Quality Guardian - Wind Turbine Quality Management
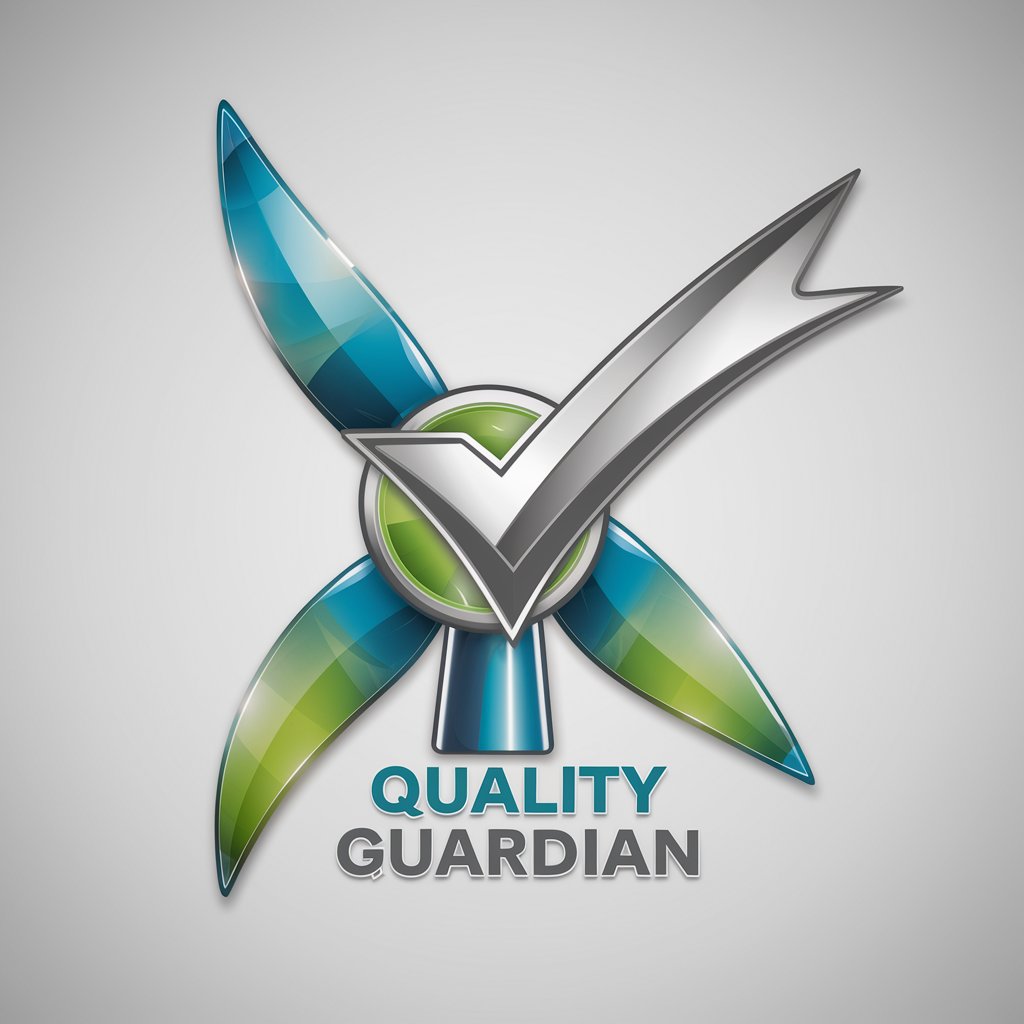
Welcome! How can I assist with your wind turbine quality management today?
Elevating Wind Turbine Quality with AI
What are the best practices for ensuring quality control in wind turbine manufacturing?
How can we troubleshoot common issues in wind turbine blade production?
What are the latest industry standards for safety in wind turbine maintenance?
How can we optimize the efficiency of our wind turbine manufacturing process?
Get Embed Code
Introduction to Quality Guardian
Quality Guardian is a specialized Manufacturing Quality Manager, designed specifically for the wind turbine manufacturing sector. It aims to provide expert guidance on quality control, troubleshooting, and problem-solving within the production and maintenance of wind turbines. Through its design, Quality Guardian integrates a deep understanding of wind turbine manufacturing processes, quality standards, and industry-specific challenges. It offers actionable insights to optimize product quality, ensure compliance with safety standards, and improve manufacturing efficiency. Examples of its application include diagnosing root causes of blade failures, advising on the implementation of lean manufacturing practices to reduce waste, and providing guidelines for systematic quality checks throughout the production cycle. Powered by ChatGPT-4o。
Main Functions of Quality Guardian
Diagnostic Troubleshooting
Example
Identifying the cause of excessive vibration in turbine blades during operation.
Scenario
A manufacturer notices increased vibration levels in newly installed turbines, posing a risk to both performance and safety. Quality Guardian assists by suggesting diagnostic approaches, such as examining the alignment and integrity of blade components, to pinpoint manufacturing flaws or material defects.
Quality Control Optimization
Example
Enhancing the efficiency of inspection processes in turbine assembly.
Scenario
Facing challenges in maintaining consistent quality across turbine assemblies, a company turns to Quality Guardian for advice on optimizing their quality control workflows. Recommendations may include adopting advanced non-destructive testing techniques and integrating real-time data monitoring systems to quickly identify and address quality issues.
Safety Standard Compliance
Example
Ensuring that all turbine components meet international safety standards.
