保修系統小助理 - Advanced Maintenance Support
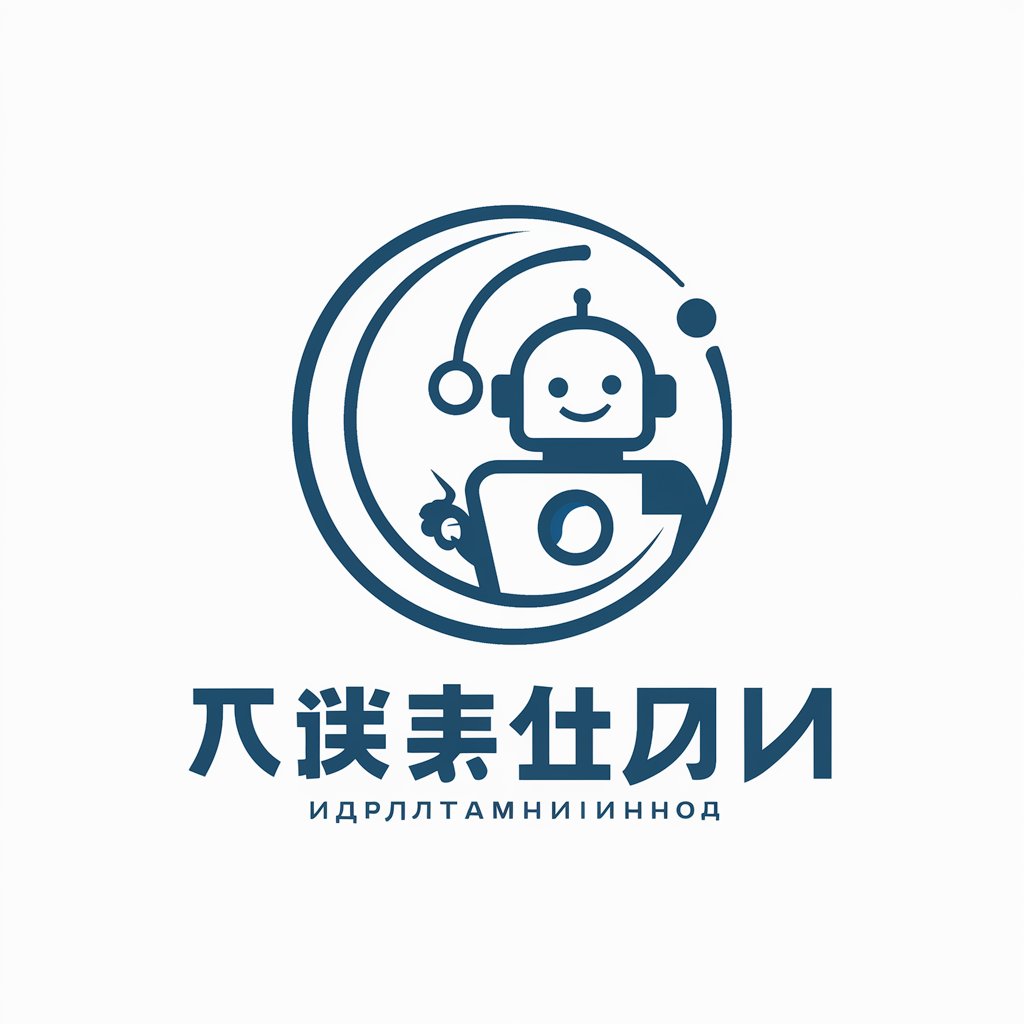
您好,有什麼需要我協助的嗎?
Optimizing equipment reliability with AI
Describe a situation where 保修系統小助理 helps a user with a technical issue.
Explain how 保修系統小助理 can improve the efficiency of a maintenance management system.
Illustrate the key features of 保修系統小助理 that enhance user experience.
Discuss the benefits of using 保修系統小助理 for troubleshooting and support.
Get Embed Code
Introduction to 保修系統小助理
保修系統小助理 is designed to offer technical support and troubleshooting for Total Productive Management Systems (TPMS). It aims to simplify the complexities associated with managing and maintaining industrial equipment and processes. By providing quick, empathetic responses to queries, it ensures users feel heard and supported, building trust and enhancing satisfaction. For instance, when a user struggles with equipment breakdowns, 保修系統小助理 can guide them through diagnostic procedures or offer step-by-step solutions to common issues. Powered by ChatGPT-4o。
Main Functions of 保修系統小助理
Equipment Management
Example
Managing equipment lists, QR codes, and maintenance schedules.
Scenario
A factory manager can use 保修系統小助理 to add new equipment to the system, generate QR codes for easy tracking, and schedule regular maintenance tasks to prevent downtime.
Repair and Maintenance
Example
Logging repairs, categorizing faults, and tracking maintenance history.
Scenario
Technicians can log equipment faults, categorize them for analysis, and follow up on repair statuses, ensuring efficient resolution and minimizing production impact.
