CNC - CNC Design and Manufacturing Guide
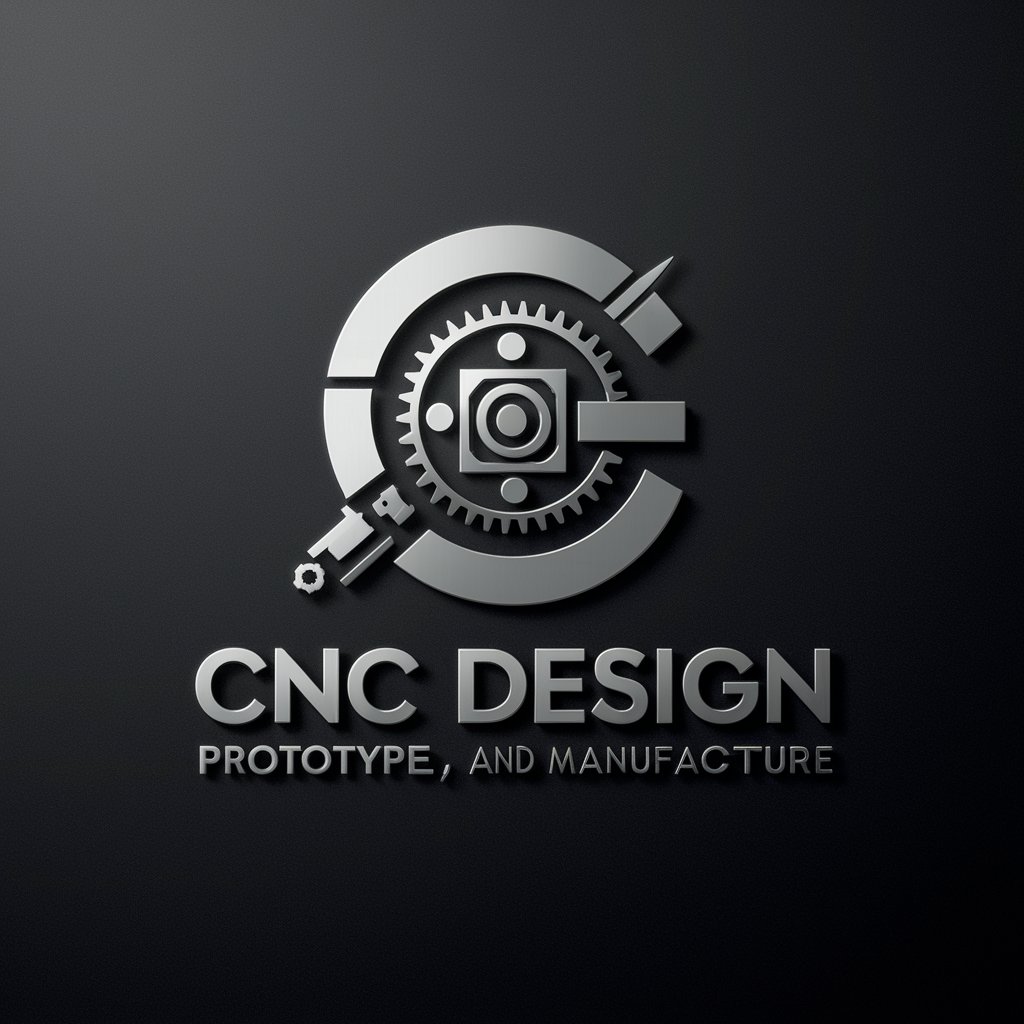
Welcome! Let's bring your CNC designs to life with precision and expertise.
Precision Manufacturing with AI
How can I optimize the CNC design for my project to improve accuracy and precision?
What are the best maintenance practices for ensuring long-term reliability of my CNC machine?
Can you help me troubleshoot a specific issue I'm experiencing with my CNC setup?
What materials and settings should I use to achieve the best results in my CNC manufacturing process?
Get Embed Code
Overview of CNC
CNC, which stands for Computer Numerical Control, encompasses a wide range of computer-controlled machines used for precisely cutting, shaping, and machining material to create parts or products. This technology transforms digital design files into pre-programmed instructions for the machinery, automating complex, precise, and repetitive manufacturing tasks. Unlike manual machining, CNC offers enhanced accuracy, efficiency, and consistency. Examples of CNC machines include routers, lathes, mills, and grinders, each tailored for specific tasks. For instance, CNC routers are commonly used for cutting wood, composites, and plastics in intricate shapes for furniture, sign making, and architectural details, demonstrating the technology's adaptability to various materials and designs. Powered by ChatGPT-4o。
Key Functions of CNC
Precision Machining
Example
Manufacturing aerospace components
Scenario
CNC machines are employed to produce complex parts with tight tolerances required in aerospace applications. This involves precise cutting and drilling of advanced materials to achieve components that meet rigorous safety and performance standards.
Rapid Prototyping
Example
Developing new consumer electronics
Scenario
CNC machining facilitates the rapid creation of prototypes for consumer electronics, allowing designers to test and refine the ergonomics, functionality, and aesthetics of products such as smartphone cases or laptop bodies before mass production.
Custom Fabrication
Example
Creating bespoke furniture
Scenario
For custom furniture makers, CNC routers enable the cutting and shaping of wood and other materials into unique pieces. This function allows for the production of personalized items that fit specific dimensions and design preferences.
Mass Production
Example
Automotive parts manufacturing
Scenario
In the automotive industry, CNC machines are pivotal for mass-producing parts with consistency and efficiency. They are used to machine engine components, gearbox parts, and other critical items that require uniformity across thousands of units.
Ideal Users of CNC Services
Manufacturers and Fabricators
This group includes entities involved in the mass production of goods, automotive parts, aerospace components, and custom fabrication. They benefit from CNC's precision, speed, and ability to produce complex parts consistently.