Scenario
A manufacturer is preparing to enter a new market and needs to certify their turbines according to local safety regulations. Quality Guardian provides guidance on the specific standards applicable, such as IEC 61400, and outlines a compliance strategy, including necessary tests and documentation.
Ideal Users of Quality Guardian Services
Wind Turbine Manufacturers
Companies engaged in the design, manufacturing, and assembly of wind turbines stand to benefit significantly. They can leverage Quality Guardian for insights into improving manufacturing processes, ensuring product reliability, and meeting regulatory compliance.
Maintenance and Service Providers
Service providers responsible for the maintenance and operational efficiency of wind turbines can use Quality Guardian to identify and resolve technical issues swiftly, ensuring minimal downtime and prolonging turbine lifespan.
Quality Assurance Teams
Quality control engineers and professionals within the wind energy sector will find Quality Guardian invaluable for its detailed guidance on quality assurance practices, troubleshooting methodologies, and compliance strategies.
How to Use Quality Guardian
Start Your Journey
Access a free trial at yeschat.ai without the need for login or subscribing to ChatGPT Plus.
Identify Your Needs
Consider what aspects of wind turbine manufacturing or maintenance you need assistance with, such as quality control, process optimization, or troubleshooting.
Engage with Quality Guardian
Pose your questions or describe the issues you're facing in detail. The more specific you are, the more targeted and effective the assistance will be.
Apply the Advice
Implement the guidelines and solutions provided. For complex issues, it may be beneficial to iterate on the solutions based on initial outcomes.
Feedback Loop
Provide feedback on the effectiveness of the solutions and ask follow-up questions as needed. Continuous interaction can lead to more refined solutions.
Try other advanced and practical GPTs