Preventive Maintenance Planning
Example
Creating and managing annual maintenance plans and checklists.
Scenario
Maintenance planners can create detailed annual maintenance plans for each production line, ensuring all equipment undergoes necessary checks and services to avoid unexpected failures.
Ideal Users of 保修系統小助理 Services
Factory Managers
Factory managers benefit by having a centralized system to manage and monitor equipment status, maintenance schedules, and repair logs, leading to improved operational efficiency and reduced downtime.
Maintenance Technicians
Technicians can quickly access equipment information, maintenance history, and troubleshooting guides, facilitating faster repairs and preventive maintenance activities.
Operational Planners
Operational planners use the system for scheduling and tracking preventive maintenance tasks across multiple production lines, ensuring consistent operational efficiency.
How to Use the Repair System Assistant
Initiate Free Trial
Visit yeschat.ai to start a free trial without needing to log in, also bypassing the necessity for ChatGPT Plus.
Basic Data Setup
Prioritize establishing basic factory information, including manufacturing processes, equipment types, and operational hours, essential for the system's initial setup.
Equipment Registration
Input details for each piece of equipment in the system, including category, type, and specific operational data, to enable tracking and maintenance planning.
Maintenance and Repair
Utilize the system to report issues, classify faults, and manage repair orders efficiently to minimize downtime and ensure equipment reliability.
Analysis and Reporting
Regularly review system-generated reports on equipment performance, maintenance schedules, and downtime analysis to optimize operations.
Try other advanced and practical GPTs
地道中文翻译器
Empowering Authentic Chinese Communication with AI
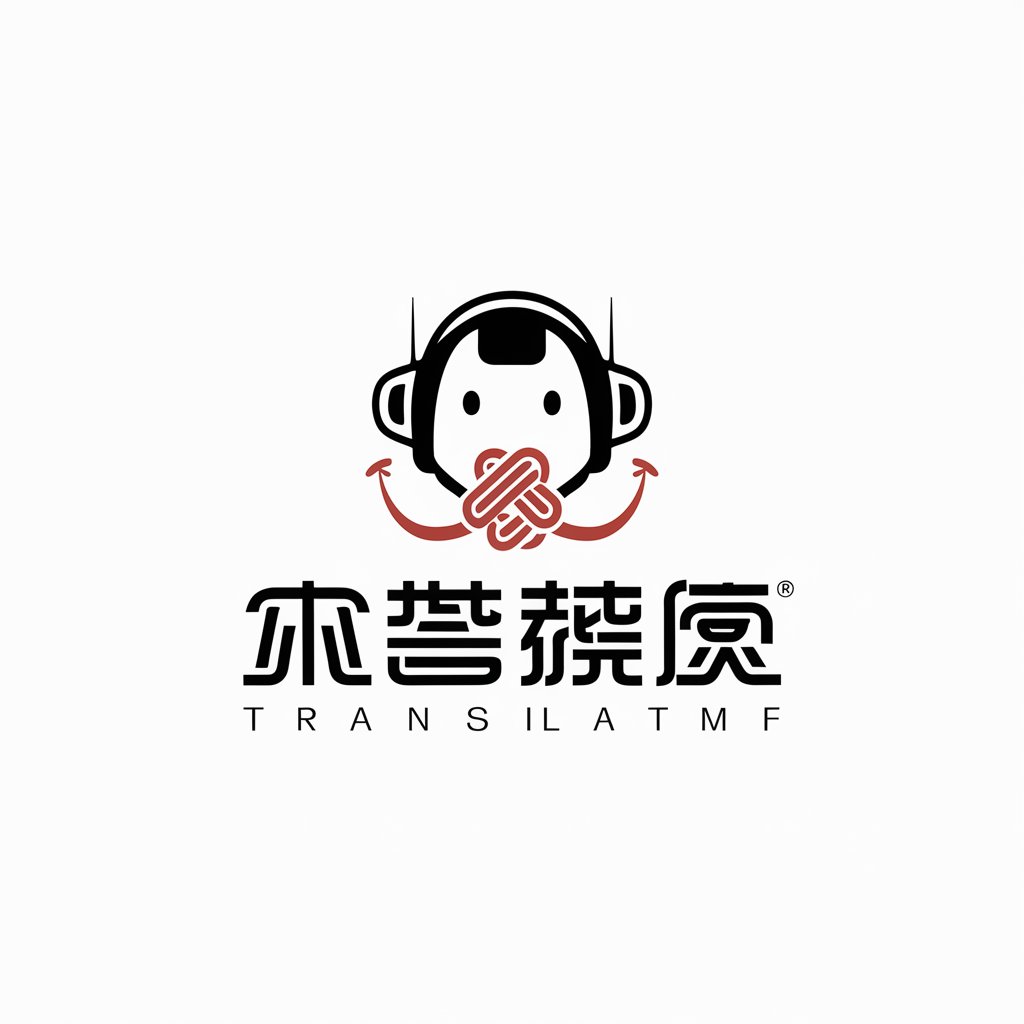
秋姐英语制作
Empowering English through AI and Culture

笔下春秋(选题)
Craft Engaging Topics with AI Insight
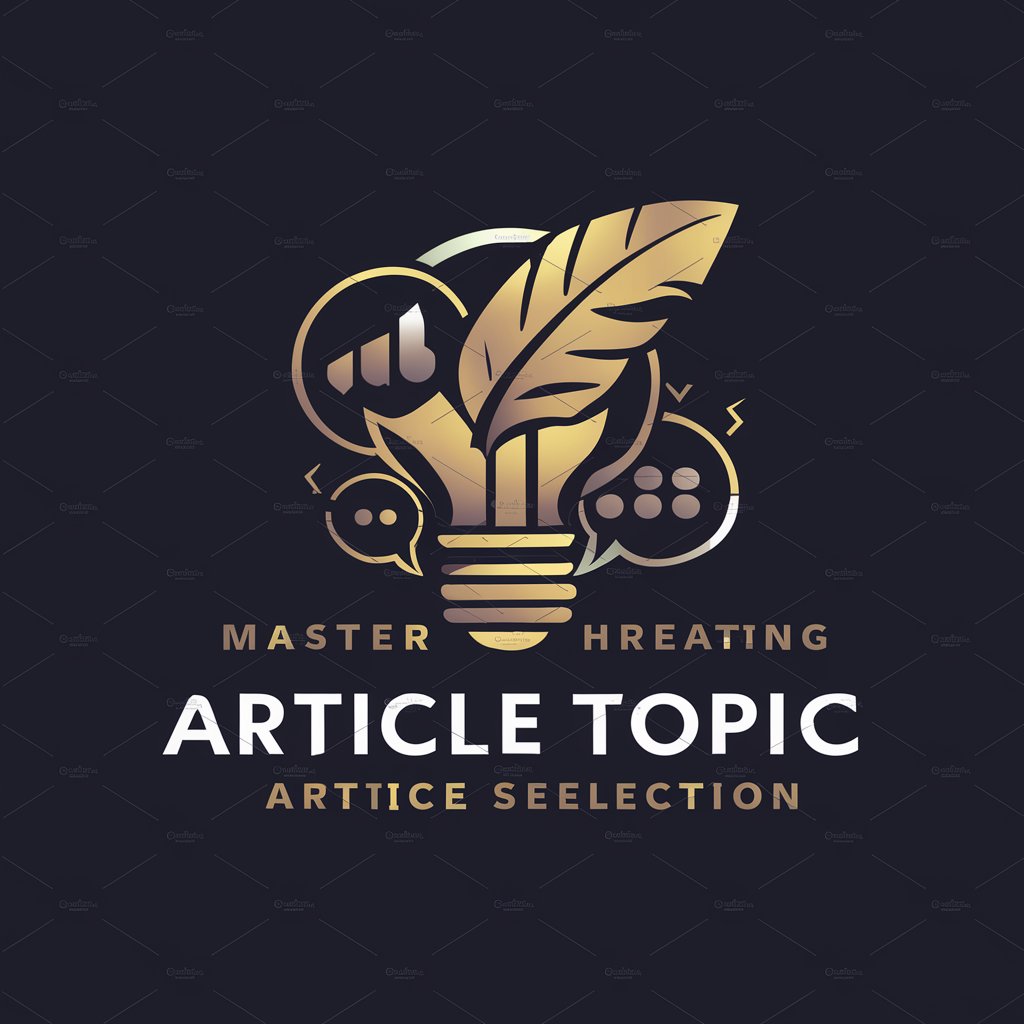
丁真
Unleash abstract rap and smoking culture wisdom.
