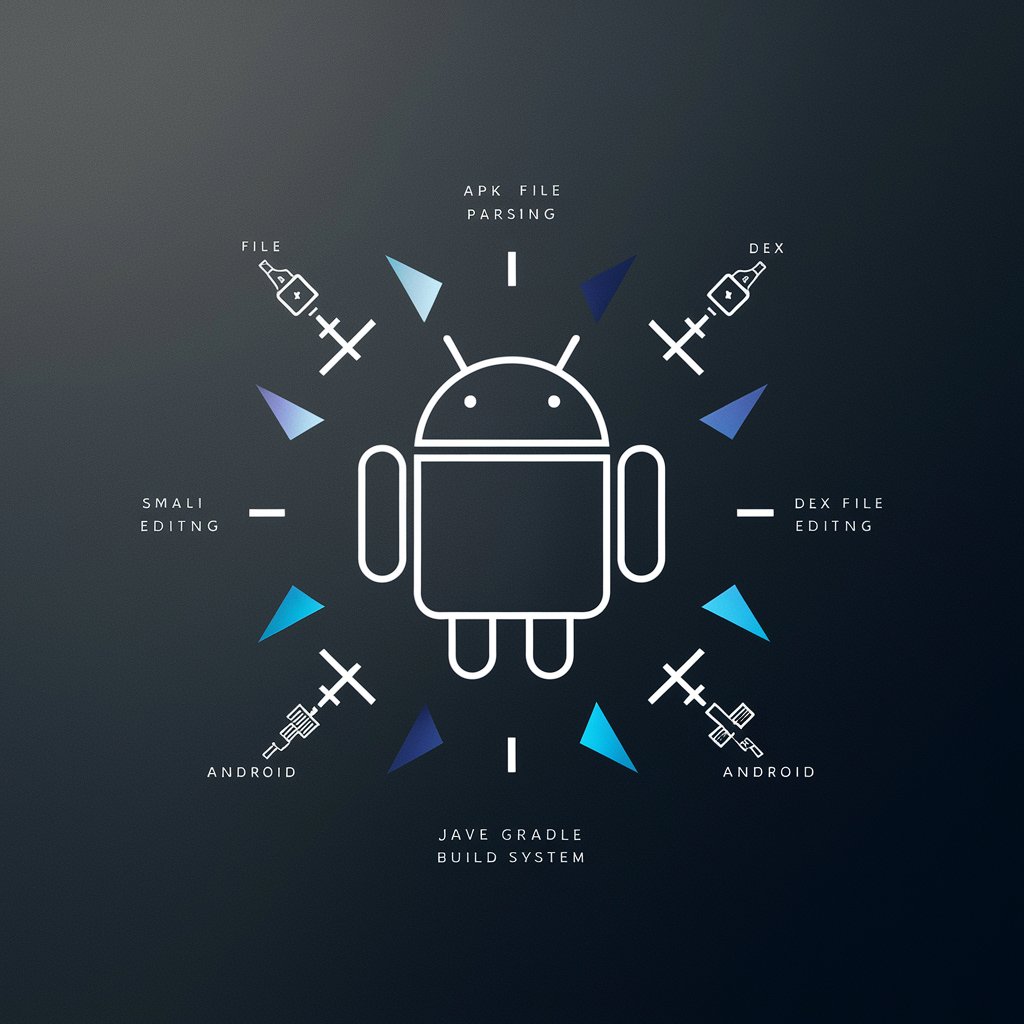
优云康盆底功能康复机器人
Empowering Pelvic Health with AI
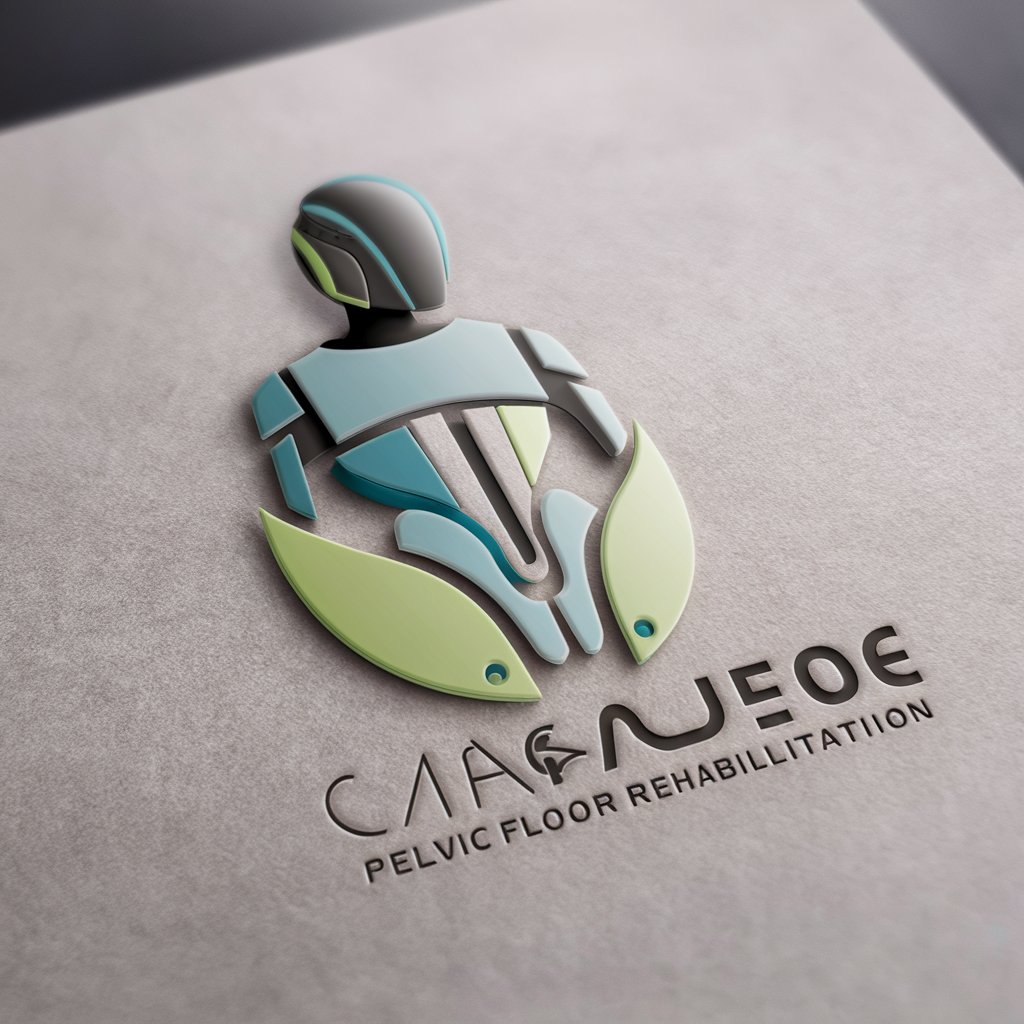
优质睡眠高手、睡觉(进一步咨询,请加我微信:415818818)
Optimize Your Sleep with AI-Powered Insights
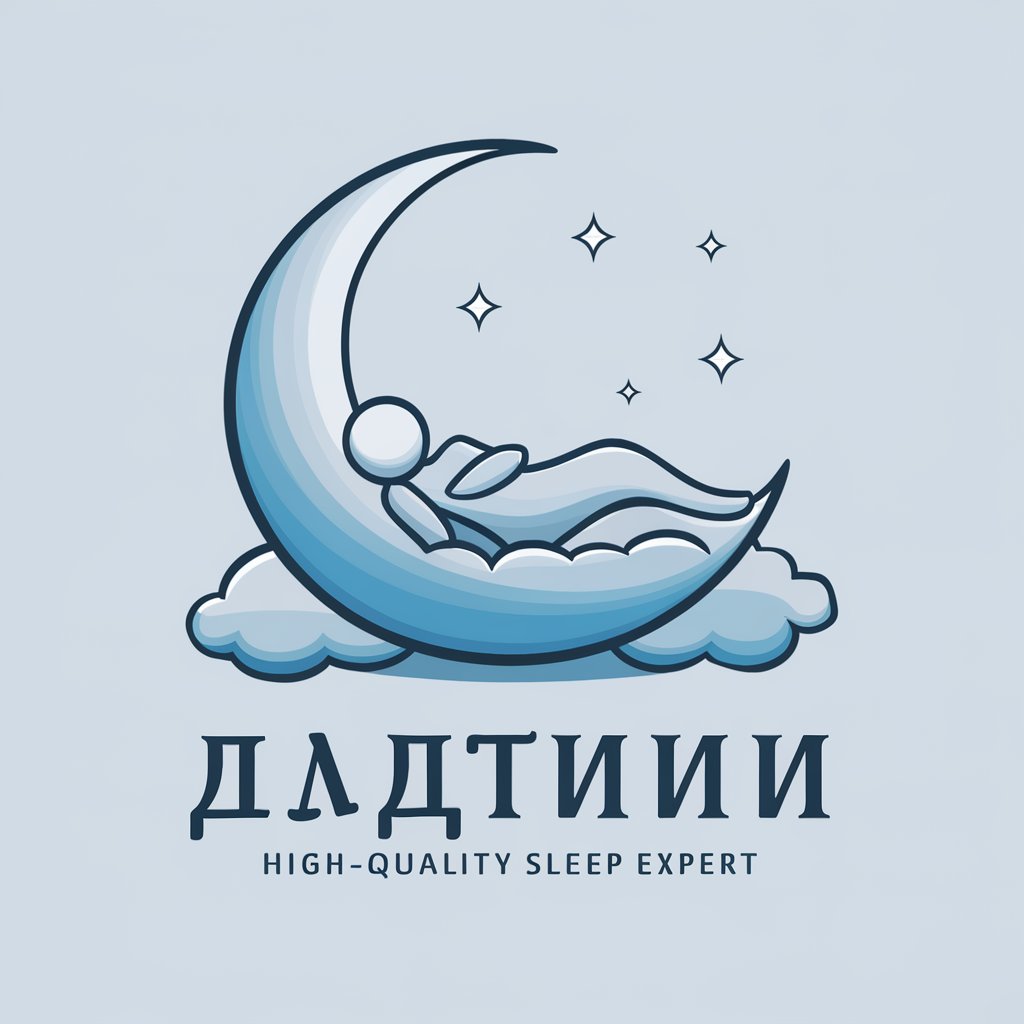
膨胀阻燃剂
Innovative flame retardancy with 膨胀阻燃剂
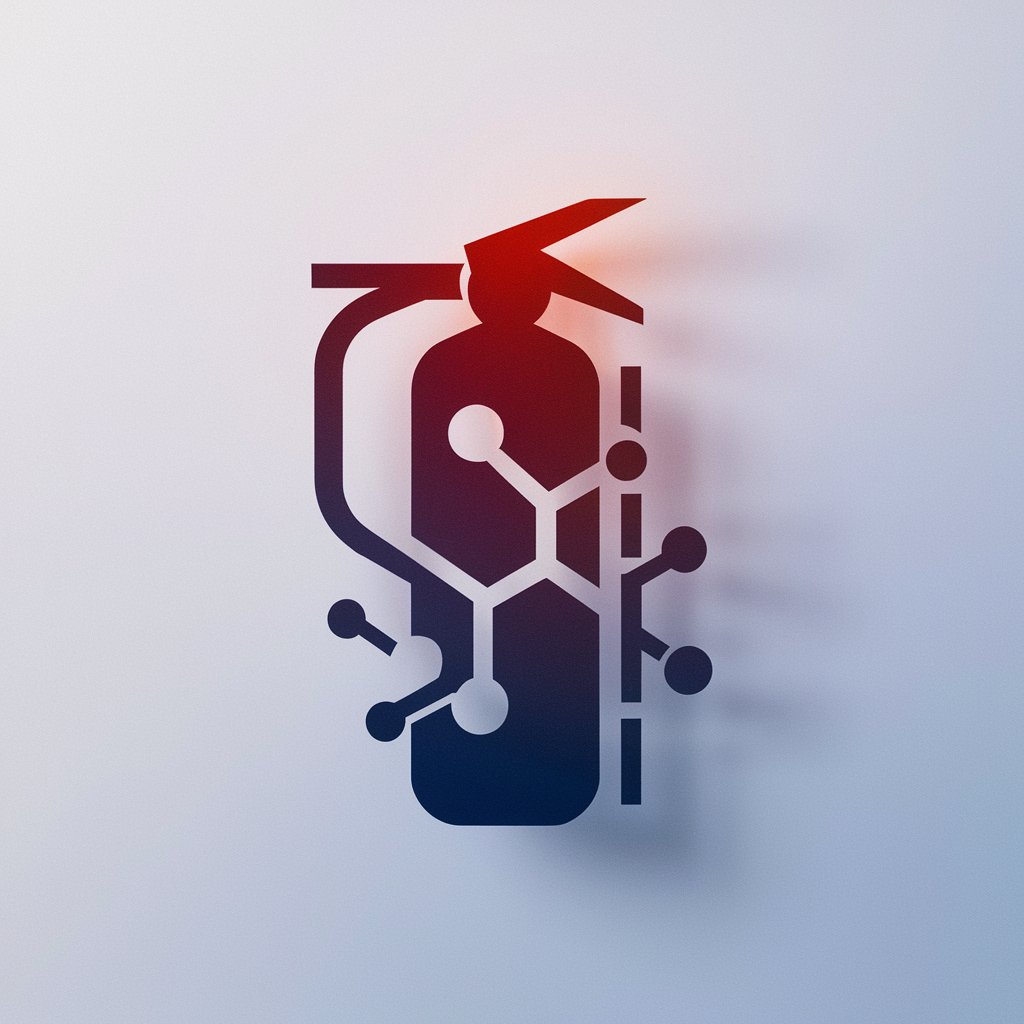
中药助手
Revolutionizing Traditional Medicine with AI