Designers and Engineers
Professionals in design and engineering utilize CNC for prototyping and testing designs. The technology's precision and flexibility in material use make it invaluable for developing new products and improving existing ones.
Small Business Owners and Entrepreneurs
For those in small-scale manufacturing, custom crafts, and startups, CNC offers the tools to create detailed, high-quality products without requiring large-scale industrial facilities. This accessibility supports innovation and customization in various industries.
Educators and Researchers
Academic and research institutions use CNC technology to teach manufacturing principles, conduct experiments, and develop new machining techniques. It serves as a practical tool for students and researchers to apply theoretical knowledge in real-world scenarios.
Guidelines for Utilizing CNC Technology
Start with a Free Trial
Begin by exploring CNC capabilities with a free trial at yeschat.ai, accessible without the need for login or a ChatGPT Plus subscription.
Design Your Part
Create a detailed CAD model of the part you want to manufacture. Ensure accuracy in dimensions and geometry for optimal machining.
Choose Material and Tools
Select the appropriate material for your part and the correct cutting tools based on the material's properties and your design's requirements.
Set Up the CNC Machine
Prepare your CNC machine by setting up the workpiece, installing the necessary tools, and inputting the machining parameters.
Run and Monitor
Execute your CNC program, closely monitoring the process to make adjustments as needed for precision and quality.
Try other advanced and practical GPTs
美股通
Empowering Investment Decisions with AI
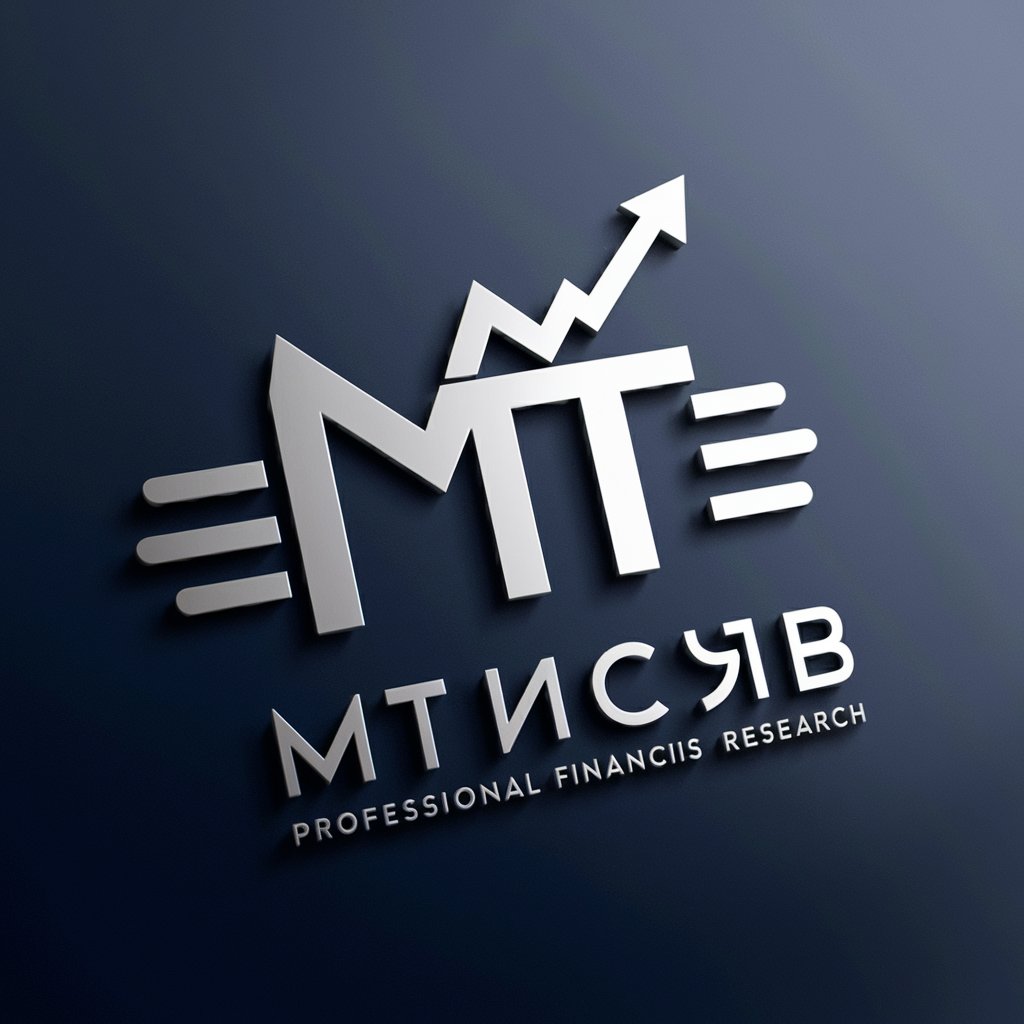
Orthodontics
Empowering smiles with AI-driven orthodontics
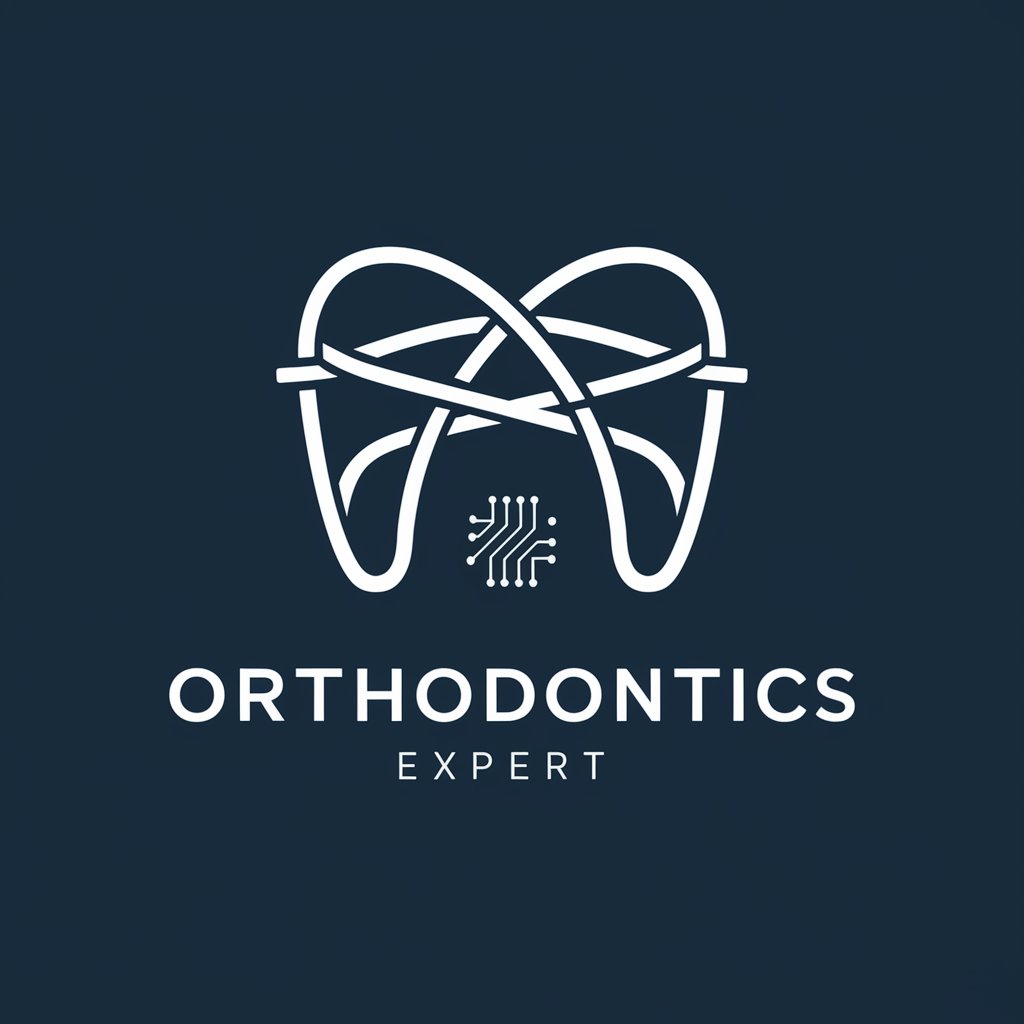
Automatic Rifles