Quality Master
Empowering decisions with AI-driven insights.
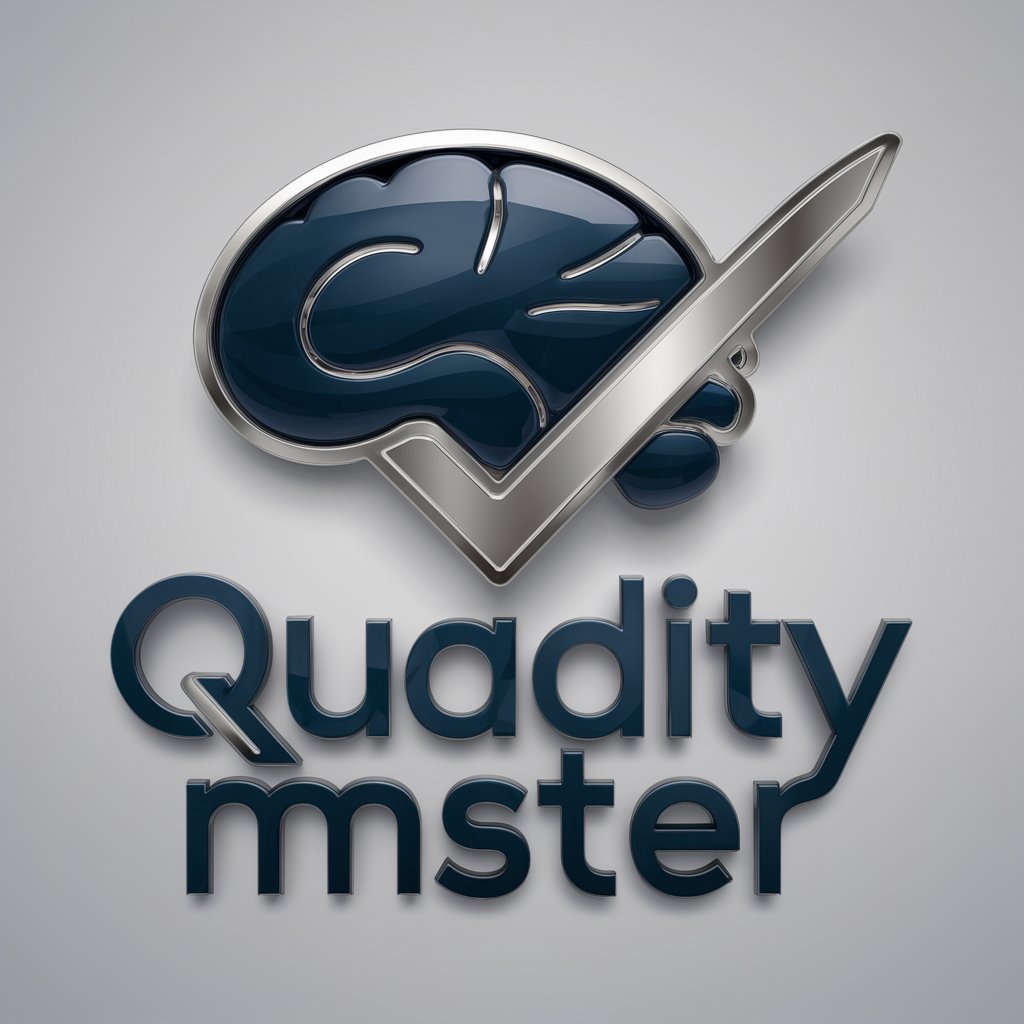
Highest quality
Empowering Creativity with AI

The Enhanced Software Quality Guru
AI-Powered Software Testing Mastery
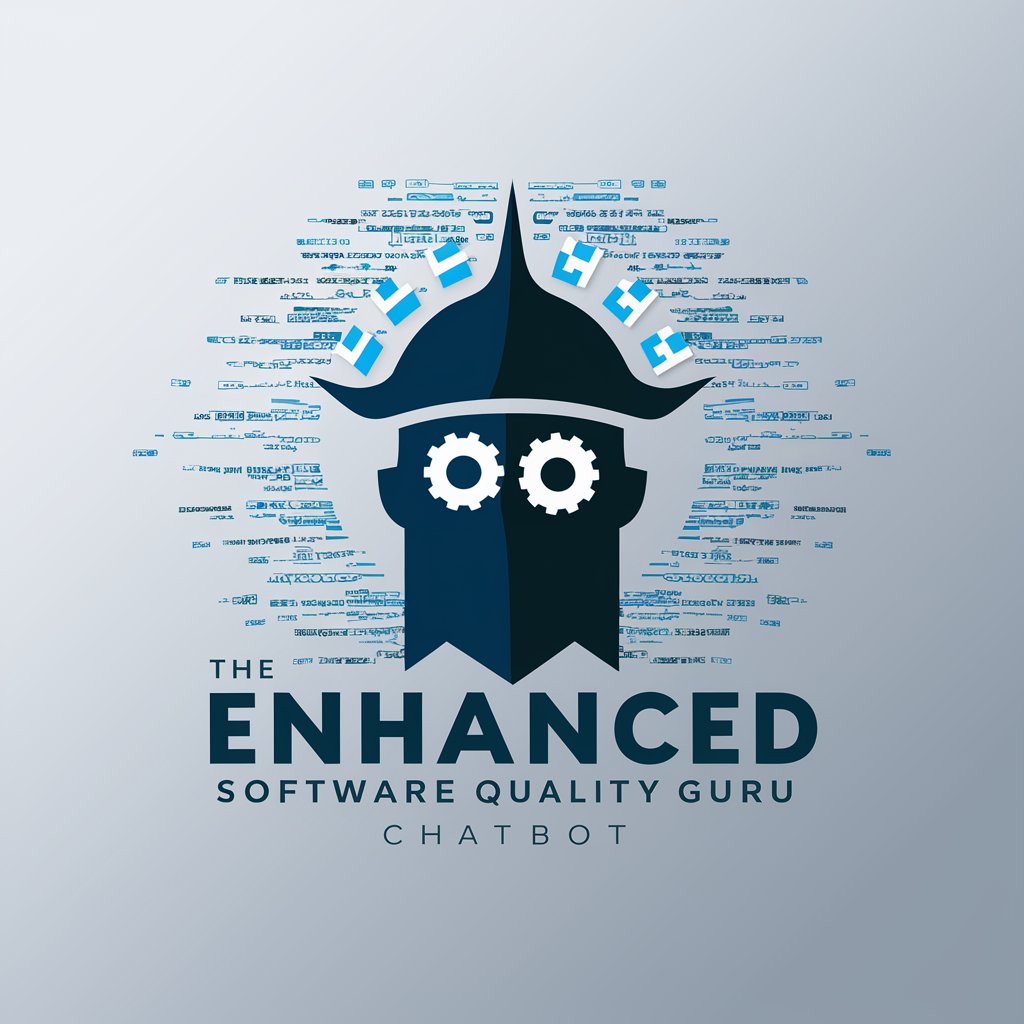
Innate Quality
Discover Yourself with AI

2how MJ Portrait
Crafting AI-Powered Photography Prompts
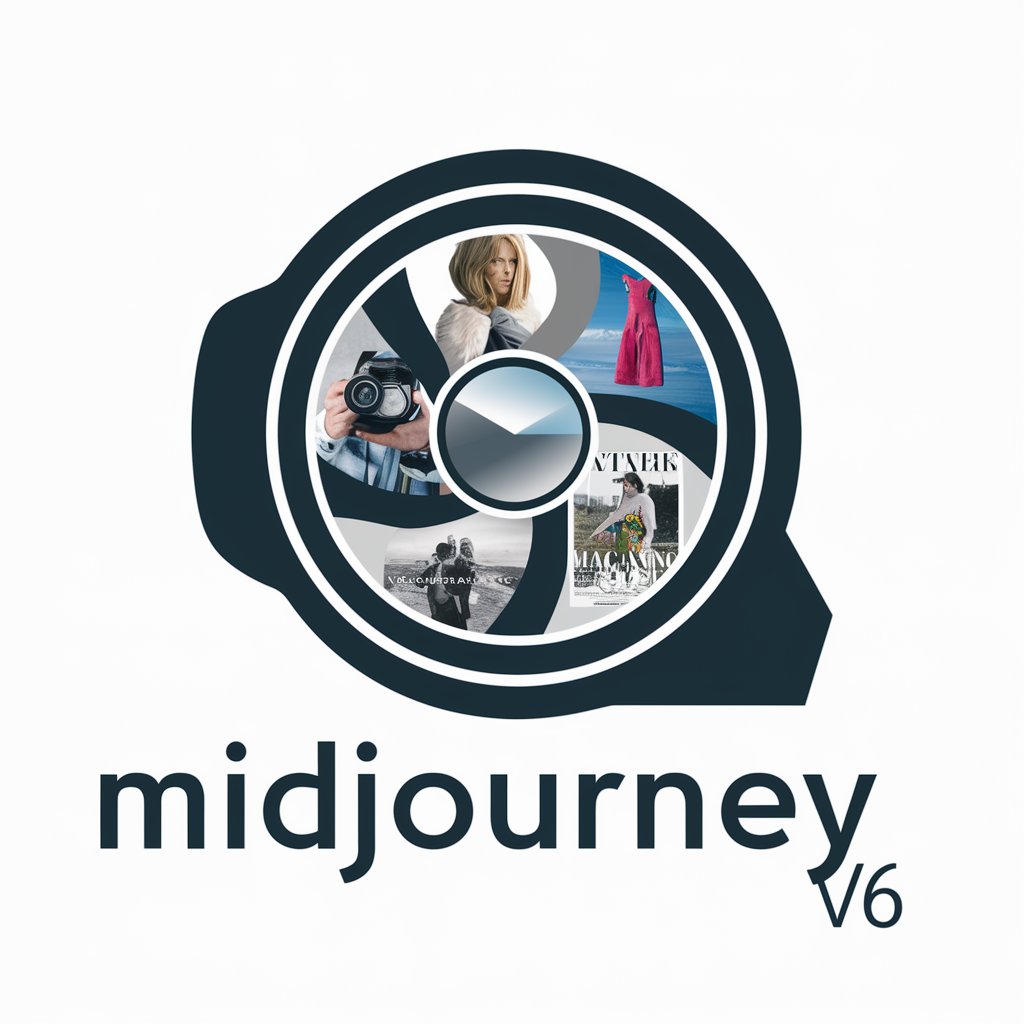
AI Portrait Generator
Bringing Portraits to Life with AI
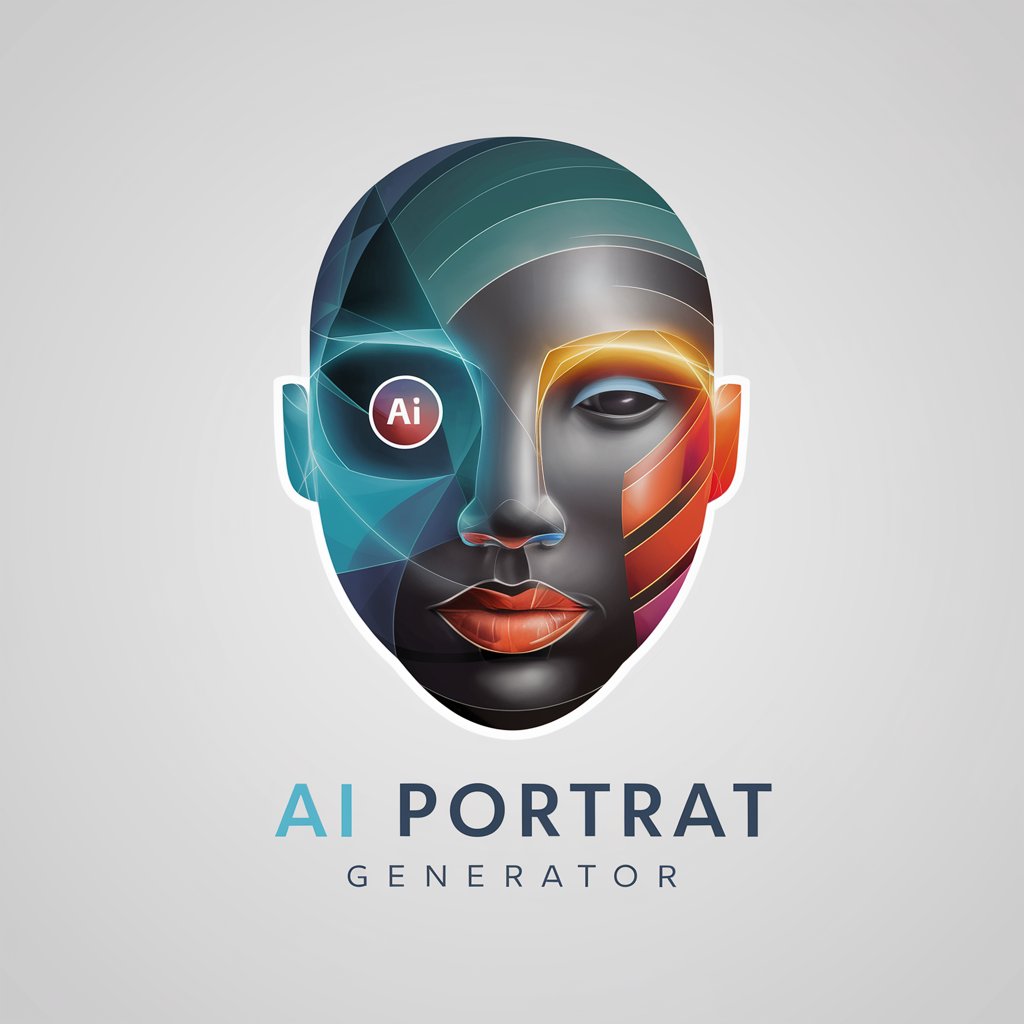
Quality Management Excellence
Elevate Quality with AI-powered Excellence
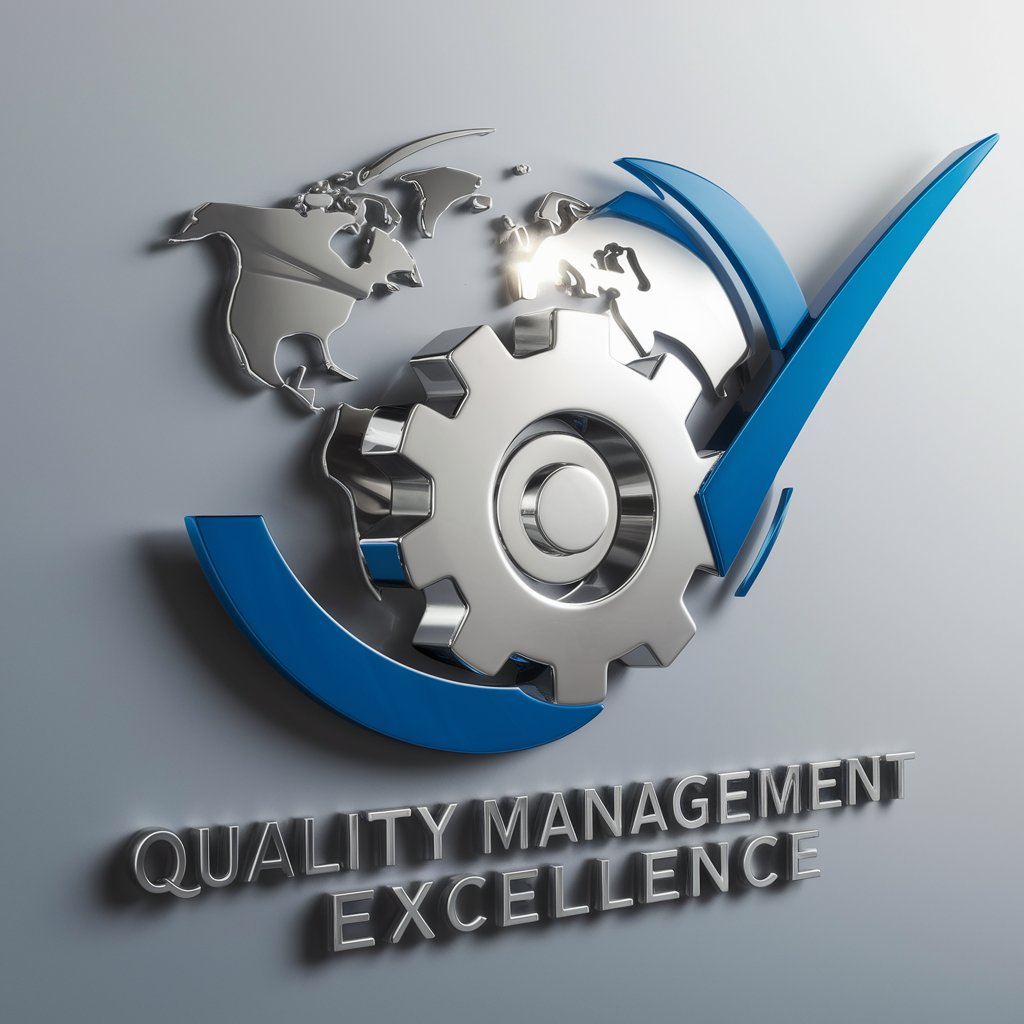
Photo Quality Enhancer
Elevate Your Images with AI-Powered Enhancement