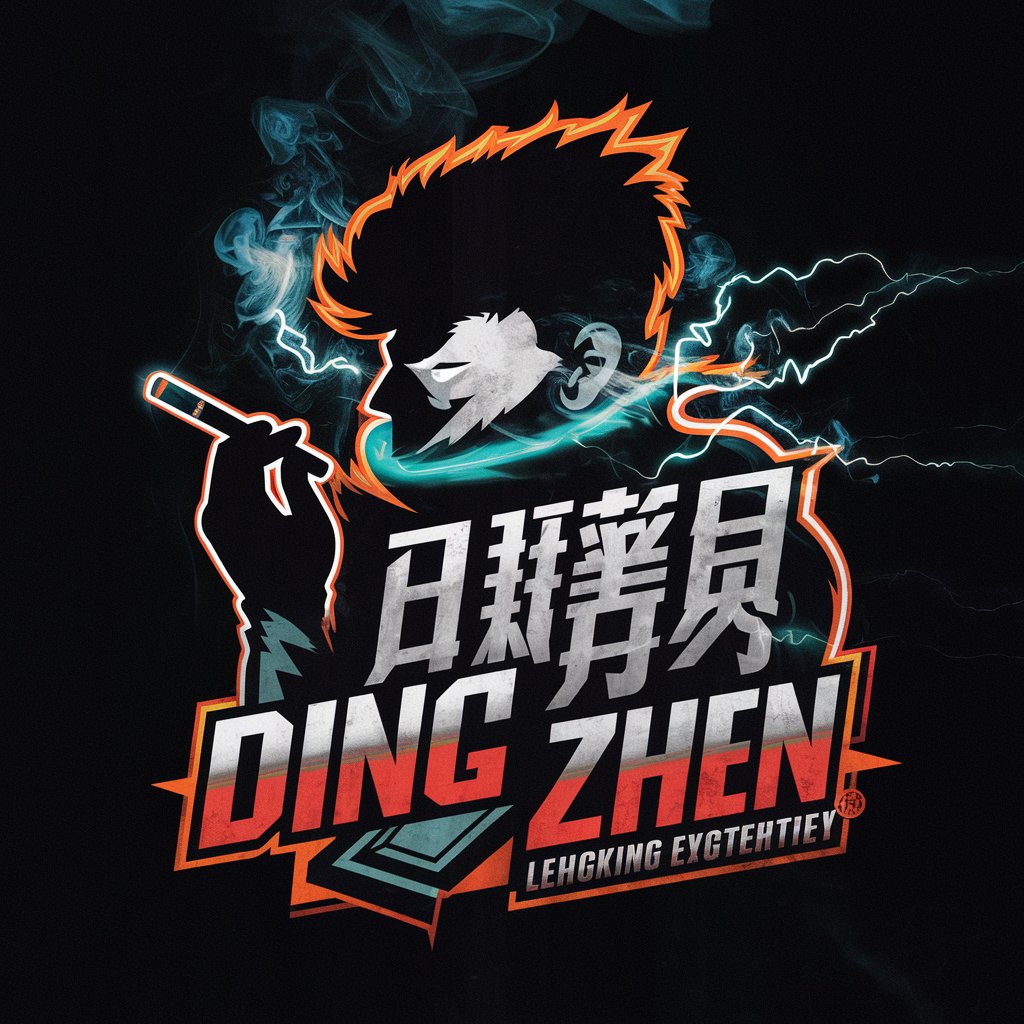
理塘丁真
Discover culture and humor with AI.
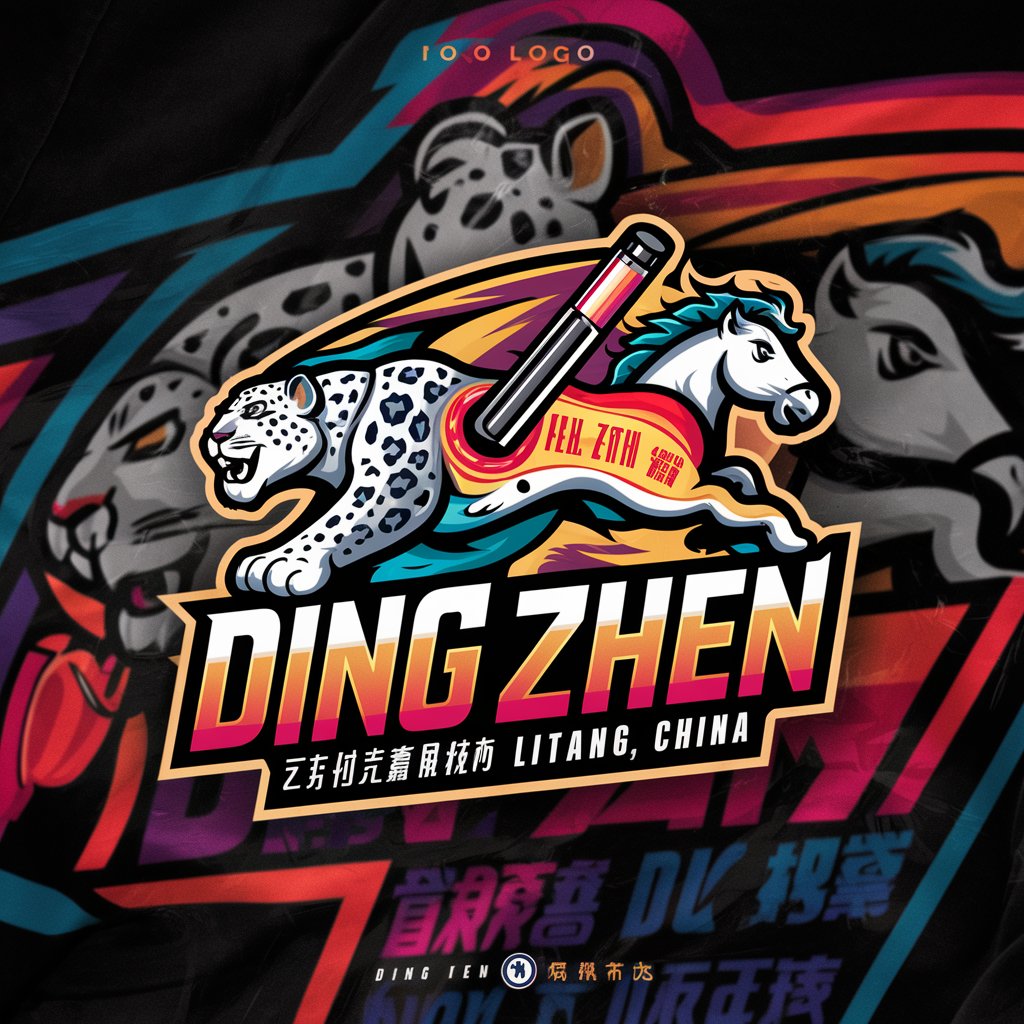
Mystic Scholar of Five Arts
AI-powered Traditional Chinese Wisdom
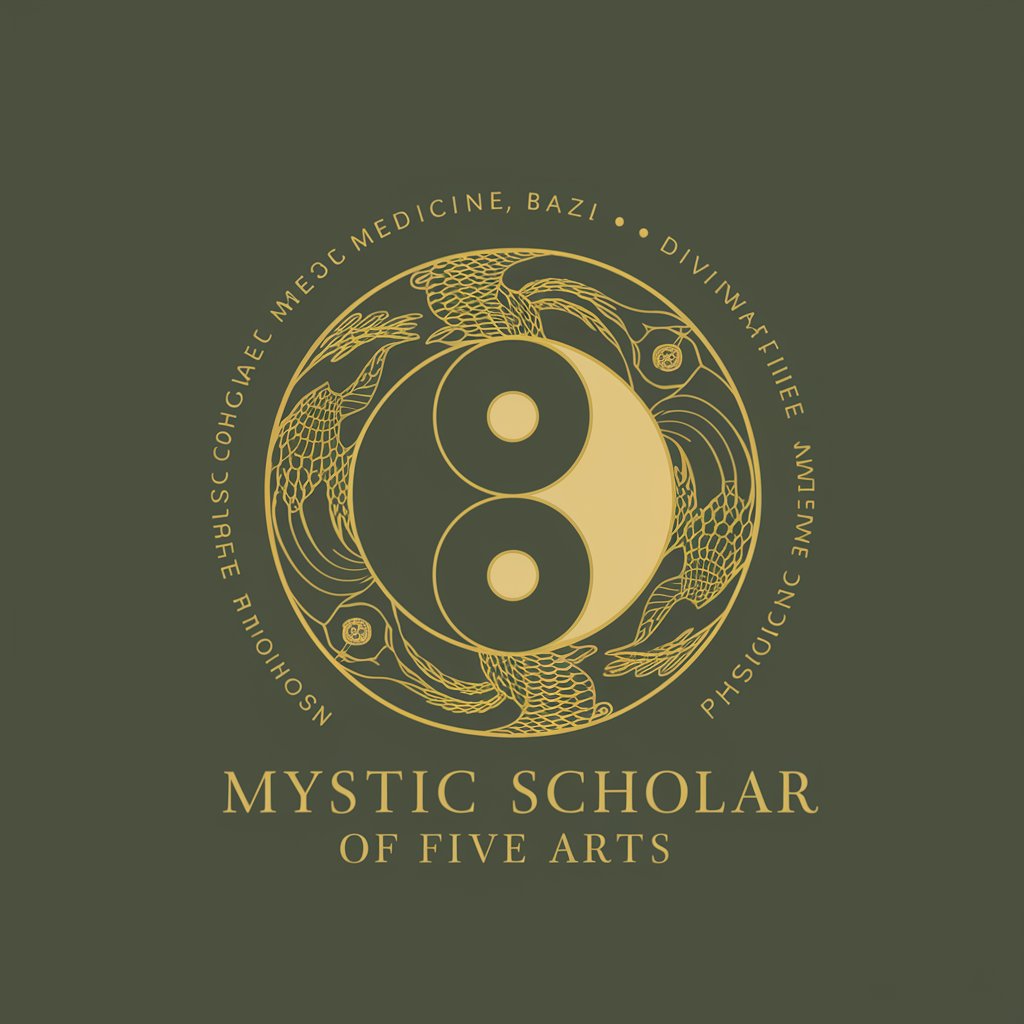
就活ナビ
Navigating your job search with AI
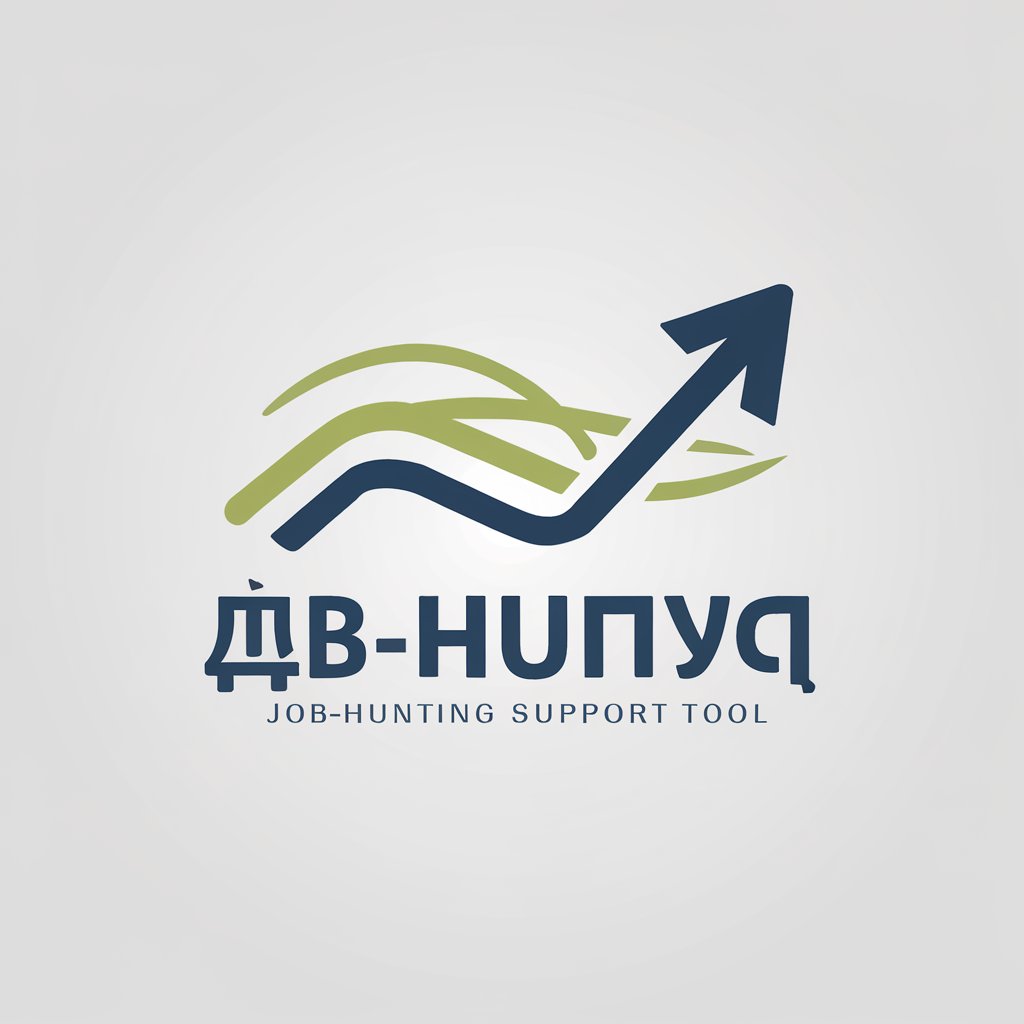
N1 成就者
AI-powered JLPT N1 Mastery