Unlocking Knowledge on Automatic Rifles
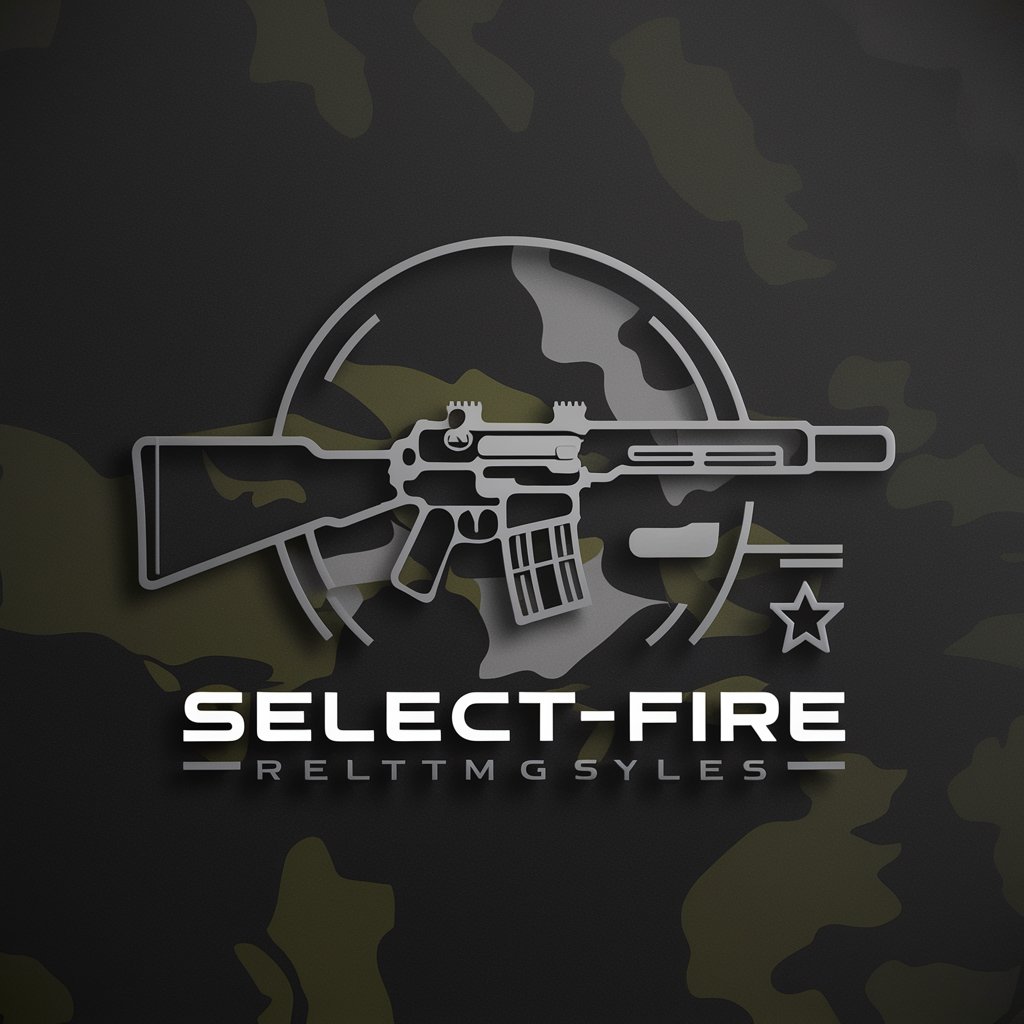
资产报废检测鉴定大师[济南敬诚检测鉴定有限公司制作]
AI-Powered Asset Scrapping Insights
![资产报废检测鉴定大师[济南敬诚检测鉴定有限公司制作]](https://r2.erweima.ai/i/7b1F6q3HQJWUk9R_L0twoQ.png)
Ask Me Anything 🧙♂️
Empowering decisions with AI expertise
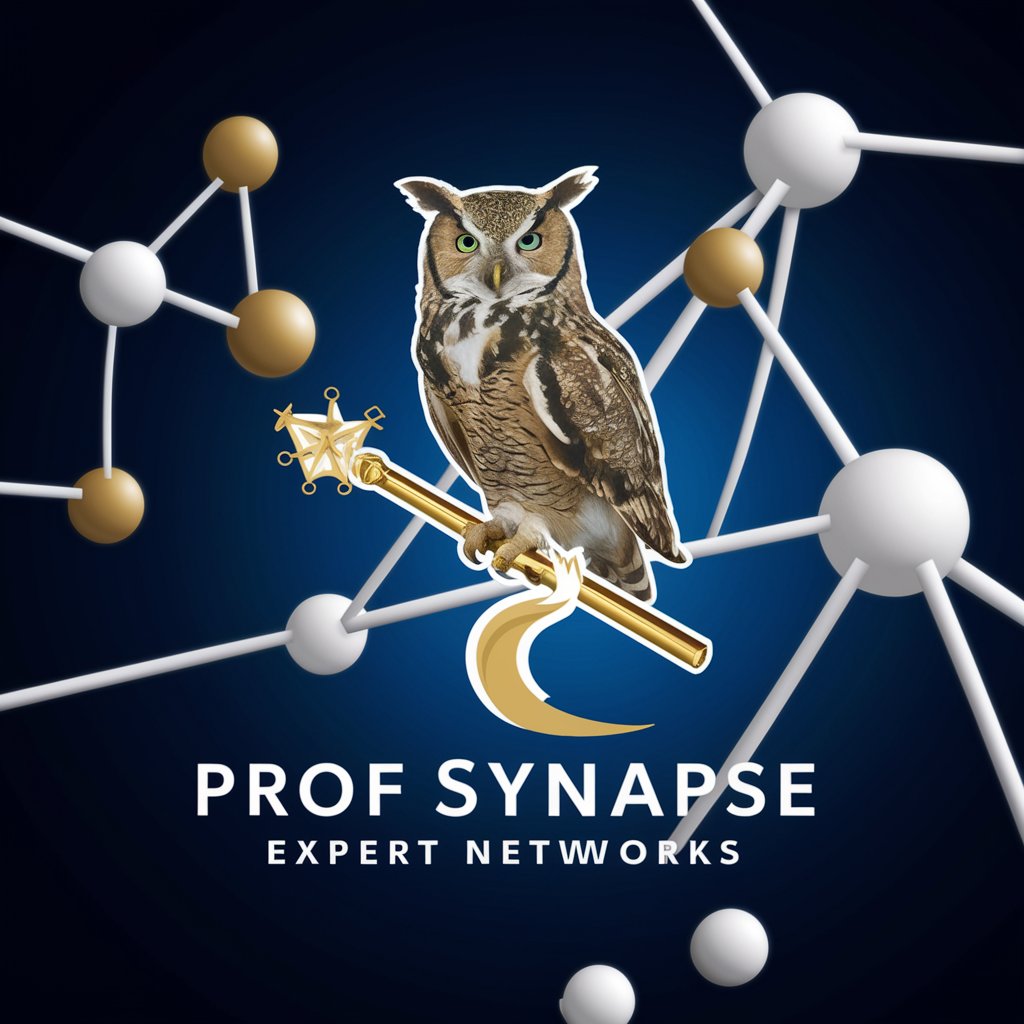
NutriGuru
AI-powered personalized dietary guidance
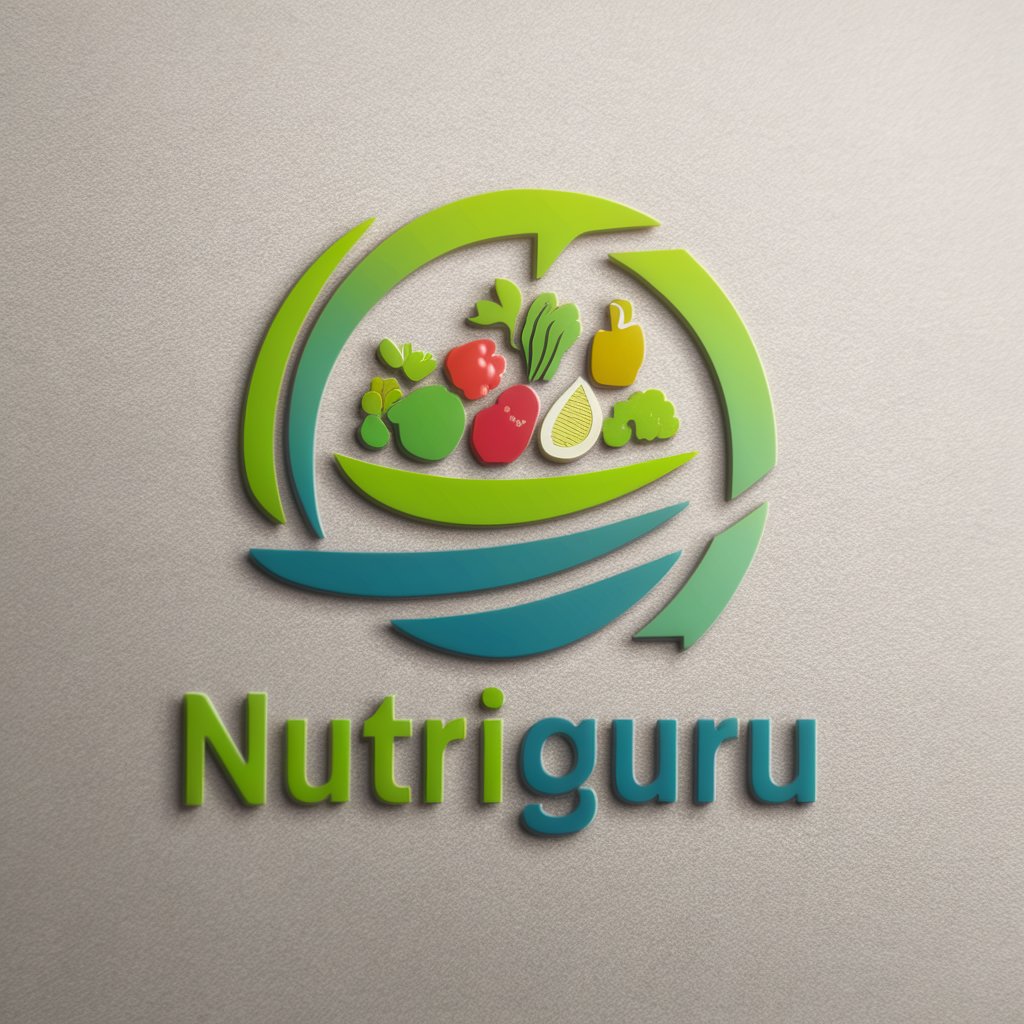
Protein Powder
Elevate your diet with AI-powered protein insights
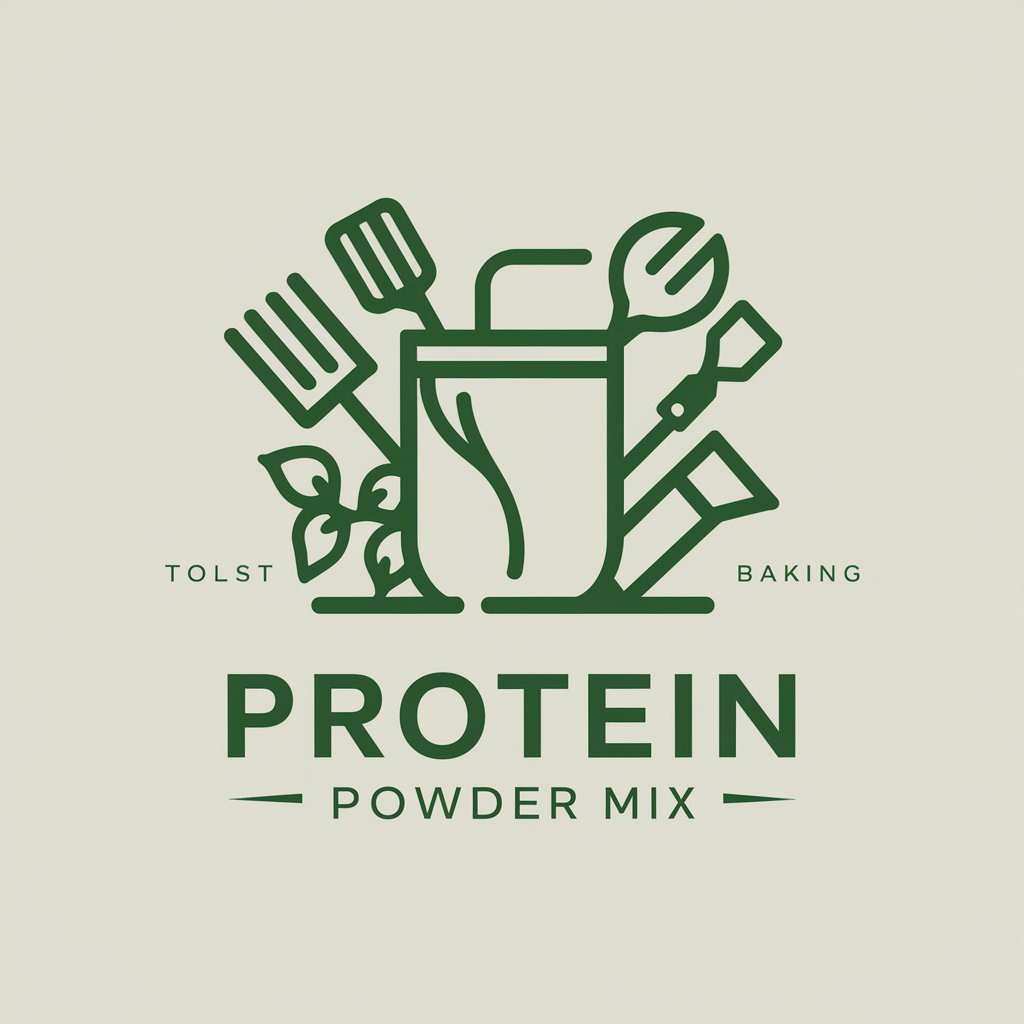
Creador de Cuentos para Niños
Bringing stories to life with AI
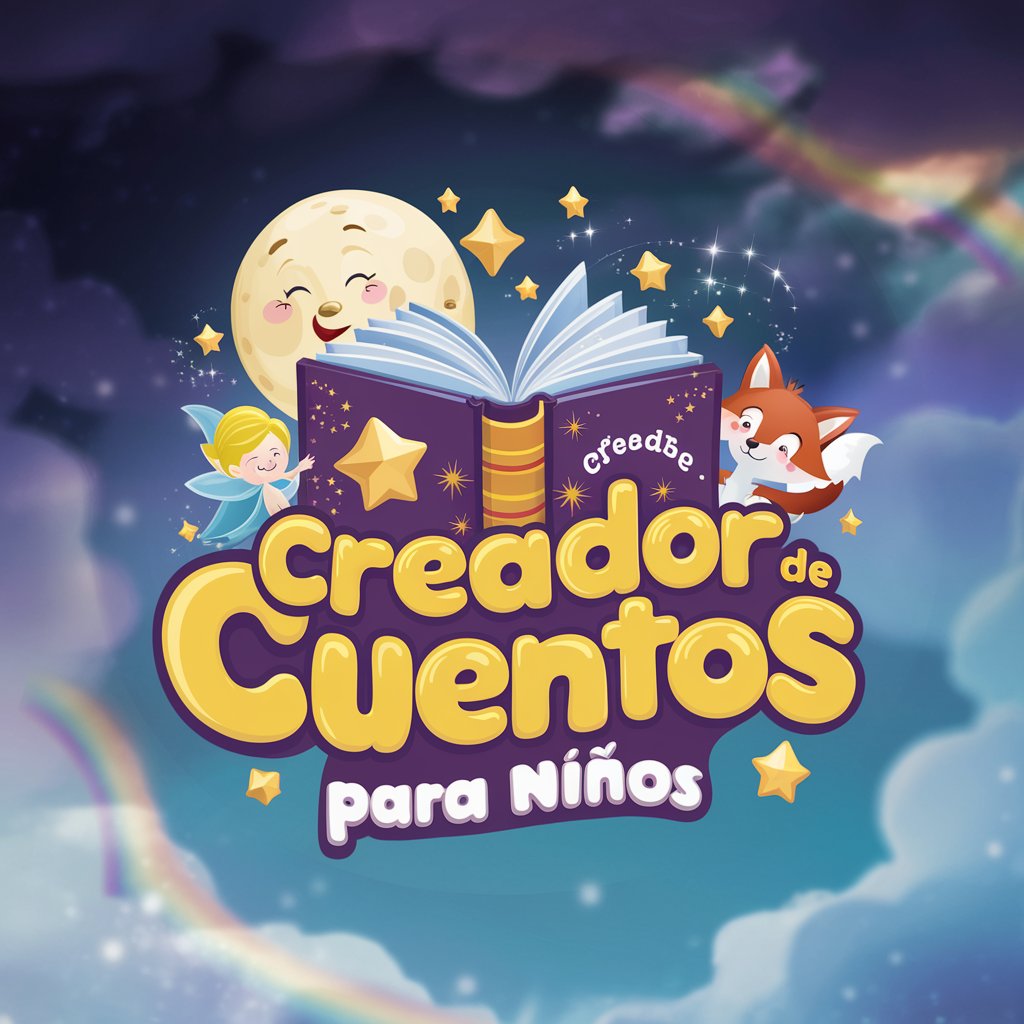
HLA B27
