Value Stream Mapping & Process Flow Tools - Process Optimization Tool
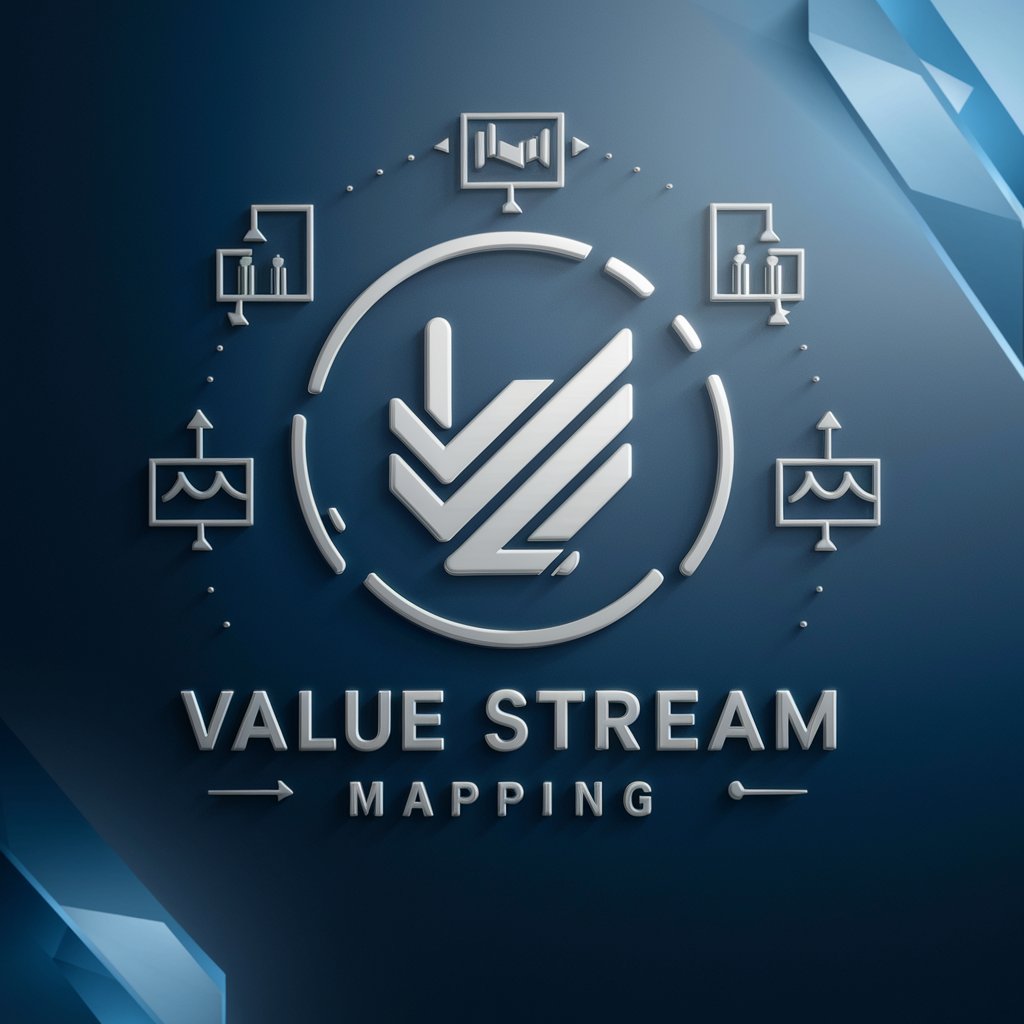
Welcome! Let's optimize your productivity and efficiency together.
Streamline workflows with AI-powered insights
How can I improve my time management skills?
What are the best practices for optimizing workflows?
Can you help me create a value stream map?
What strategies can I use to enhance my productivity?
Get Embed Code
Introduction to Value Stream Mapping & Process Flow Tools
Value Stream Mapping (VSM) and Process Flow Tools are methodologies and tools designed to help organizations visualize and analyze the flow of materials and information as a product or service makes its way through the value stream. The primary goal is to identify waste within the system and opportunities for improvement. VSM, for example, is a lean-management method that documents, analyzes, and improves the steps required to deliver a product or service from start to finish. Process Flow Diagrams (PFDs), on the other hand, are more focused on the detailed steps and decision points within individual processes. An example scenario where these tools are applied is in manufacturing, where a company might use VSM to map out the entire production process from receiving raw materials to delivering the final product to the customer, identifying bottlenecks, redundancies, or unnecessary steps that can be eliminated to improve efficiency and reduce costs. Powered by ChatGPT-4o。
Main Functions of Value Stream Mapping & Process Flow Tools
Visualization of Processes
Example
Creating a visual map of the production line in an automotive manufacturing plant.
Scenario
This allows managers and team members to see the entire process flow, including where materials are waiting or where there are delays in the process, enabling targeted interventions.
Identification of Waste
Example
Highlighting areas within a hospital's patient discharge process where redundant paperwork increases wait times.
Scenario
By mapping out each step in the discharge process, healthcare administrators can see where inefficiencies exist, such as duplicate form fillings or unnecessary approvals, and streamline the process.
Facilitation of Continuous Improvement
Example
Implementing VSM in an e-commerce company's order fulfillment process.
Scenario
Through regular value stream mapping exercises, the company identifies areas for improvement in their order packing and shipping process, leading to faster delivery times and higher customer satisfaction.
Enhancement of Collaboration and Communication
Example
Using process flow diagrams to facilitate cross-departmental meetings in a software development company.
Scenario
The diagrams help different departments understand how their work affects others in the product development lifecycle, fostering a collaborative environment and reducing silos.
Ideal Users of Value Stream Mapping & Process Flow Tools
Manufacturing Companies
These organizations benefit from VSM and PFDs by identifying inefficiencies in production processes, reducing costs, and increasing output quality.
Healthcare Organizations
Hospitals and clinics use these tools to improve patient flow, reduce waiting times, and enhance the quality of care through more efficient administrative and clinical processes.
Service Industries
Companies in sectors such as finance, hospitality, and IT can use VSM to optimize service delivery processes, enhancing customer satisfaction and loyalty.
Lean Consultants and Continuous Improvement Specialists
Professionals who specialize in lean management and continuous improvement initiatives use these tools to guide organizations in various industries towards more efficient and effective processes.