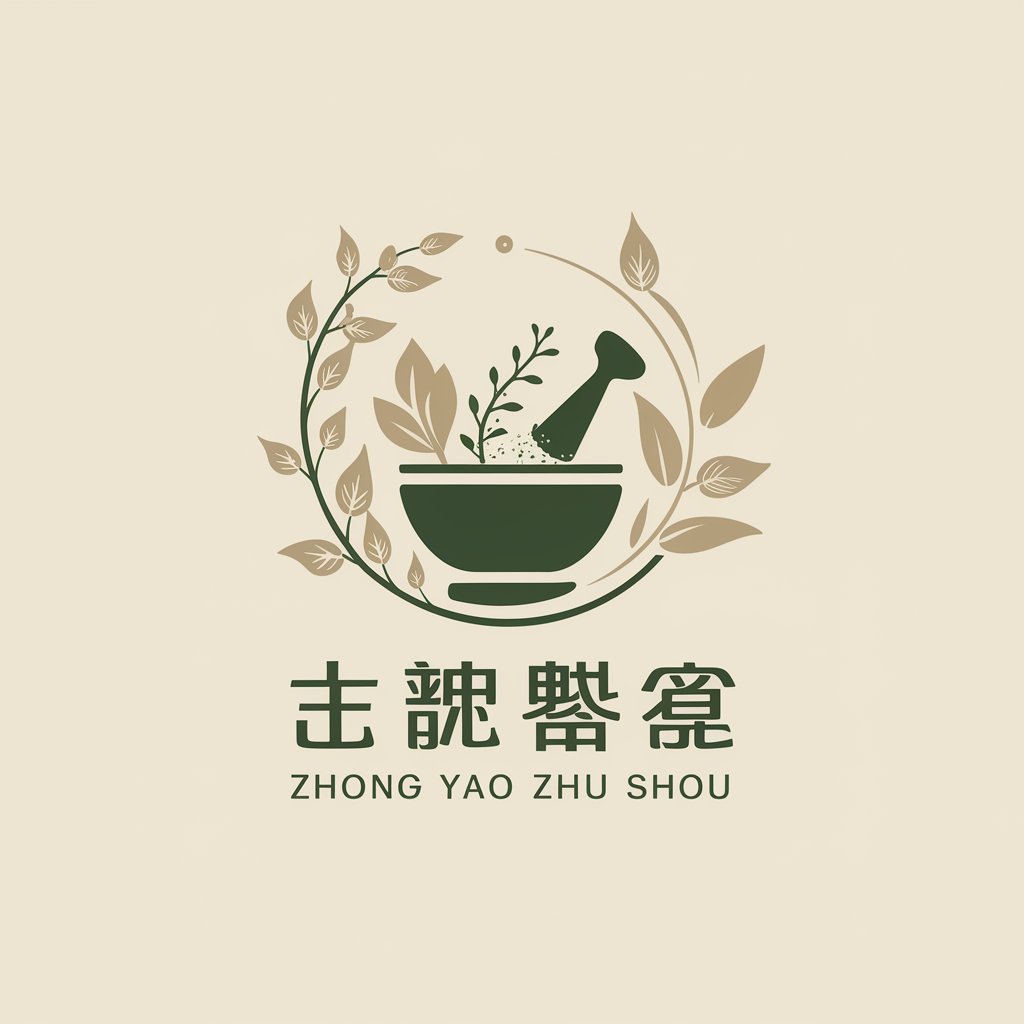
Shaanxi
Unlocking China with AI

Social Media Mastermind
Unleash Viral Potential with AI
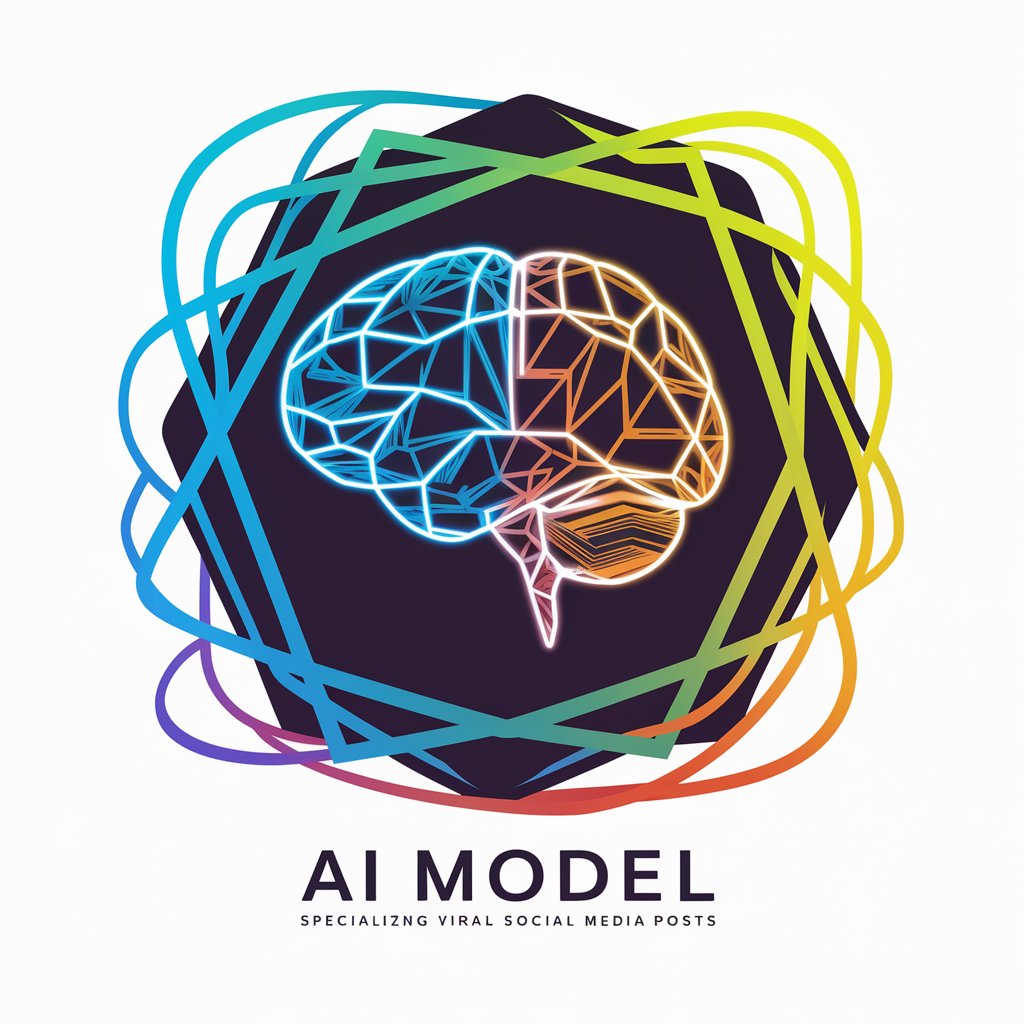
代碼測試及優化
Elevate Your Code with AI-Powered Optimization
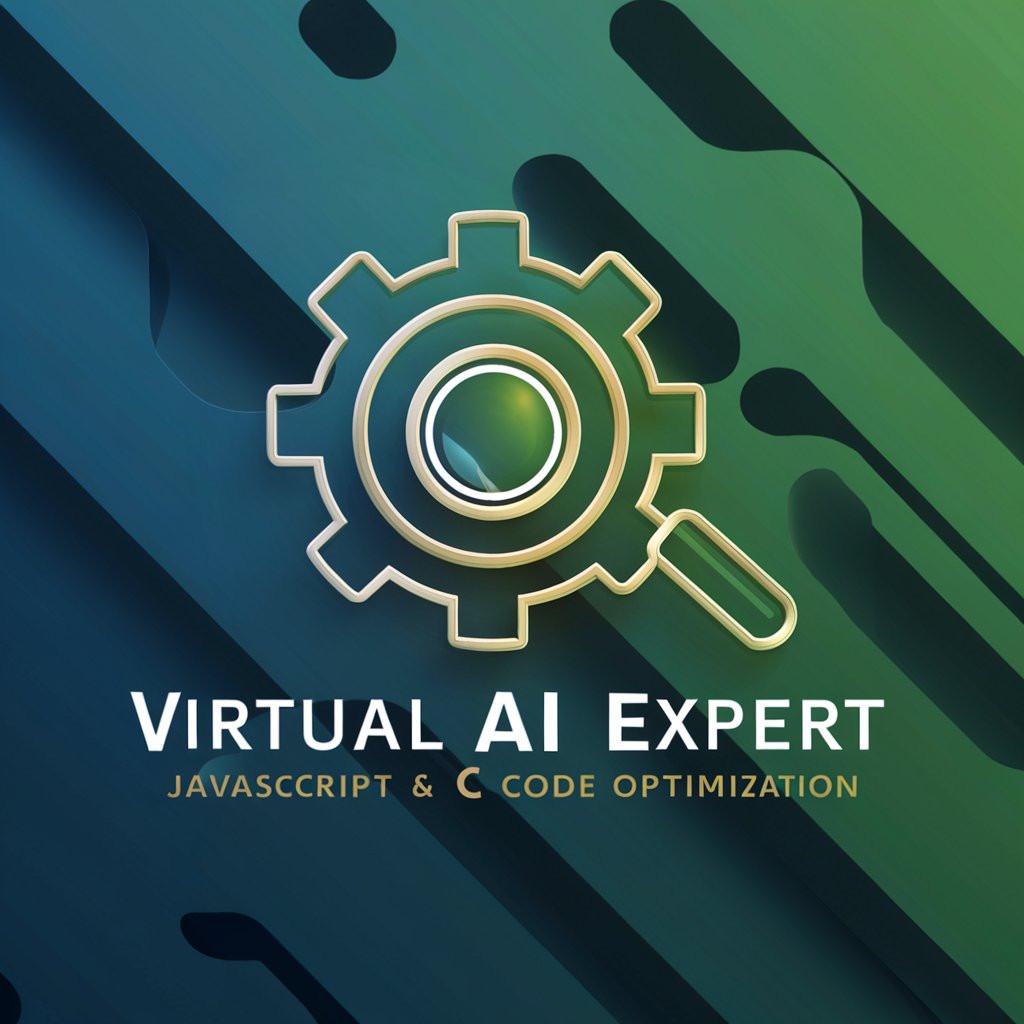
Detailed Q&A about Resin, Pigment, Filler, Additive, Defoamer, Promoter
What are the ideal conditions for storing pigment-based products?
Pigment-based products should be stored in a dry environment at temperatures between 10℃ and 25℃, with containers kept sealed to maintain their quality and effectiveness over a 12-month period.
How can I achieve the best rainbow effect using laser mirror silver paste?
For the most vivid rainbow effect, it's recommended to use the paste on smooth, transparent substrates, adjusting pigment particle size and the ink formulation with specific resins and solvents. Smaller particles yield a finer appearance, while larger ones create a brighter, coarser flash.
Can TPU adhesives be used on a variety of materials?
Yes, TPU adhesives are versatile and can effectively bond various materials, including PVC, PU, leather, and textiles, making them suitable for a wide range of applications from footwear to firefighting equipment.
What makes waterborne polyurethane dispersions (PUDs) environmentally friendly?
Waterborne PUDs are considered environmentally friendly due to their low VOC emissions, non-toxic nature, and the use of water as a solvent, which significantly reduces environmental impact compared to solvent-based systems.
How do I select the right defoamer for my application?
Selecting the right defoamer involves considering the medium you're working with, the application process, and desired outcomes. Test small quantities first to observe the defoaming effect and ensure it does not adversely affect the final product's appearance or performance.