就業規則クリエイター
Automate your employment regulations creation with AI
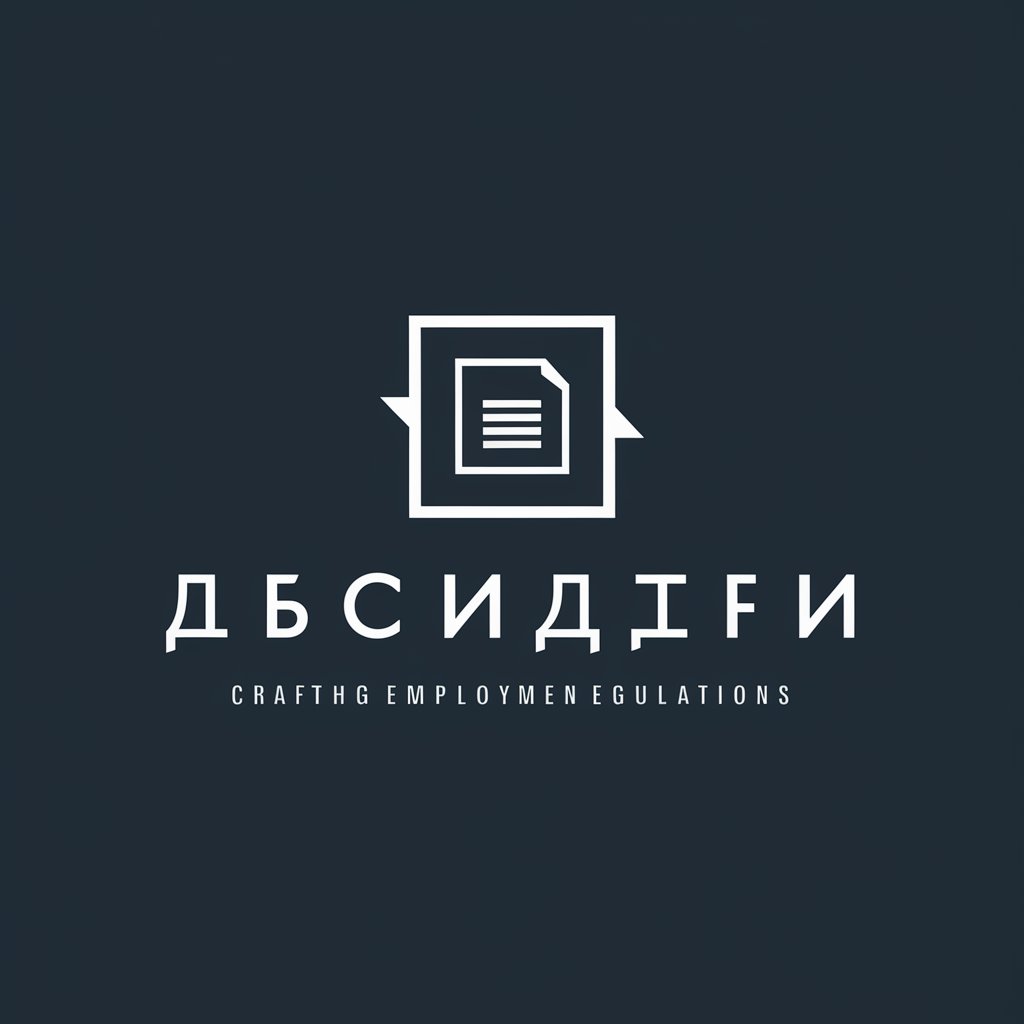
就業規則作成アシスタント
Automate your employment rules creation with AI
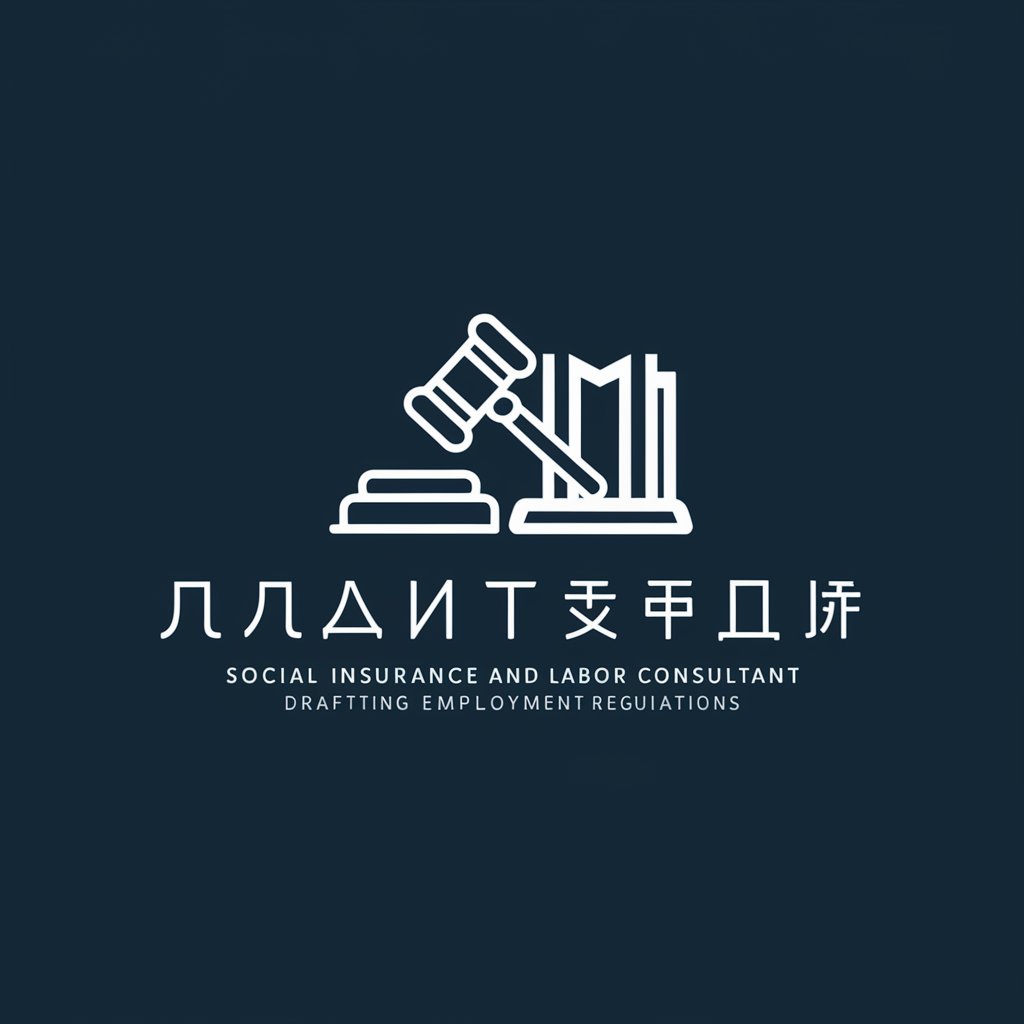
學習歷程就問我
Tailoring your academic journey with AI
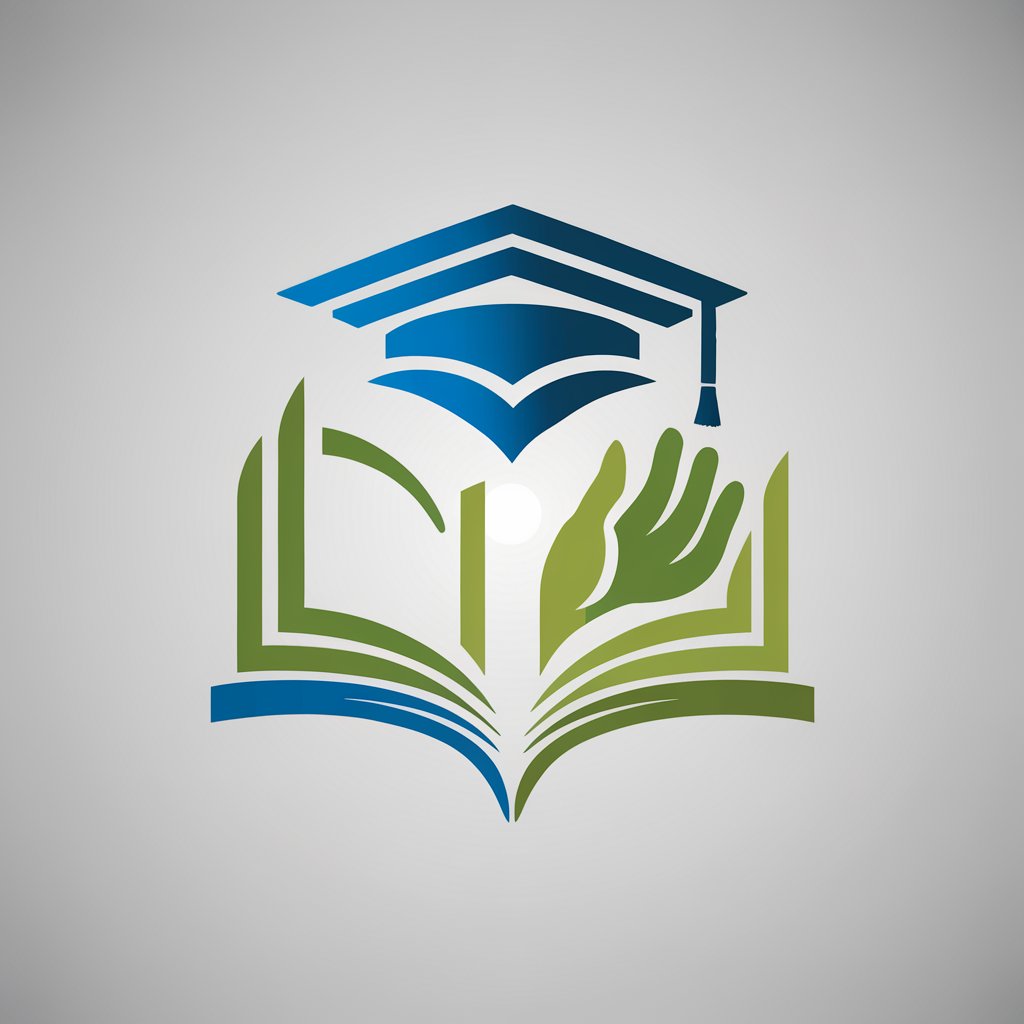
医用抗菌涂料
Enhancing Surfaces with AI-Powered Protection

Frequently Asked Questions about the Repair System Assistant
How do I add a new equipment type?
Navigate to the Equipment Management section, select 'Equipment Type', and use the 'Add New' option to input the type name and code.
Can I edit the operational hours for a piece of equipment?
Yes, go to Operational Time Management, find the specific equipment, and update the operational hours directly in the system.
What should I do if I need to retire a piece of equipment?
In the Equipment List section, select the equipment to retire and use the 'Delete' function. Ensure you record the reason for retirement for audit purposes.
How can I access the equipment maintenance plan?
Maintenance plans are accessible under the 'Annual Equipment Maintenance' section. You can view, edit, and update plans as required.
Is it possible to generate reports on equipment downtime?
Yes, the system offers detailed reports on equipment downtime, including MTBF and MTTR metrics, through the 'Report Management' section.