Guidelines for Using Value Stream Mapping & Process Flow Tools
Start with a Free Trial
Begin by accessing a complimentary trial at yeschat.ai, where you can explore the features without the need for signing in or subscribing to a premium service.
Identify Your Process
Select a specific process or workflow within your organization that you wish to analyze and improve. Common use cases include manufacturing processes, administrative tasks, and service delivery.
Map the Current State
Using the tool, visually map out all the steps in the current process, including inputs, outputs, and flow of information or materials. This helps in identifying bottlenecks and waste.
Analyze and Design the Future State
Leverage the tool to analyze the current state map, identify areas for improvement, and design a future state map that optimizes the process flow and reduces inefficiencies.
Implement and Monitor
Apply the changes in your process based on the future state map. Use the tool to monitor the process continuously and make adjustments as needed for ongoing improvement.
Try other advanced and practical GPTs
Kafka's Scream
Deep insights into life's existential dilemmas.
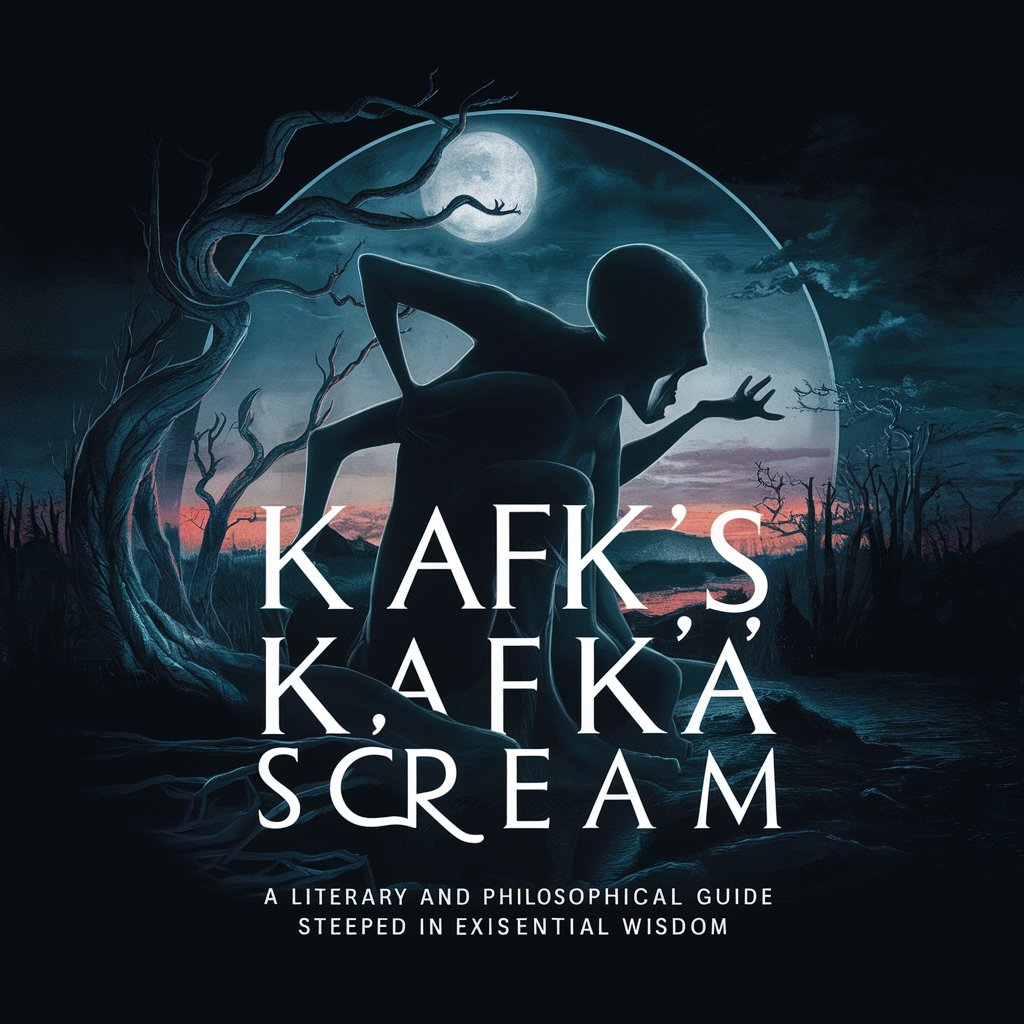
Stream Scout
Navigate Ozark Streams with AI-Powered Insights
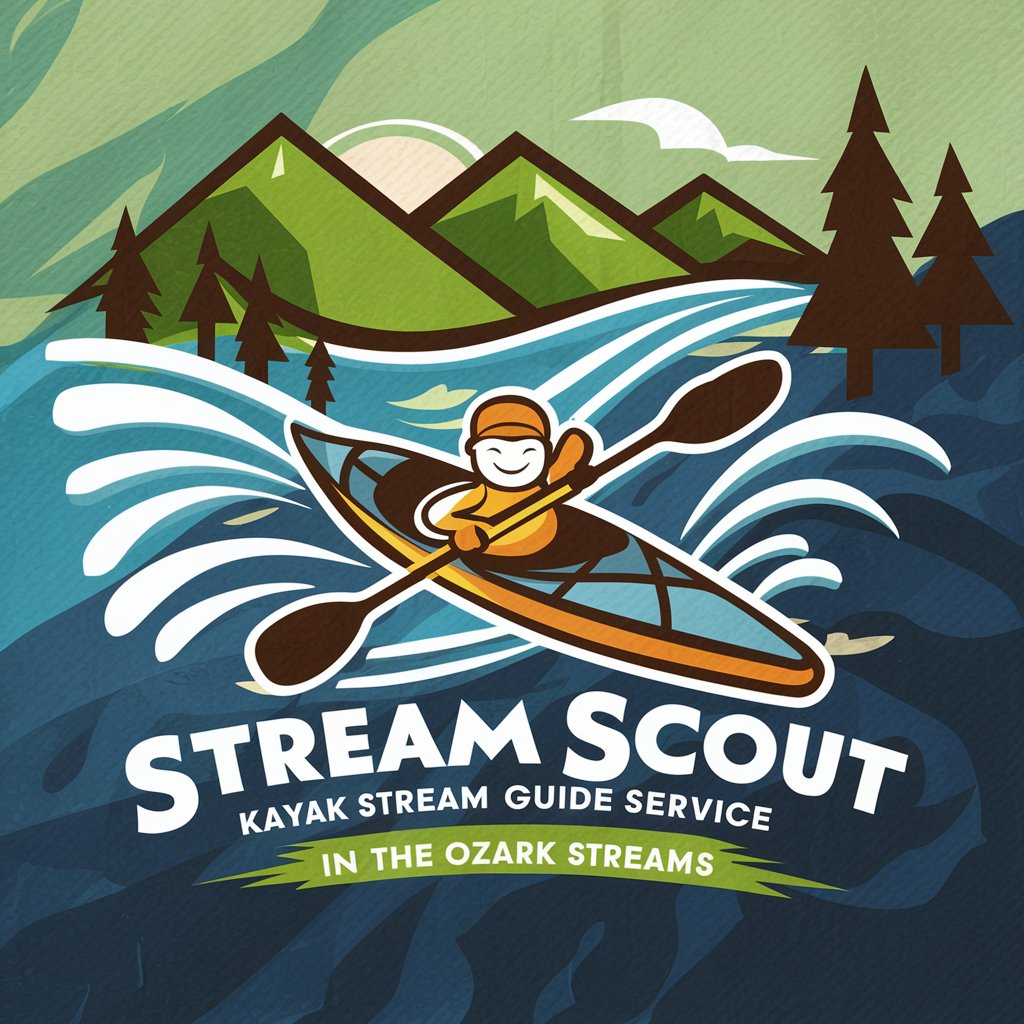
Idea Stream
Elevate Creativity with AI-Powered Ideas
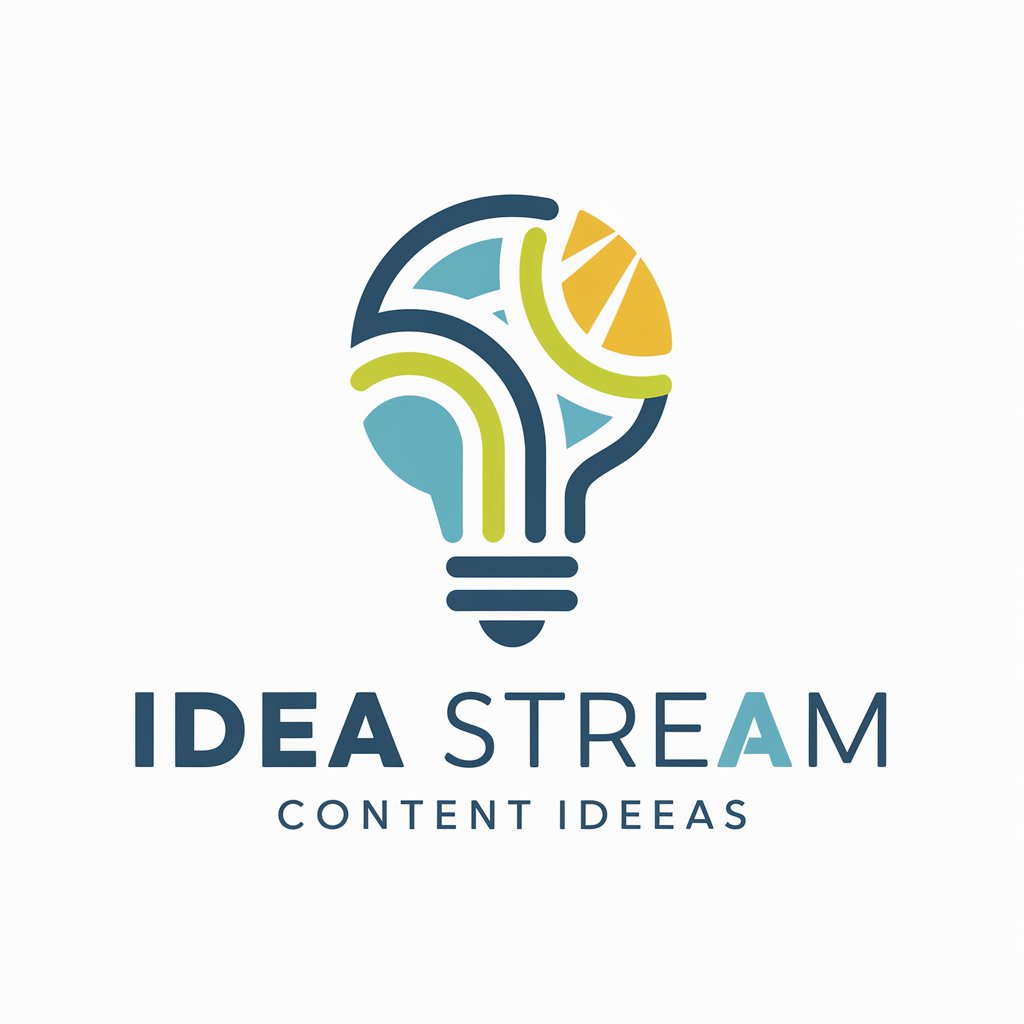
Scream Seeker
Empowering your thrill-seeking journey with AI
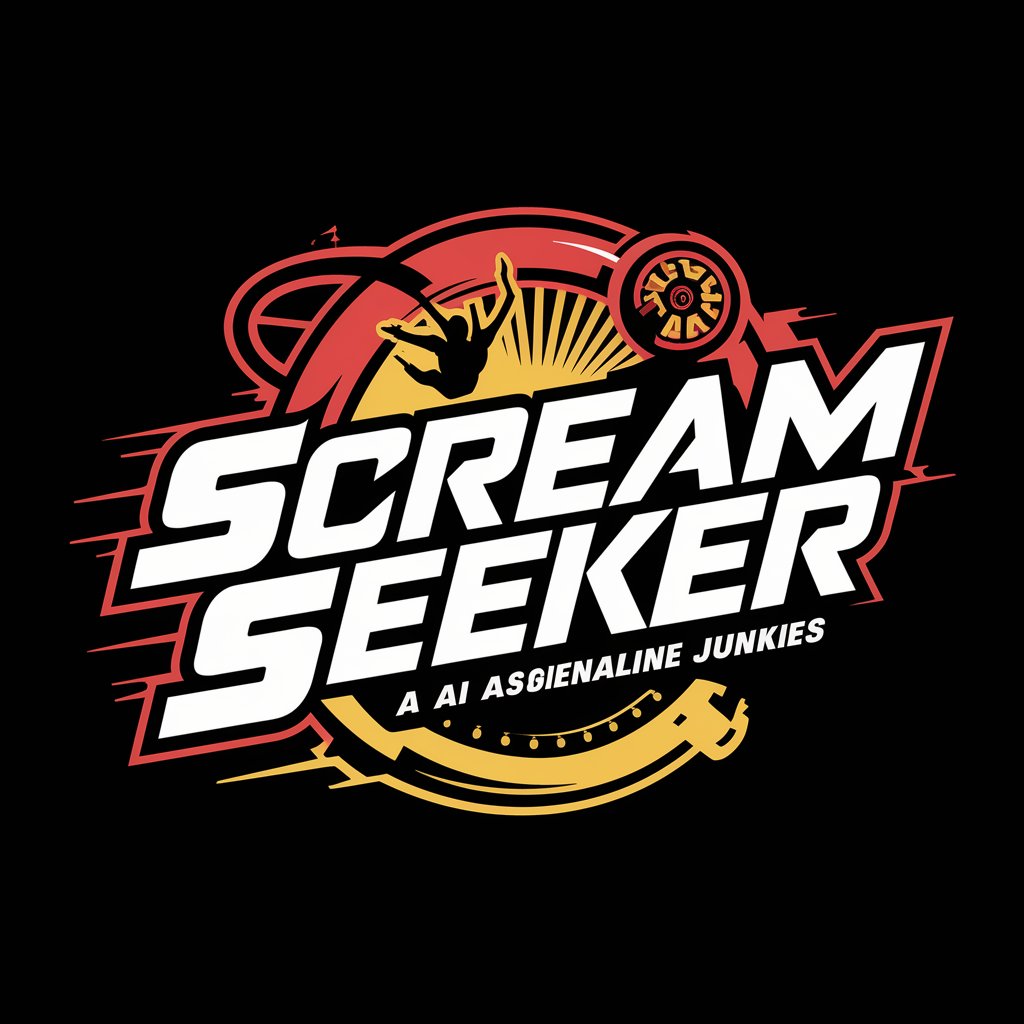
Skalable Stream
Empower Your Workflow with AI