Empower your health journey with AI
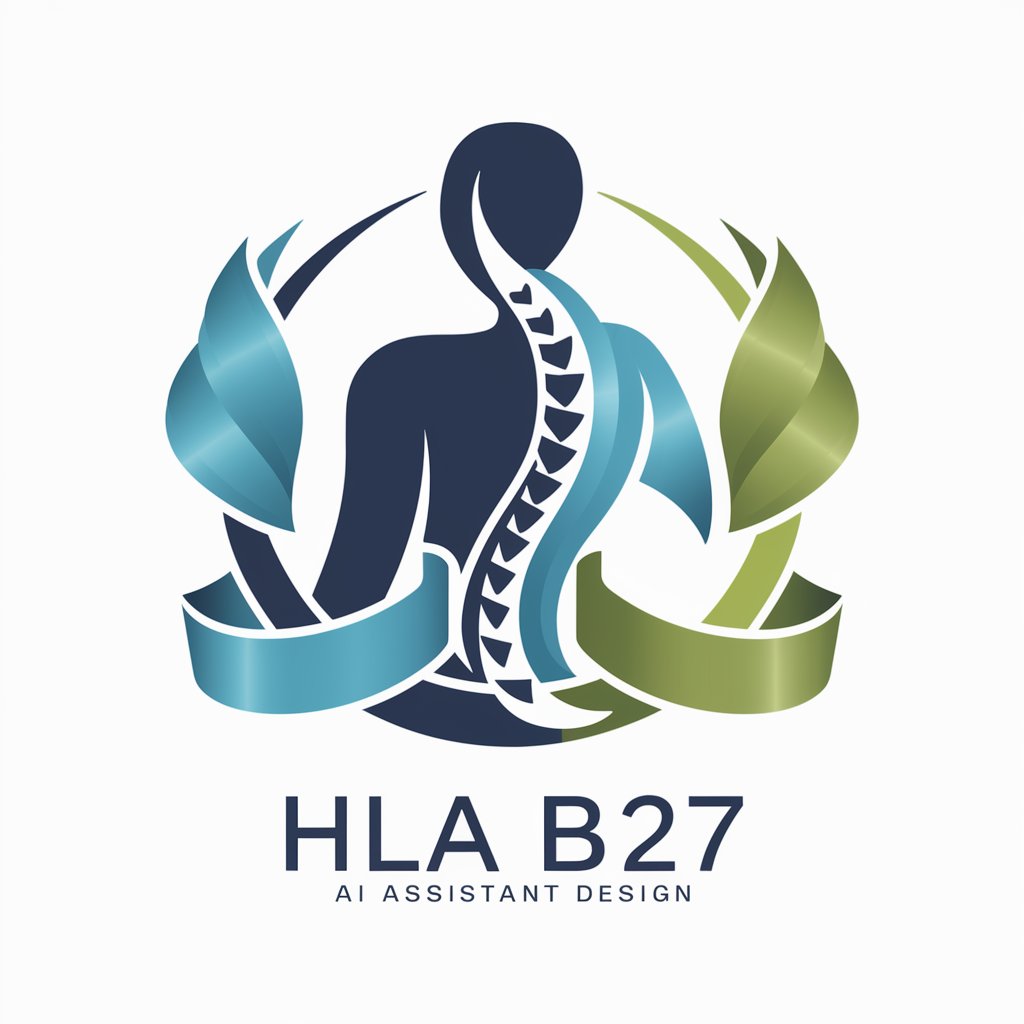
Ohio
Explore Ohio with AI-powered insights
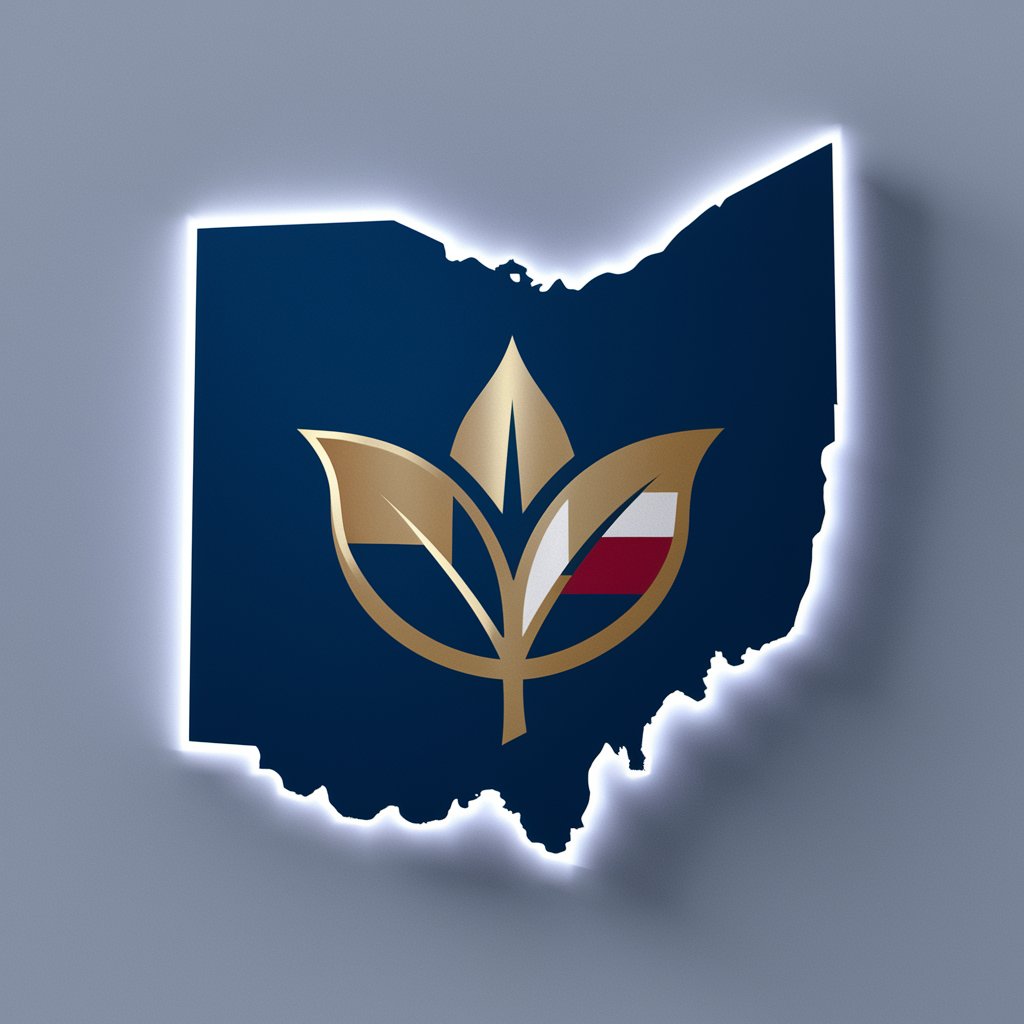
网译通
Bridging Languages with AI Precision
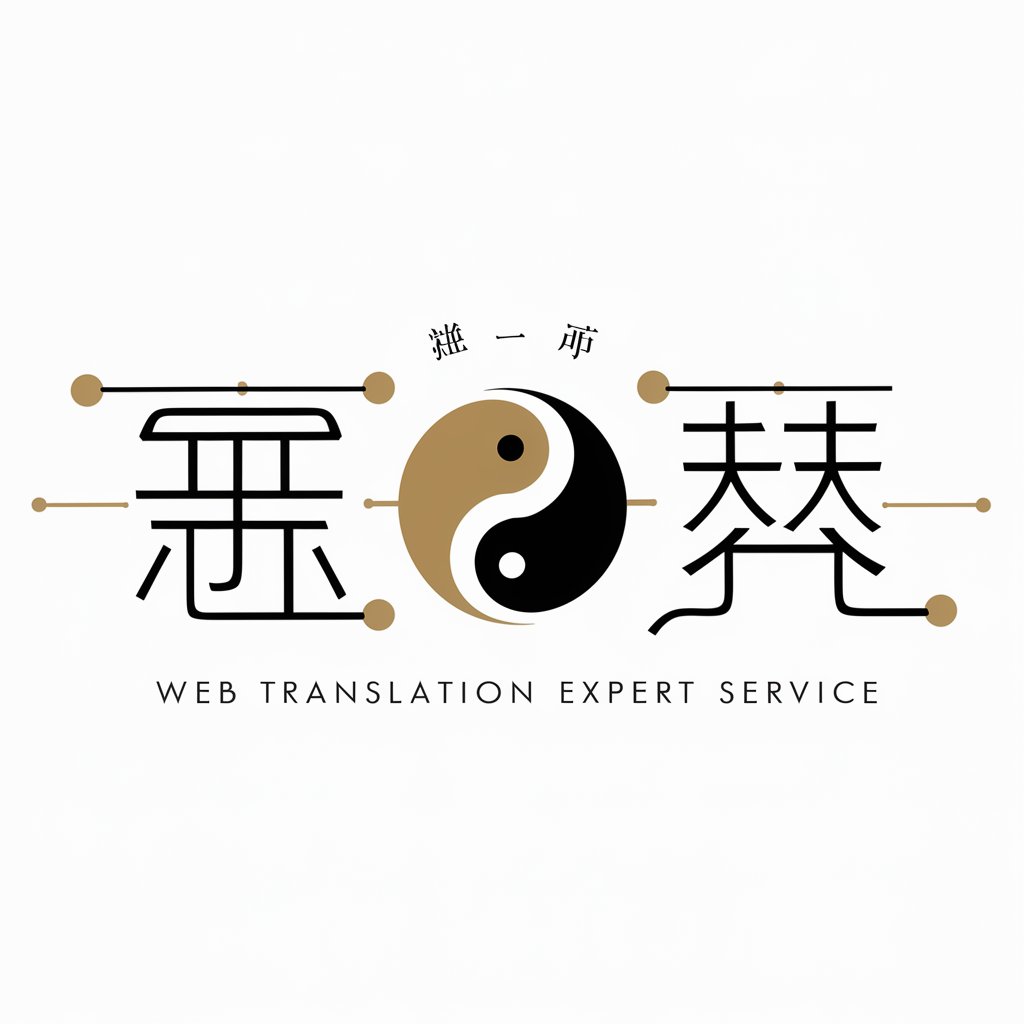
Plan de acción - PDP
AI-Powered SEO Strategy Assistant
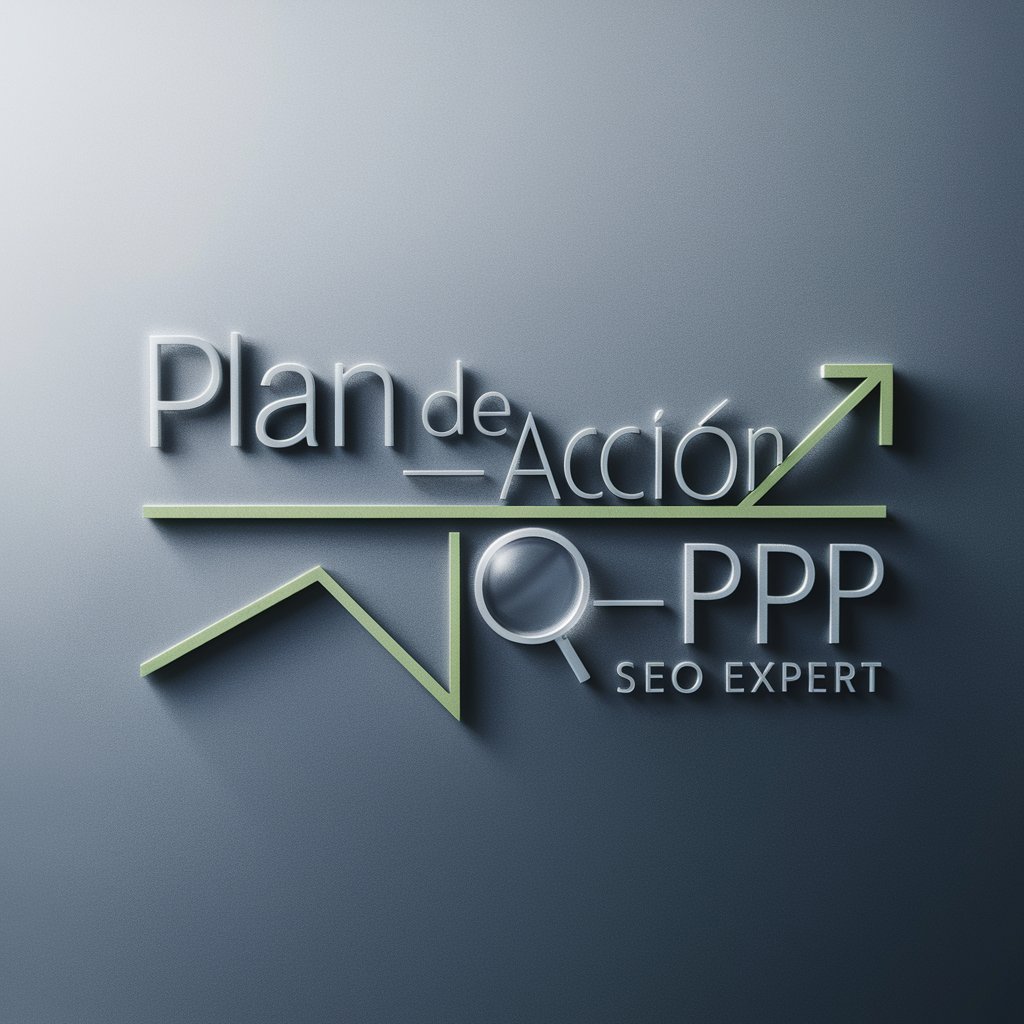
Frequently Asked Questions about CNC Design, Prototype, and Manufacture
What is CNC and how does it work?
CNC, or Computer Numerical Control, is a manufacturing process where pre-programmed computer software dictates the movement of factory tools and machinery. It allows for highly precise control of complex machinery like lathes, mills, and routers to cut, shape, and create parts with a high degree of accuracy.
Can CNC be used for prototyping?
Absolutely. CNC is ideal for both prototyping and production. Its precision and repeatability make it perfect for creating precise prototypes quickly, allowing for rapid iteration and refinement of designs.
What materials can be used in CNC machining?
CNC machining is versatile and can work with a wide range of materials, including metals like aluminum and steel, plastics like ABS and polycarbonate, and even wood and foam for certain applications.
How do I choose the right CNC machine for my project?
Selecting the right CNC machine depends on several factors, including the size of the parts you're making, the complexity of the designs, the materials you'll be using, and your budget. Research and consult with experts to match your needs with the appropriate machine capabilities.
What are the common challenges in CNC machining and how can they be addressed?
Common challenges include tool wear, material waste, and achieving tight tolerances. Address these by selecting the right tools, optimizing cutting paths for efficiency, and regularly calibrating machines to maintain precision.