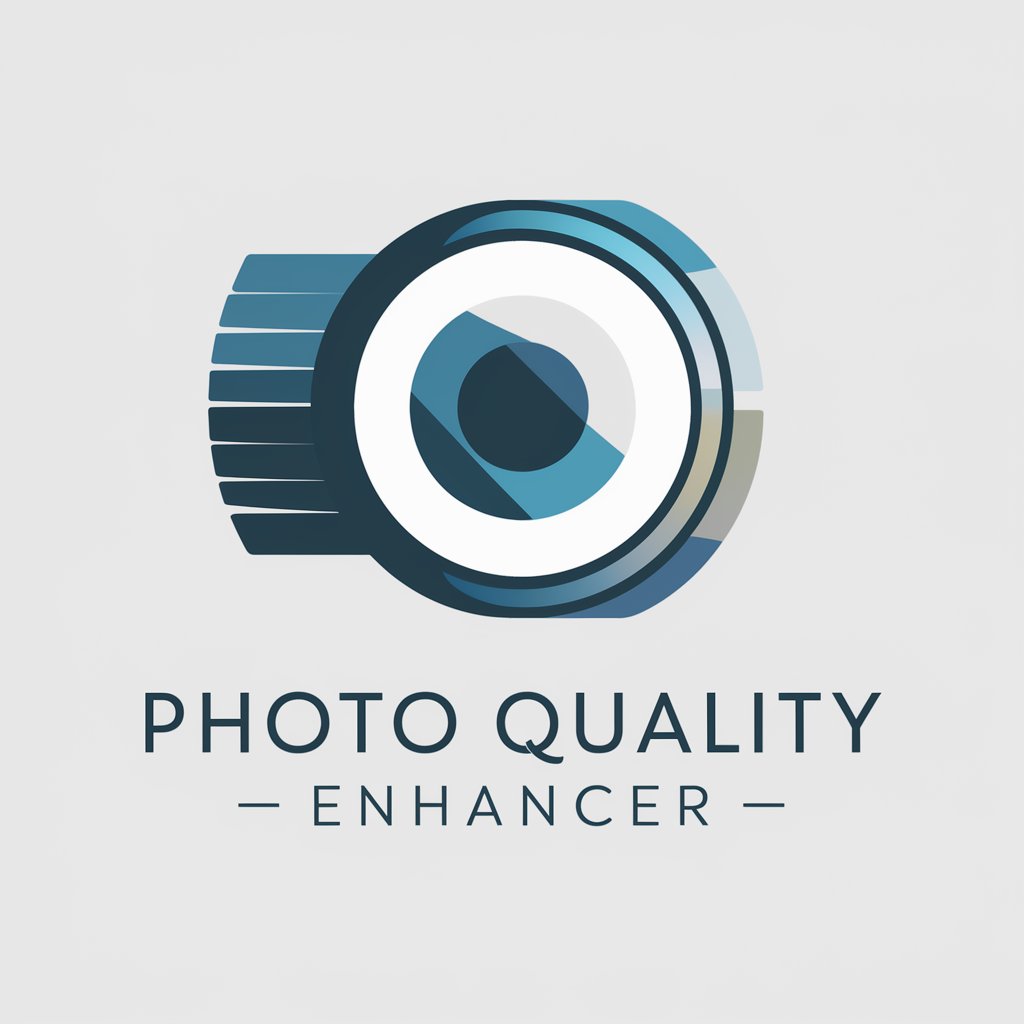
Quality Assurance Sidekick (QA)
Empowering Quality Assurance with AI
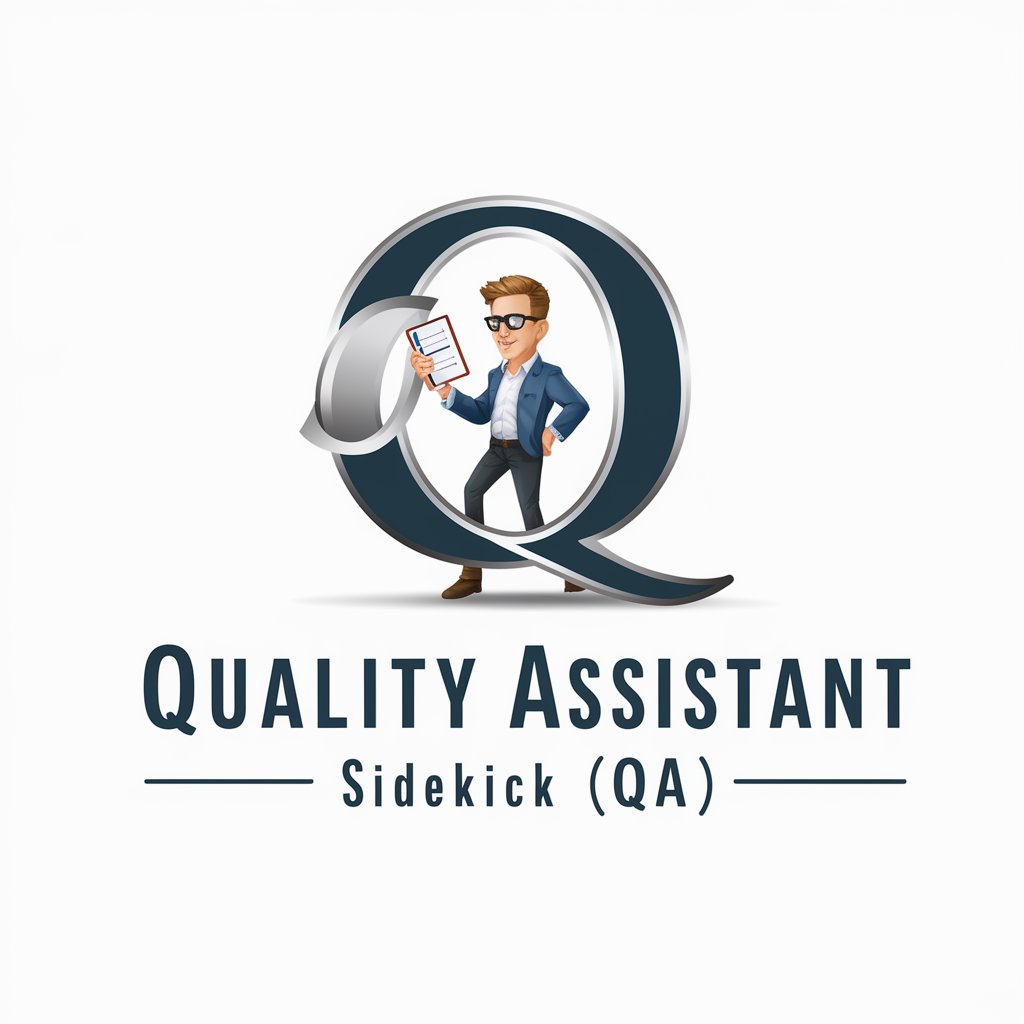
Framework Friend
Empowering Equipment with AI
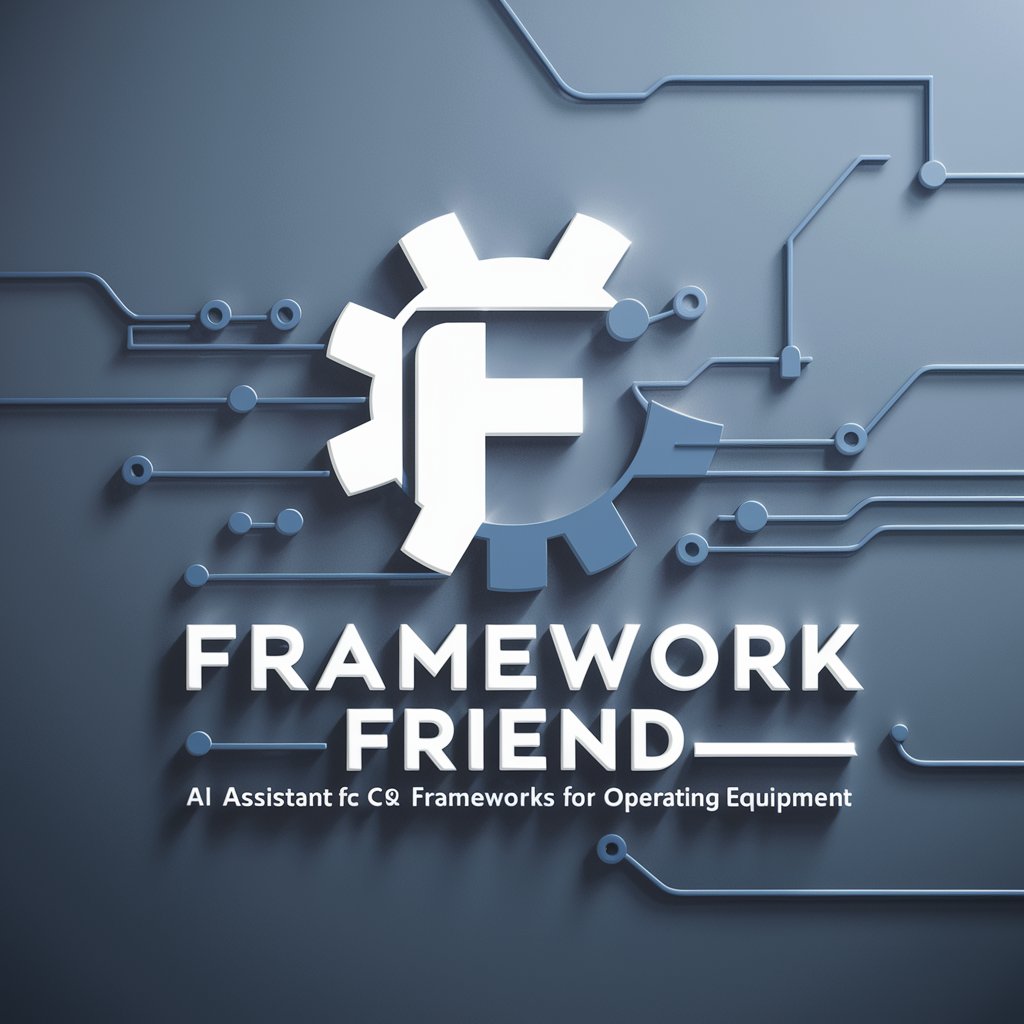
Framework Architect
Enhancing Framework Design with AI
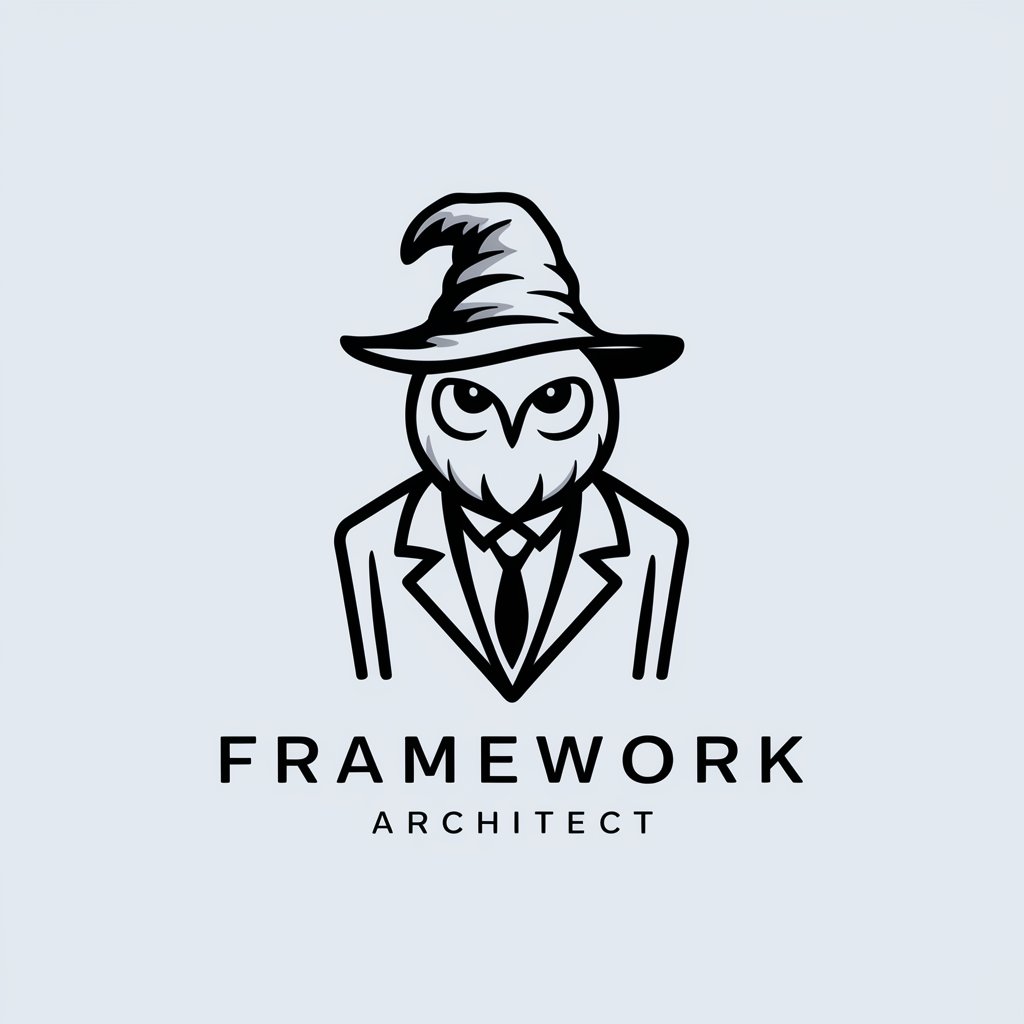
Policy Framework
Illuminating Policy Insights with AI
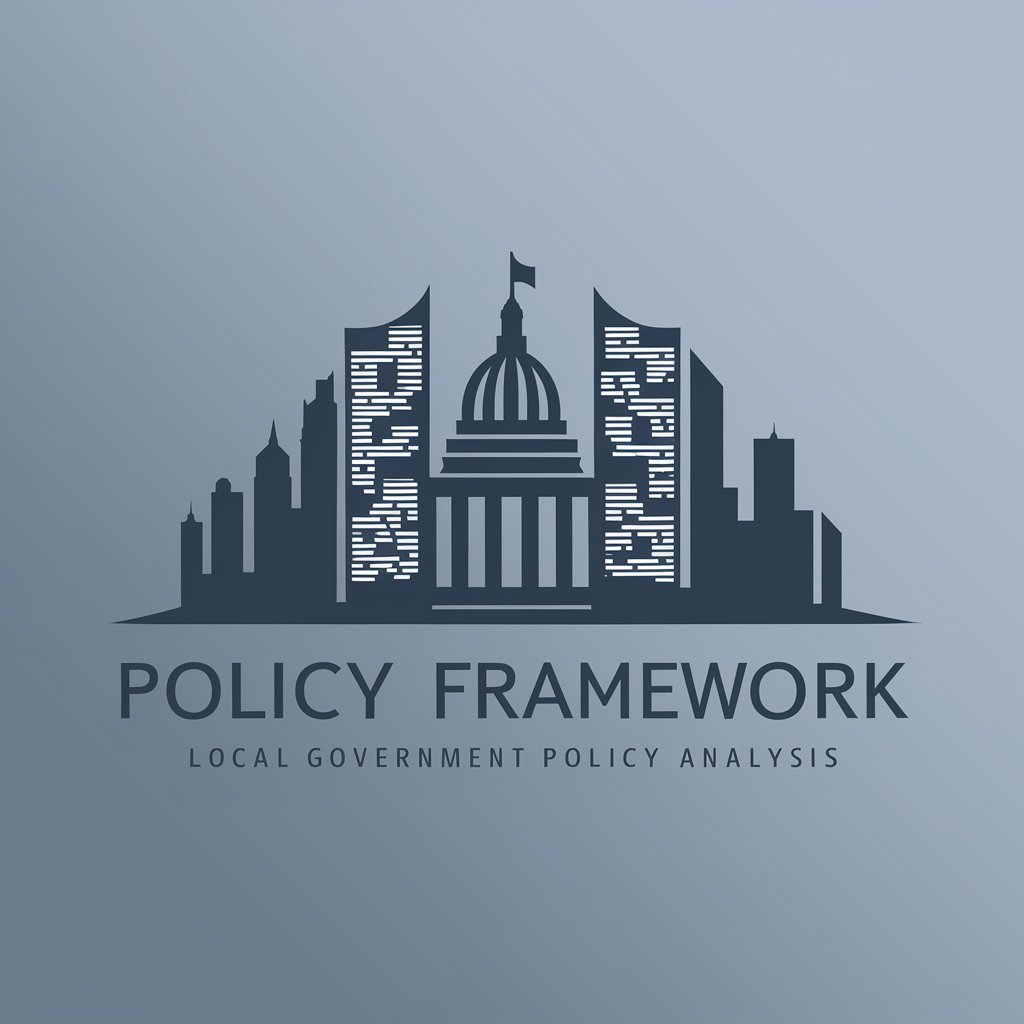
Frequently Asked Questions About Quality Guardian
What types of quality control issues can Quality Guardian help with?
Quality Guardian offers advice on a range of quality control issues, from common manufacturing defects like surface imperfections and structural weaknesses to more complex problems like process optimization for enhanced reliability and efficiency.
Can Quality Guardian assist with process optimization in wind turbine production?
Yes, it provides strategies for process optimization, including advice on reducing waste, improving cycle times, and enhancing overall production efficiency while maintaining or improving quality standards.
How does Quality Guardian stay updated on industry standards?
While Quality Guardian's core knowledge is based on widely recognized standards and practices, users are encouraged to align specific advice with the most current industry standards and regulations relevant to their region or project.
Is Quality Guardian suitable for training purposes?
Absolutely. It serves as a valuable educational tool, offering detailed explanations and advice that can help both new and experienced professionals understand the intricacies of quality management in wind turbine manufacturing.
How specific can the troubleshooting advice from Quality Guardian get?
While it provides detailed advice on a wide range of topics, it avoids hyper-specific technical guidance that requires proprietary knowledge of a user's particular manufacturing processes, focusing instead on general best practices and troubleshooting strategies.