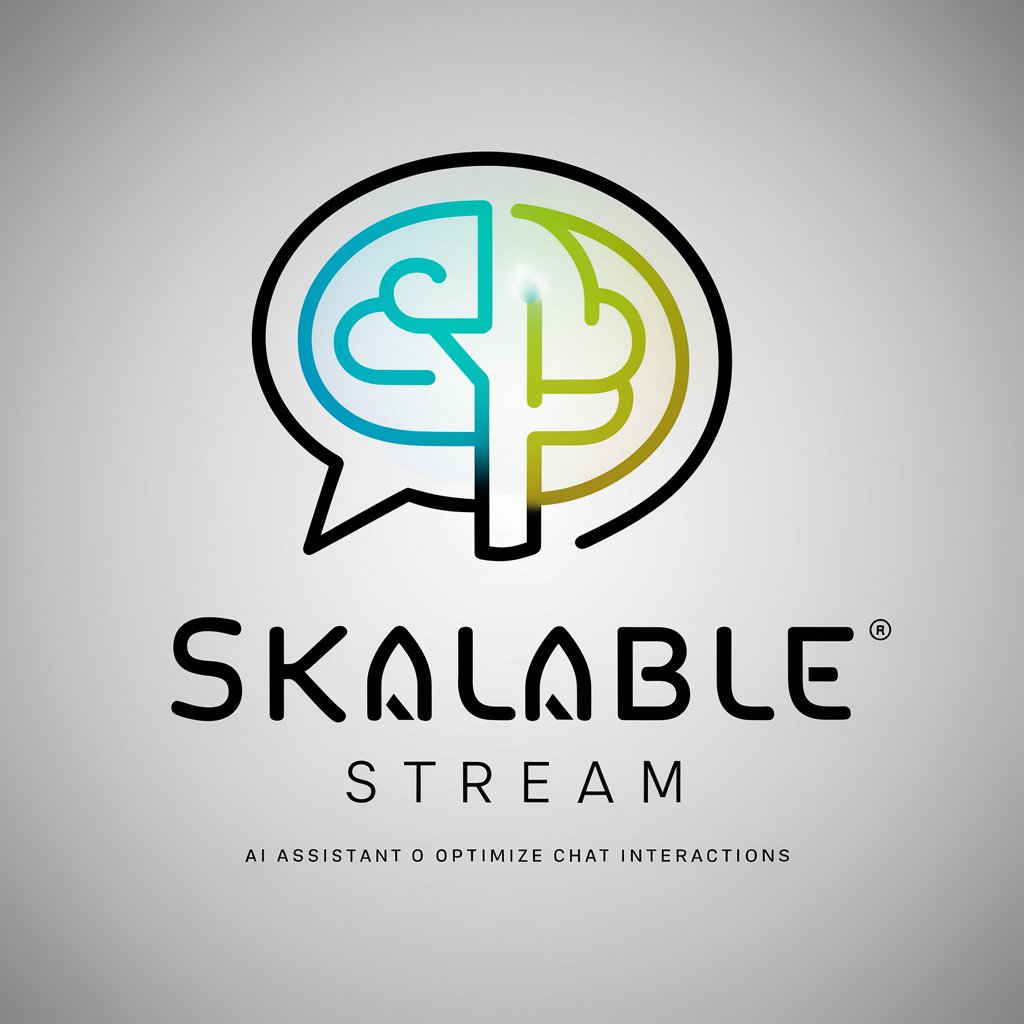
Stream Guide
AI-Powered Streaming Navigator
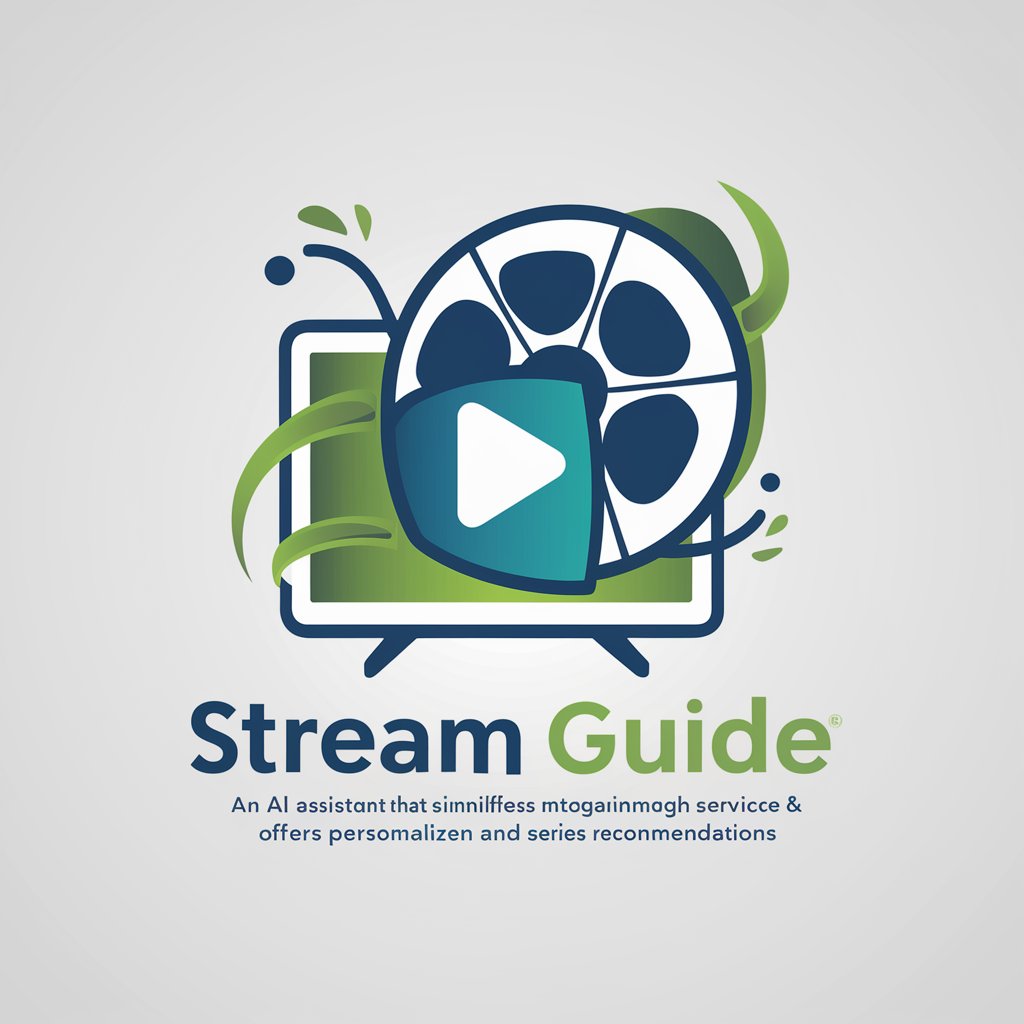
Income Stream Surfer's General ContentGPT
Powering Content with AI Creativity
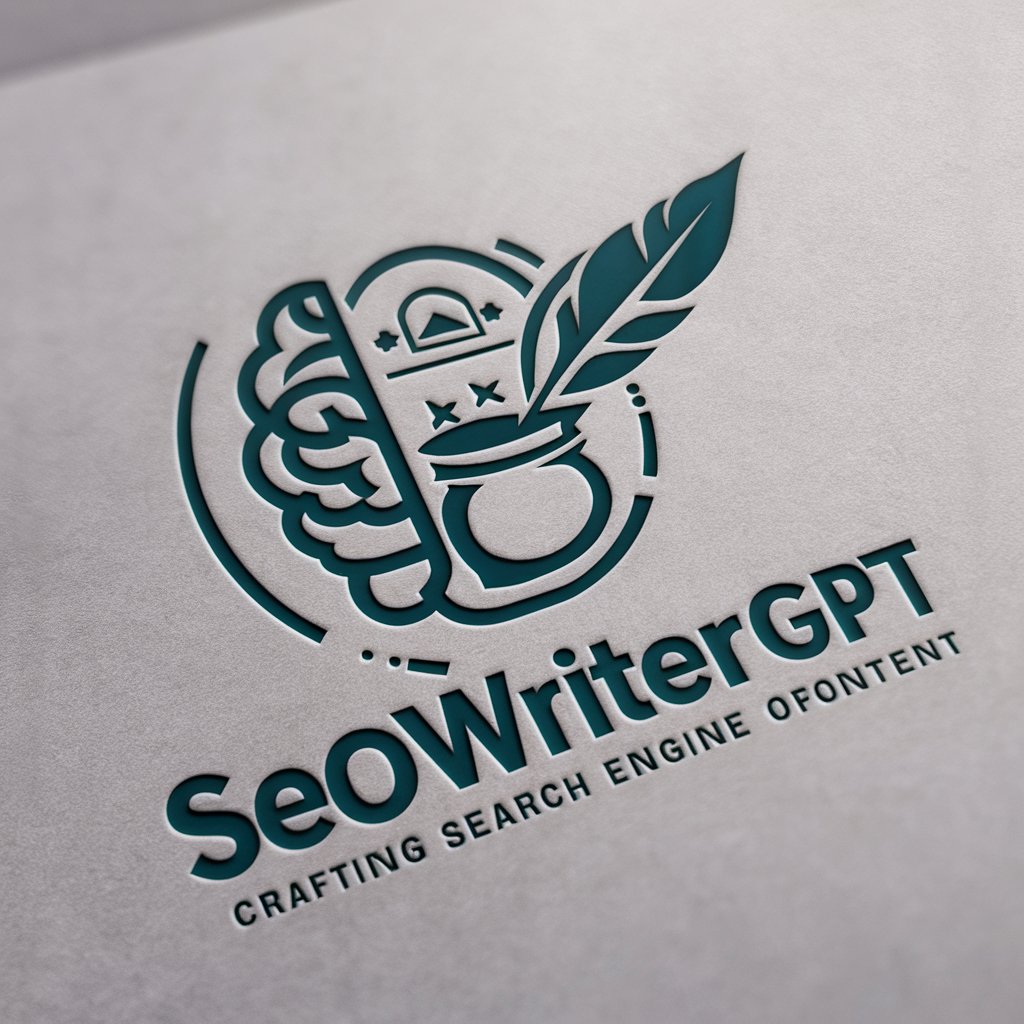
Hope Companion
Empathy at your fingertips, powered by AI
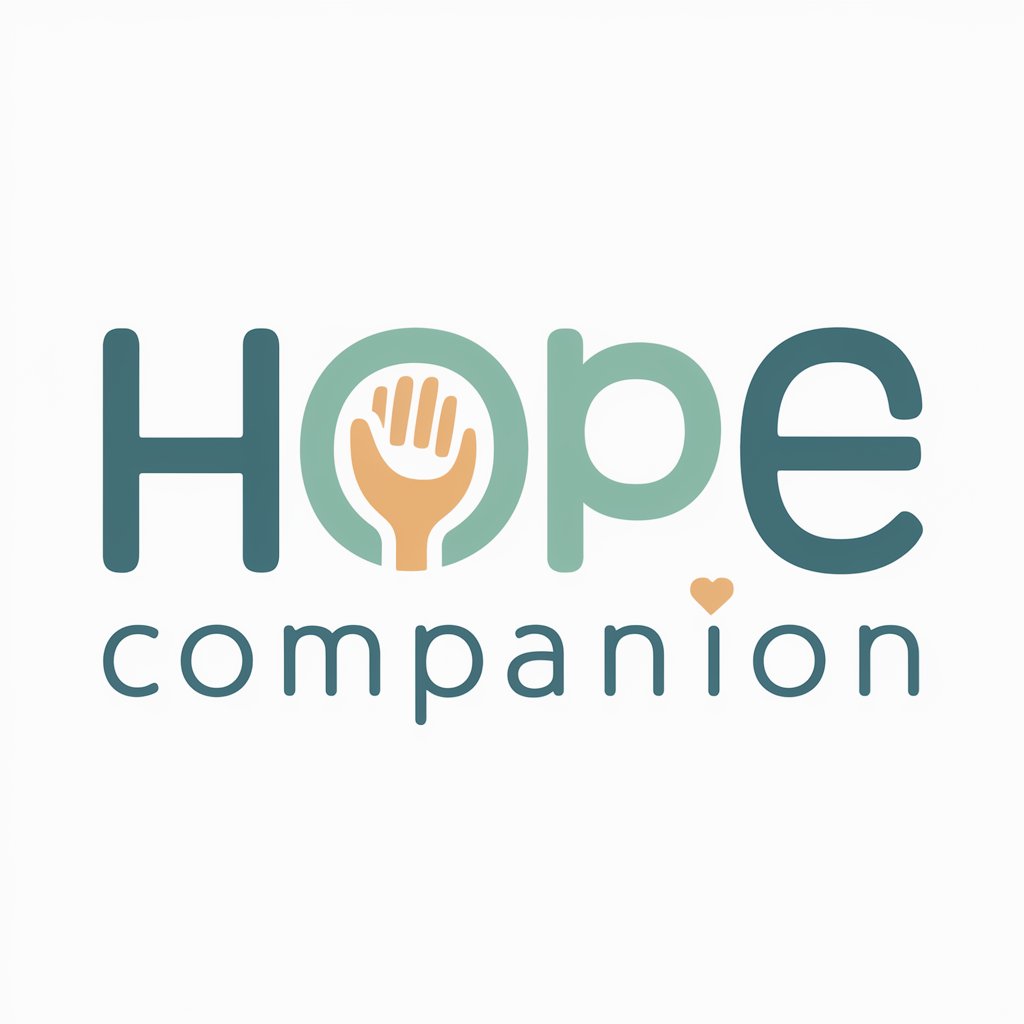
Hope Companion
Empowering emotional resilience with AI
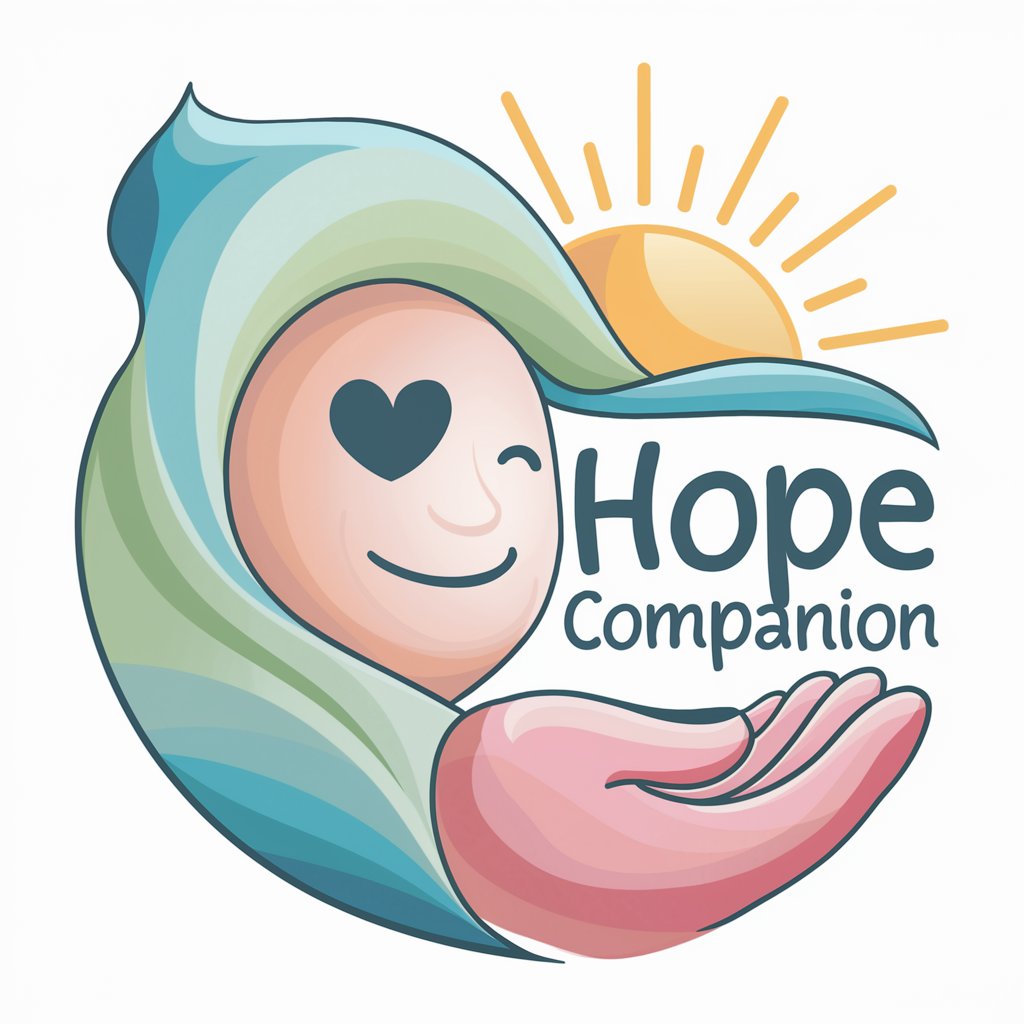
Ally Hope
Enhancing Conversations with AI-Powered Memory
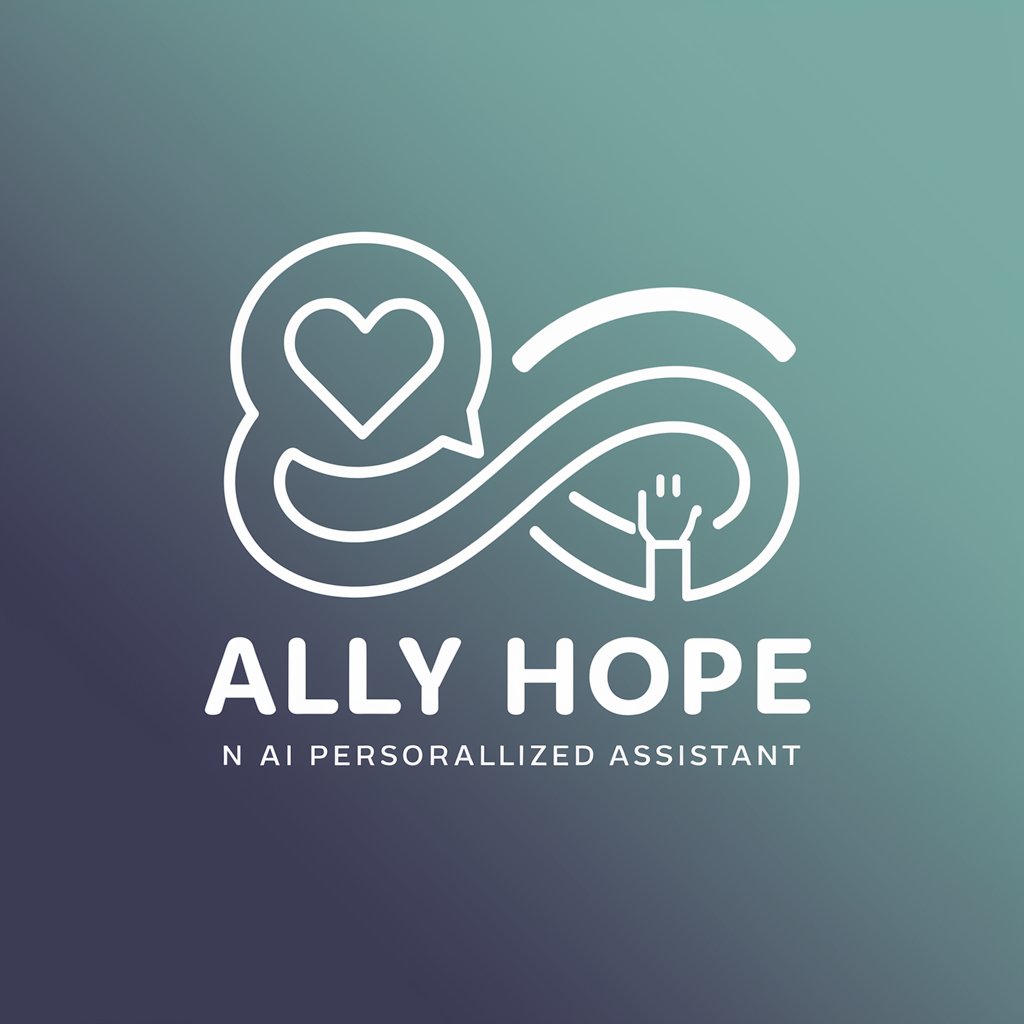
Hope AI
Empathetic AI for Life's Challenges
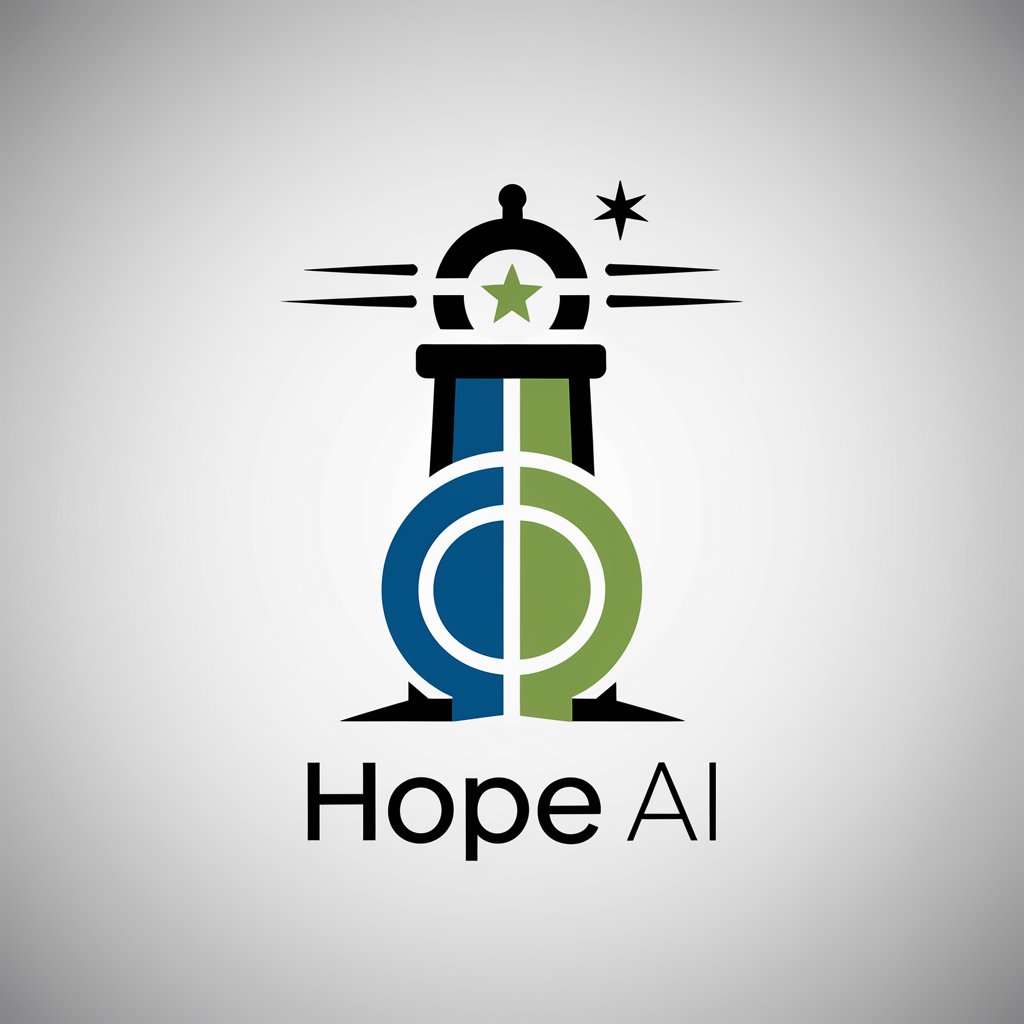
Hope Ally
Elevating spirits with AI support
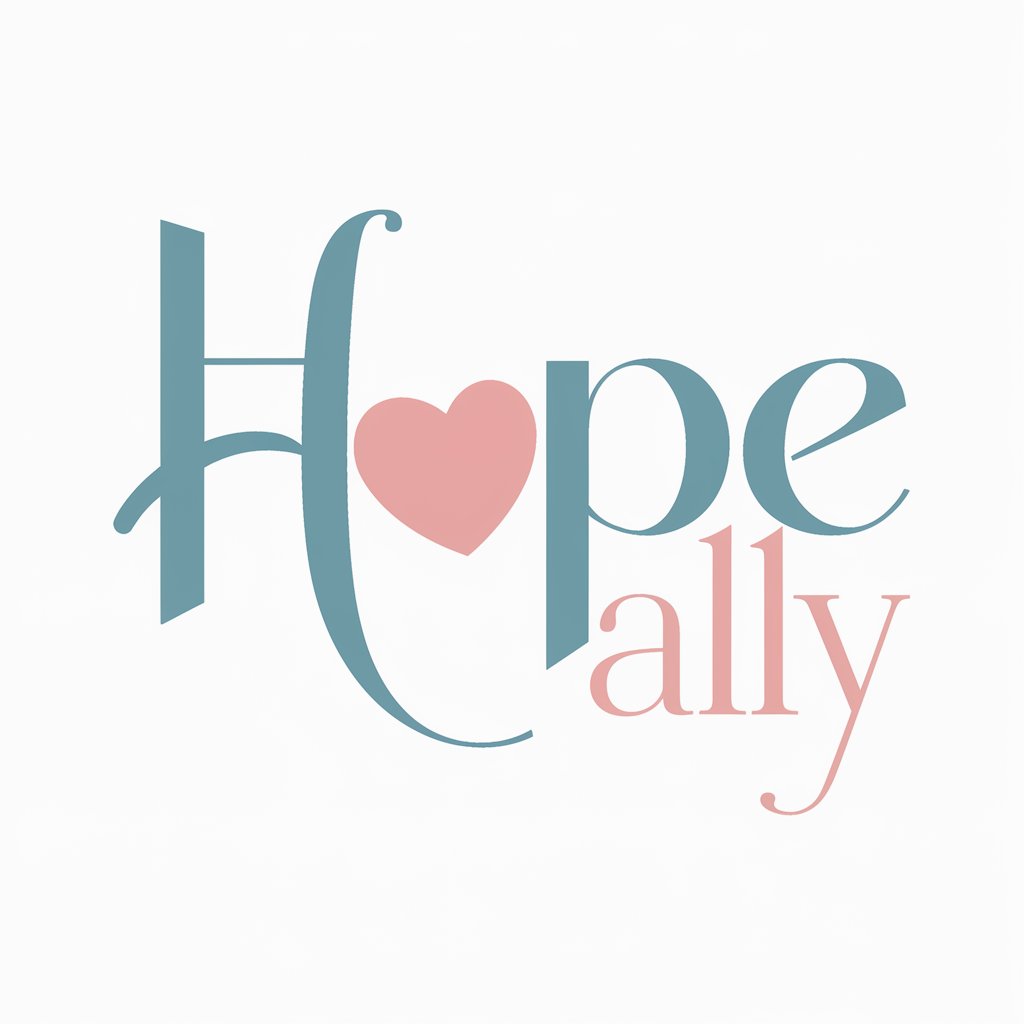
Value Stream Mapping & Process Flow Tools FAQ
What is Value Stream Mapping?
Value Stream Mapping is a visual tool used to analyze and design the flow of materials and information required to bring a product or service to a consumer. It helps identify waste and streamline processes.
How can Value Stream Mapping benefit my business?
It can enhance operational efficiency by identifying bottlenecks, reducing lead times, improving product quality, and optimizing resource utilization, ultimately leading to cost savings and better customer satisfaction.
Can I use these tools for non-manufacturing processes?
Yes, these tools are versatile and can be applied to a wide range of processes, including administrative, service-oriented, and software development processes, to improve efficiency and productivity.
Do I need any prior experience to use these tools?
While prior experience can be beneficial, many tools are designed with user-friendly interfaces and provide tutorials or guides to help beginners understand and apply the principles of value stream mapping and process flow analysis.
How often should I update my Value Stream Maps?
It's advisable to review and update your maps regularly, especially when there are significant changes in your processes, to ensure they accurately reflect the current state and to identify new opportunities for improvement.